как работает, как ломается, как восстанавливают
Категория: Полезная информация.
Топливный насос высокого давления (ТНВД) — самый сложноустроенный и дорогостоящий элемент топливной системы дизельных двигателей.
Назначение этого узла — подавать топливо под большим давлением в форсунки (или топливную рампу, затем в форсунки), откуда оно затем будет впрыскиваться в цилиндры. Поэтому при возникающих неисправностях с ТНВД владельцу грозят серьёзные проблемы со стабильной работой мотора или тот просто откажется заводиться.
Принцип работы ТНВД
Основная задача ТНВД — нагнетать под давлением порядка 500-1400 бар (зависит от конструкции и типа насоса) топливо и подавать его к форсункам, которые открываются в нужный момент и быстