Топливная система дизельного двигателя автомобиля: устройство и принцип работы
У многих из нас дизельные двигатели ассоциируются в первую очередь с шумными моторами, которые не отличаются должностными мощностными показателями. Однако современные дизели благодаря использованию автоматических систем управления и измененному принципу работы существенно прибавили в показателях мощности, избавились от характерной дрожи и своего тракторного звука. Неудивительно, что с учетом отличной тяги и топливной экономичности дизельные моторы сегодня пользуются все большей популярностью. В этой статье мы поговорим с вами о том, что представляет собой топливная система дизельного двигателя и что такое ТНВД.
Устройство
Дизели используют свойство солярки воспламеняться при высоком давлении. Именно поэтому особенностью устройства топливной системы у дизелей является наличие необходимости поддерживания высокого давления в системе.

Устройство топливной системы состоит из следующих элементов:
- Фильтр грубой и тонкой очистки;
- Топливный бак;
- Подкачивающий насос;
- Топливный насос высокого давления;
- Форсунки.
В зависимости от конкретной модификации силового агрегата топливная система дизельного двигателя может иметь различные дополнительные элементы. Автовладельцу лишь необходимо знать какая компрессия должна быть в моторе его автомобиля.
Устройство системы питания у дизельного двигателя отличается простотой.
Принцип работы следующий:
- Из бака топливо при помощи топливного насоса высокого давления и дополнительного подкачивающего насоса помпового или шестеренчатого типа заканчивается в систему, проходя первоначально через фильтр грубой очистки, в котором из топливной смеси удаляются крупные включения.
- Непосредственно перед топливным насосом располагается уже фильтр тонкой очистки.
- Топливо через форсунки попадает в цилиндры, где под действием высокого давления, которое возникает за счет движения поршней, воспламеняется, что и приводит в движение поршни и коленвал.
ТНВД
За создание в системе колоссального давления отвечает ТНВД. Для начала разберем, что такое ТНВД. Большинство модификаций таких топливных насосов высокого давления приходит в движение от вращающегося вала, который связан с распредвалом. Конструкция топливного насоса высокого давления состоит из нескольких секций, число которых соответствует количеству цилиндров.
Подобная сложная конструкция этого узла обуславливает высокую стоимость этой запчасти. Поэтому ремонт ТНВД приводит к существенным затратам автовладельца.
Непосредственно за подачу топлива в ТНВД отвечает подкачивающий насос, который забирает солярку из топливного бака. За дополнительное увеличение давления в системе отвечает специальный плунжер, который конструктивно находится за насосом высокого давления. Этот плунжер нагнетает топливо в форсунки, которые распыляют мельчайшие частички солярки внутри камеры сгорания.
Следует сказать, что использование сразу нескольких фильтрующих элементов обусловлено зависимостью долговечности и беспроблемности эксплуатации силового агрегата от качества используемого топлива. Именно поэтому вопросам качества используемой солярки необходимо уделить должное внимание.
Сегодня не редкость изготовление топлива с большим содержанием серы. Удалить из топлива такую серу с помощью фильтрующих элементов невозможно. Тогда как такая сера в солярке приводит к появлению нагара в топливной системе дизельного двигателя.
Форсунки
Большинство современных моделей дизелей используют специальные форсунки высокого давления, которые позволяют максимально качественно распрыскивать топливную смесь внутри цилиндра. Следует сказать, что чем мельче частички топливной смеси, тем устойчивее работа силового агрегата.
Современные форсунки изготавливаются с многочисленными отверстиями, поэтому распыление топливной смеси происходит во всех направлениях равномерно. Такие форсунки в процессе эксплуатации автомобиля могут выходить из строя, что приводит к необходимости их замены.
Причиной выхода из строя форсунок может также стать некачественная солярка, тогда как стоимость таких запчастей может находиться на достаточно высоком уровне.
Подача топлива в камеру сгорания выполняется форсунками под колоссальным давлением. В том числе и за счет такого высокого давления создаваемого форсунками происходит воспламенение топливной смеси.
“Именно в высоком давлении в системе и состоит основное отличие дизельного силового агрегата от бензинового мотора. Если в бензиновых силовых агрегатах воспламенение бензина происходит за счет искры от свечей зажигания, то в дизелях смесь воспламеняется самостоятельно за счет высокого давления.
Турбины
Большинство модификаций современных моторов используют дополнительные турбины, которые позволяют существенно повысить мощность силового агрегата. Отдельные силовые агрегаты оснащаются двумя, тремя и даже четырьмя такими турбинами. Использование таких небольших по объему нагнетателей позволяет одновременно улучшить показатели мощности и избавляет от характерной турбоямы, которая проявляется в существенной задержке ускорения при нажатии на педаль газа.
Современные турбированные дизели по мощности даже превосходят атмосферные бензиновые силовые агрегаты. При этом, по показателям топливной экономичности, они на 20-30% лучше, нежели чем бензиновые моторы.
В то же время следует сказать, что наличие турбины может отрицательно сказаться на показателях надежности силового агрегата. Во время работы турбина может вращаться с высокой скоростью, и при этом на этот узел неизменно приходится повышенная нагрузка. Поэтому не редкость поломки, которые вызваны усталостью этого узла, а также использованием некачественного масла.
Следует сказать, что устройство турбины дизельного двигателя отличается повышенной сложностью, и в большинстве случаев устранение таких неполадок заключается в замене вышедшего из строя элемента.
Тюнинг
Чип тюнинг дизельных двигателей может выполняться как путем перепрограммирования блока управления, так и за счет изменения давления турбины.
Следует сказать, что чип тюнинг дизельного двигателя отличается простотой и имеет доступную стоимость. При этом он позволяет существенным образом увеличить показатели мощности мотора без снижения его ресурса работы.
Отметим, что для качественной работы такого чипованного силового агрегата необходимо удалить катализаторы или поставить их обманки. Следует помнить о том, что чип тюнинг дизельного двигателя должен выполнять исключительно опытный специалист, который знает, какая компрессия должна быть в моторе.
В настоящее время существуют различные программы увеличения мощности силового агрегата путем перепрограммирования его блока управления. В данном случае имеется возможность как легкого тюнинга, так и кардинальное увеличение мощности.
Топливная аппаратура — Википедия
Материал из Википедии — свободной энциклопедии
Текущая версия страницы пока не проверялась опытными участниками и может значительно отличаться от версии, проверенной 20 августа 2014; проверки требуют 6 правок. Текущая версия страницы пока не проверялась опытными участниками и может значительно отличаться от версии, проверенной 20 августа 2014; проверки требуют 6 правок.Эта статья о топливной аппаратуре поршневых двигателей внутреннего сгорания.
Топливная аппаратура это общее название систем, снабжающих двигатель топливом. Топливная аппаратура является неотъемлемой частью автомобиля, как с бензиновым так и с дизельным двигателем. Часть механизмов топливной аппаратуры крепится непосредственно к двигателю.
Карбюратор[править | править код]
основная статья: Карбюратор
В настоящее время встречается только на старых машинах. В России устанавливались на легковые машины до 2005 года, а двигатели мотоциклов, бензопил, мобильных электрогенераторов оснащаются карбюраторами и в настоящее время.
Инжектор[править | править код]
основная статья: Инжекторная система подачи топлива
Инжекторная система подачи топлива начала широко внедряться в автомобилестроение с середины 80-х годов, первые же образцы относятся ещё к концу 1950-х (разработки в то время велись в СССР, США, ФРГ). В настоящее время наиболее распространенная топливная аппаратура бензиновых моторов. Достоинства: высокий кпд, надёжность, но довольно низкая ремонтопригодность в домашних условиях.
ТНВД[править | править код]
основная статья: Топливный насос высокого давления
Топливные насосы высокого давления предназначены для подачи в цилиндры дизеля под определенным давлением и в определенный момент точно отмеренных порций топлива. Располагаются обычно в развале блока (для V-образных дизелей) или на боковой поверхности блока (рядные дизели). К ТНВД топливо из бака подаётся обычно дополнительным топливным насосом низкого давления (помпочка). Давление впрыска топлива создаваемое ТНВД составляет обычно 150—220 бар, в современных двигателях до 1600 бар и выше.
Насос-форсунка[править | править код]
основная статья: Насос-форсунка
Устанавливались на некоторые дизели до 70-х годов (в США и позже). В настоящее время в развитии дизелей наблюдается тенденция к возвращению установки индивидуальных насосов топлива на каждый цилиндр.
Common Rail[править | править код]
основная статья: Common Rail
В системе Common Rail насос нагнетает топливо под высоким давлением (до 2000 бар, в зависимости от режима работы двигателя) в общую топливную магистраль, из которой топливо впрыскивается в цилиндры с помощью раздельно управляемых форсунок. Наиболее современная топливная аппаратура для дизеля. Её недостаток придирчивость к качеству топлива. Достоинство — высокий КПД.
Газобаллонное оборудование становится с каждым годом все более популярным во всех носителях от «Жигулей» до «Кайенна», но наиболее популярно среди таких носителей бензиновых моторов как например «ГАЗель» и «ПАЗ».Однако среди носителей дизельных двигателей не особо популярно изза сложности и высокой себестоимостью эксплуатации.
Топливная система двигателей, работающих на газообразном топливе (LNG)
Оборудование для подачи газового топлива под высоким давлением включает в себя компрессоры, теплообменные аппараты, систему подвода газового топлива к рабочим цилиндрам, модули управления подачей газа и газовые форсунки.
На газовозах, перевозящих LNG, для повторного сжатия испаряющегося груза и для подачи газа к двигателю под высоким давлением широкое использование находят компрессоры фирмы Cryostar. Общее устройство компрессора серии 6LP250-5S-1 представлено на рисунке 4.16.
Компрессор с вертикальным расположением цилиндров имеет пять ступеней сжатия и позволяет на выходе получать газ под давлением до 30 МПа. При этом четвертая и пятая ступень объединены в одном рабочем цилиндре. Всего компрессор имеет по два рабочих цилиндра каждой ступени сжатия. Основной особенностью данного компрессора является возможность работать в широком диапазоне температур газа на всасывании от –160 до –40°C. Это достигается тщательным подбором материалов и рядом оригинальных конструктивных решений. Учитывая, что количество испарений из танков может меняться в широких пределах, на судне устанавливается по два компрессора, каждый из которых в состоянии обеспечить полностью потребности двигателя. Кроме того, каждый компрессор имеет возможность уменьшить свою производительность вдвое путем отключения половины рабочих цилиндров с помощью перепускных клапанов, приводимых в действие сжатым азотом.
Наибольший пик выделения газовых испарений приходится на грузовые операции, когда главный двигатель вообще не потребляет топлива, в этот момент компрессоры работают на сжижение. При движении судна часть газов отводится на питание главного двигателя, а неиспользованное топливо повторно сжижается и возвращается в грузовые танки.
На судах, не предназначенных для перевозки газов, энергетические установки которых переоборудованы на газовое топливо, перевозимое на борту в специальных емкостях, используются рядные газовые компрессоры с горизонтальным расположением цилиндров. Поперечный разрез такого компрессора серии HPP3 60/110 фирмы Cryostar представлен на рисунке 4.17. Данные компрессоры позволяют получить давление на выходе от 15 до 30 МПа. Величина давления подводимого топлива зависит от режима работы двигателя. Компрессоры данного типа отличаются большой эффективностью. Главным образом это достигается за счет малых механических потерь и хорошей теплоизоляции рабочего цилиндра, включающей вакуумную теплоизолирующую камеру.
После охлаждения газа в теплообменнике он поступает в газовую магистраль питания двигателя, которая одновременно выполняет функции аккумулятора давления.
Все газопроводы на двигателе выполняются цельносварными, и только в местах присоединения трубок, отводящих газовое топливо на блоки управления подачей, используются фланцевые соединения, необходимые для обслуживания элементов газовой системы. Конструкция трубопроводов спроектирована таким образом, чтобы компенсировать тепловые расширения при нагреве двигателя. Все трубы газовой системы рассчитаны на давление, превышающее рабочее на 50%, а во время заводских испытаний их опрессовывают давлением на 150% выше рабочего. Все газовые трубы помещаются в защитные оболочки, способные выдержать давление, которое может возникнуть при разрыве основной магистрали. Внутреннее пространство между оболочкой и трубопроводом соединяется с системой принудительной вентиляции, которая в течение часа обеспечивает примерно 30-кратную смену воздуха. К вентилируемым относятся и полости, прилегающие к основным элементам топливной системы, в которых может возникнуть утечка газа. На выходе из системы вентиляции устанавливается датчик наличия газа, соединенный с системой аварийной сигнализации. Расположение трубопроводов подобрано так, чтобы они не были повреждены в случае падения тяжелых предметов при ремонте и обслуживании двигателя. В остальном меры безопасности такие же, как и в рассмотренных ранее установках с четырехтактными газодизельными двигателями.
Фрагмент газовой магистрали представлен на рисунке 4.18.
Для повышения безопасности эксплуатации двигателей в составе энергетической установки предусмотрена система инертных газов, которая позволяет под давлением 0,4…0,8 МПа продуть как всю систему подачи газового топлива, так и ее отдельные элементы. Такая очистка является обязательной процедурой при переходе на работу по дизельному циклу или при повреждении какого-либо из участков системы газоснабжения.
Как уже отмечалось, газодизельные двигатели дооборудуются системой подачи газового топлива в рабочий цилиндр. Схематически система питания газодизельного двигателя показана на рисунке 4.19а.
Из рисунка 4.19б видно, что подача газа в камеру сгорания осуществляется сразу после того, как в цилиндр подана и воспламенилась запальная порция жидкого топлива. Таким образом достигается высокая степень выгорания топлива и предотвращается опасность попадания газа через неплотности поршневых колец в подпоршневое пространство.
Все элементы управления подачей газа скомпонованы в одном модуле, который включает: газовый аккумулятор, главный отсечной клапан с гидравлическим приводом, клапаны продувки системы инертным газом, клапаны управления гидроприводом форсунок.
Сам модуль крепится к крышке цилиндра, которая имеет внутренние сверления для подвода газа от модуля управления к газовым форсункам, установленным в крышке цилиндра рядом с форсунками для впрыска жидкого топлива.
Общее устройство модуля управления подачей газа представлено на рисунке 4.20. Схема модуля и порядок его работы представлены на рисунке 4.21.
Газовое топливо из подводящей магистрали через обратный клапан поступает в аккумулятор давления, выполненный как полость в корпусе модуля управления. Емкость аккумулятора эквивалентна примерно 20 цикловым подачам газа на номинальной нагрузке.
Наличие аккумулятора в блоке управления служит для уменьшения падения давления в процессе впрыска топлива. Стабильное давление необходимо, чтобы система управления могла правильно определить время впрыска, которым и задается величина цикловой подачи.
При отсутствии управляющего сигнала на блок управления главным отсечным клапаном последний закрыт и газ не поступает к газовым форсункам (рис. 4.21а). При поступлении электрического сигнала с блока управления двигателем на блок управления главным отсечным клапаном его золотник перемещается и подает управляющее масло на механизм гидропривода главного отсечного клапана. Клапан открывается, и газ поступает к форсункам, игольчатые клапаны которых на этот момент остаются закрытыми (рис. 4.21б). Заполняя каналы между модулем и форсунками, газ воздействует на датчик давления. Информация о фактическом давлении, полученная с датчика, поступает на блок управления двигателем и используется при вычислении необходимого времени открытия форсунки для обеспечения заданной величины цикловой подачи.
На основании полученной информации блок управления формирует сигнал, подаваемый на блок управления гидроприводом форсунок. Под действием сигнала золотник блока перемещается и подает управляющее масло на привод форсунок (рис. 4.21в). Открываясь, форсунки производят подачу газа в камеру сгорания двигателя.
После снятия управляющего сигнала с блока управления гидроприводом форсунок золотник, перемещаясь, переключает масло из контура гидропривода на слив, в результате чего клапаны форсунок закрываются и подача топлива прекращается (рис. 4.21г).
Снятие сигнала с блока управления главным отсечным клапаном приводит к его закрытию, и система возвращается в исходное состояние (рис. 4.21а).
В рассмотренной схеме подачи газа в рабочий цилиндр применено двухступенчатое подключение — сначала через главный отсечной клапан, а затем через клапаны форсунок. Такое решение позволяет повысить уровень безопасности эксплуатации, а в случае необходимости, очистить поврежденные полости, продув их через специальные клапаны инертными газами.
Общее устройство газовой форсунки представлено на рисунке 4.22.
Устанавливаются газовые форсунки по две на цилиндр в специальных колодцах, выполненных в крышке цилиндра и расположенных в непосредственной близости от форсунок жидкого топлива. Газ подводится к форсунке через сверления в крышке цилиндров и поступает к запорному конусу игольчатого клапана через отверстия в ее корпусе. Для предотвращения утечек газа между корпусом форсунки и крышкой цилиндра устанавливаются уплотнительные кольца. Полости, расположенные за пределами уплотнений, соединяются с общей вентиляционной системой.
В закрытом состоянии игольчатый клапан удерживается за счет усилия пружины, действующей на тарелку, выполненную с ним как одно целое. В нижней части игольчатого клапана имеется бурт, прецизионно подогнанный к корпусу, выполняющий роль гидравлического поршня. По каналам в направляющей и в теле игольчатого клапана масло от модуля управления подачей поступает в кольцевую полость под буртом, заставляя игольчатый клапан открываться. Для предотвращения просачивания газа между игольчатым клапаном и корпусом распылителя в зазор между ними постоянно подается специальное уплотняющее масло под давлением на 0,2…0,3 МПа выше, чем давление газа перед распылителем. Уплотняющее масло поступает по системе каналов в кольцевую проточку на теле игольчатого клапана.
Похожие статьи
Аккумуляторная топливная система — Википедия
Аккумуляторная топливная система или система типа «коммон-рэйл» (англ. common rail — общая магистраль) — система подачи топлива, применяемая в дизельных двигателях. В системе типа common rail насос высокого давления нагнетает дизельное топливо под высоким давлением (до 300 МПа, в зависимости от режима работы двигателя) в общую топливную магистраль существенного объёма (аккумулятор)[1].
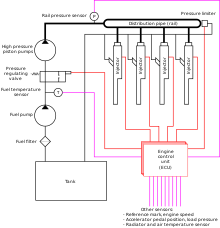
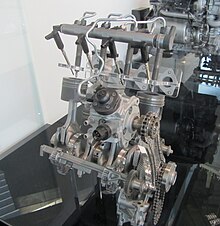
Управляемые электроникой электрогидравлические форсунки с электромагнитным или пьезоэлектрическим приводом управляющих клапанов впрыскивают дизельное топливо под высоким давлением в цилиндры. В зависимости от конструкции форсунок и класса двигателя, может впрыскиваться до 9 порций топлива за 1 цикл.
Одной из ключевых особенностей систем common rail является независимость процессов впрыскивания от угла поворота коленчатого вала и от режима работы двигателя, что делает возможным достижение высокого давления впрыскивания на частичных режимах, что необходимо для удовлетворения современных и перспективных экологических требований.
Топливо из топливного бака забирается топливоподкачивающим насосом (низкого давления), и через топливный фильтр поступает в топливный насос высокого давления (ТНВД). ТНВД подаёт топливо в напорную магистраль, которая играет роль аккумулятора давления. Блок управления регулирует производительность ТНВД для поддержания необходимого давления в магистрали по мере расхода топлива.
Топливная магистраль соединяется топливопроводами с форсунками. В каждую форсунку встроен управляющий клапан — электромагнитный или пьезоэлектрический. По команде от блока управления клапан открывается, впрыскивая необходимую порцию топлива в цилиндр.
Сравнение с другими системами подачи топлива[править | править код]
Особенности:
- В отличие от традиционной системы подачи топлива, используется одноканальный ТНВД, постоянно подающий топливо в магистраль;
- Необходимо корректировать цикл работы исходя из пропускной способности каждой форсунки, из-за чего требуется настройка электронного блока после каждой замены форсунок.
Преимущества:
- Давление, при котором происходит впрыск топлива, можно поддерживать вне зависимости от скорости вращения коленчатого вала двигателя и оно остаётся практически постоянно высоким в течение всего цикла подачи топлива, что особенно важно для стабилизации горения на холостом ходу и на малых оборотах при работе с частичной нагрузкой;
- При использовании аккумуляторной системы подачи топлива момент начала и конца подачи может в широких пределах регулироваться ЭБУ. Это позволяет более точно дозировать топливо, а также осуществлять подачу топлива несколькими порциями в течение рабочего цикла — для более полного сгорания топлива;
- Конструкция common rail проще, чем у системы ТНВД с форсунками, её ремонтопригодность выше.
Недостатки:
- Более сложные форсунки, которые требуют относительно частой замены, по сравнению с традиционной системой подачи топлива;
- Система перестаёт работать при разгерметизации любого элемента высокого давления, например, при неисправности одной из форсунок, когда её клапан постоянно находится в открытом положении;
- Более высокие требования к качеству топлива, чем у традиционных систем.
Таким образом, для удовлетворения перспективных экологических нормативов, таких как Euro-VI, Tier-IV, Euro Stage IV для тяжёлых дизелей, системы common rail были признаны наиболее подходящими для дизелей всех классов.
На данный момент до 70 % всех выпускаемых дизельных двигателей оснащается системами common rail, и эта доля растёт[2]. По прогнозам компании Robert Bosch GmbH доля системы CR на рынке к 2016 году достигнет 83 %, а в 2008 году их число составляло лишь 24 %. Таким образом, сегодня практически каждый производитель двигателей всех классов: от малых легковых и до крупных судовых, освоил применение аккумуляторных систем.
Среди производителей топливоподающей аппаратуры и систем common rail в частности, лидерами являются следующие компании: R. Bosch, Denso, Siemens VDO, Delphi, L’Orange, Scania.
В 1934—1935 годах был сконструирован, а в 1936 году показан на авиашоу в Париже дизельный двигатель Коатален (L. Coatalen). Отличием дизеля Коаталена от иных дизелей был впрыск топлива в цилиндры не гидравлическим открыванием клапана форсунки, а механическим открыванием и применением гидроаккумулятора, топливо в который нагнетается независимым от распределительной системы ТНВД. Фактически был показан работоспособный двигатель, на котором был применён прообраз системы common rail. Такой системой впрыска топлива Луи Коатален обогнал время на 60 лет[3][4].
Впервые система непосредственного впрыска топлива на дизельных двигателях была разработана и внедрена в 1939 году советскими инженерами при создании двигателя семейства В-2 на Харьковском паровозостроительном заводе.
Прототип системы common rail был создан в конце 1960-х годов Робертом Хубером в Швейцарии, далее технологию разрабатывал доктор Марко Гансер из Швейцарской высшей технической школы Цюриха.
Разработки электронно управляемых аккумуляторных систем питания дизельных двигателей и электро-гидравлических форсунок проводились ещё в 60-80 годах XX века в СССР в лаборатории автоматики и систем питания ДВС Коломенского филиала ВЗПИ под руководством профессора Ф. И. Пинского. Первые в мире работоспособные электронно-управляемые аккумуляторные топливные системы дизелей были реализованы на дизелях Коломенского Завода и НПО Звезда (г. Ленинград). Отсутствие производства в СССР малогабаритных электромагнитных исполнительных устройств для форсунок не позволило применить тогда эти системы на автомобильных дизелях. Электронно-управляемые аккумуляторные топливные системы дизелей в документах для служебного пользования фирмы R.Bosch до 1988 года имели обозначение «русские топливные системы», так как описание таких систем, разработанных в Коломне, существовало только на русском языке[5][6].
В середине 1990-х годов доктор Шохей Ито и Масахико Мияки из корпорации Denso разработали систему common rail для коммерческого транспорта и воплотили её в системе ECD-U2, которая стала использоваться на грузовиках Hino Rising Ranger; в 1995 году они продали технологию другим производителям. Поэтому Denso считается пионером в адаптации системы common rail к нуждам автомобилестроения.
Современные системы common rail работают по тому же принципу. Они управляются блоком электронного управления, который открывает каждый инжектор электрически, а не механически. Эта технология была детально разработана общими усилиями компаний Magneti Marelli, Centro Ricerche Fiat и Elasis. После того как концерн Fiat разработал дизайн и концепцию системы, она была продана немецкой компании Robert Bosch GmbH для разработки массового продукта. Это оказалось большим просчетом Fiat, поскольку новая технология стала очень выгодна, но в то время итальянский концерн не имел финансовых ресурсов для завершения работ. Тем не менее, итальянцы первые применили систему common rail в 1997 году на Alfa Romeo 156 1.9 JTD, и только потом она появилась на Mercedes-Benz C 220 CDI.
- ↑ Л. В. Грехов, Н. А. Иващенко, В. А. Марков. Топливная аппаратура и системы управления дизелей: Учебник для вузов. — М.: Легион-Автодата, 2004. — 344 с. — 2500 экз. — ISBN 588850187-5.
- ↑ Large Engine Injection Systems for Future. Christoph Kendlbacher, Peter Mueller, Martin Bernhaupt, Gerhard Rehbichler. Bergen : CIMAC, 2010. Full paper #50.
- ↑ Т. М. Мелькумов. Авиационные дизели. — М.: Воениздат, 1940. — С. 198—205. — 252 с.
- ↑ Coatalen Diesel Aero Engine (англ.). Peter & Rita Forbes’ Engine Webpages. Дата обращения 12 декабря 2019.
- ↑ А. Д. Блинов, П. А. Голубев, Ю. Е. Драган и др. Современные подходы к созданию дизелей для легковых автомобилей и малотоннажных грузовиков / под ред. В. С. Папанова И А. М. Минеева. — М.: Инженер, 2000. — С. 124. — 332 с. — ISBN 5-8208-0027-3.
- ↑ Ф. И. Пинский, Р. И. Давтян, Б. Я. Черняк. Микропроцессорные системы управления автомобильными двигателями внутреннего сгорания. — учебное пособие. — М.: Легион-Автодата, 2002. — 136 с. — ISBN 5-88850-129-8. — ISBN 978-5888501290.
Топливная система предназначена для приема, хранения, очистки и своевременной подачи топлива в цилиндры двигателя. В состав топливной системы входят: топливные цистерны, топливоперекачивающий и топливоподкачивающий насос низкого давления, фильтры грубой и тонкой очистки, подогреватели топлива, топливные сепараторы, подогреватели сепараторов, топливный насос высокого давления, топливные форсунки и топливные трубопроводы. На рис. 172 показана принципиальная схема топливной системы. Топливо из запасной цистерны 3 основным топливоперекачивающим насосом 2 подается в расходную цистерну 7. Расходная цистерна располагается выше двигателя для обеспечения подпора, она оборудована переливной трубой 6, указателем уровня 8 и сливным краном 9. Топливо из расходной цистерны, пройдя спаренный фильтр грубой очистки 10, топливоподкачивающим насосом 11 подается через спаренный фильтр тонкой очистки 12 к топливным насосам высокого давления 13, а последние нагнетают через трубопроводы высокого давления 15 и щелевые фильтры 16 топливо к форсункам 17. Рециркуляционный трубопровод 14 обеспечивает отвод излишнего топлива (отсечное топливо насосов высокого давления), а трубопровод 18 отвод топлива, просочившегося через неплотности форсунок и насосов, в сточную цистерну 19. Предохранительный клапан 20 осуществляет перепуск излишнего топлива в расходную цистерну. При сильном загрязнении водой и механическими примесями через сепаратор 21 пропускается топливо, предварительно нагретое в подогревателе 22. Прием топлива осуществляется через палубные втулки 5 правого и левого бортов и трубопровод 4. Резервный ручной насос — 1. При работе двигателя на тяжелом топливе устанавливается еще цистерна пускового (легкого) топлива для запуска и маневров главного двигателя. Для удаления отстоя из запасной цистерны используется ручной зачистной насос 23. Цистерны основного запаса топлива обычно располагают в междудонном пространстве, их емкость должна обеспечивать запас топлива для заданной автономности плавания. Расходные цистерны устанавливают попарно, причем одна из них может быть отстойной. Все топливные цистерны оборудуют вентиляционными трубами, дистанционными указателями уровня, необходимой арматурой, горловинами для осмотра и ремонта. При работе двигателя на тяжелом топливе все цистерны имеют паровой обогрев. Топливоперекачивающие насосы служат для приема топлива из-за борта; в случае необходимости выдачи топлива на другое судно осуществляют перекачку топлива из одних цистерн в другие и подачу его в расходные цистерны. Топливоперекачивающие насосы выполняют шестеренного, винтового и центробежного типов. Топливоподкачивающие насосы служат для обеспечения избыточного давления топлива, подаваемого к всасывающей полости насосов высокого давления. По конструкции эти насосы бывают: плунжерные, шестеренные и коловратные. Топливоподкачивающие насосы приводятся в действие от коленчатого и распределительного вала. Схема плунжерного топливоподкачивающего насоса показана на рис. 173. В процессе транспортировки и хранения происходит загрязнение и обводнение топлива, поэтому его фильтрация является необходимым условием для обеспечения надежной работы топливной аппаратуры и уменьшения износа ее трущихся частей. Топливные фильтры подразделяются на фильтры грубой очистки, которые устанавливают перед топливоподкачивающими насосами, фильтры тонкой очистки, устанавливаемые перед насосом высокого давления, и щелевые фильтры, устанавливаемые непосредственно перед форсункой или вмонтированные в форсунку. С помощью фильтров достигается высокая эффективность очистки топлива, простое обслуживание и легкость замены фильтрующих элементов. Обычно фильтры выполняют спаренными, что обеспечивает чистку или замену одного из элементов фильтров при работе другого. Фильтрующая поверхность грубых фильтров состоит из металлических сеток или набора металлических пластин со щелями. Для фильтров тонкой очистки фильтрующим элементом являются металлические пластины с уменьшенными зазорами, а также бумажные, войлочные, фетровые и капроновые сменные вставки. На рис. 174 показаны топливные фильтры грубой очистки: а — щелевой и б — сетчатый. В корпусе 5 расположен фильтрующий элемент 4 в виде набора пластин или сеток, стянутых специальным пустотелым болтом 3. Топливо поступает с наружной стороны фильтрующего элемента и, пройдя его, попадает в центральный канал смежного болта и затем выходит из фильтра. Спускная пробка 6 обеспечивает удаление осевшей на дно фильтра грязи. Корпус фильтра закрывается крышкой 2, вентиляционный винт 1 обеспечивает удаление воздуха из системы при заполнении ее топливом. Тонкая очистка топлива достигается с помощью специальных фильтров и сепараторов. Применяя сепараторы, из топлива можно удалить воду и механические частицы размером до 3—10 мкм. Работают сепараторы на принципе центробежной силы. В процессе сепарирования топливо распыляется на мельчайшие частицы при этом происходит удаление воды и примесей. Для лучшего сепарирования вязкие топлива предварительно подогревают. |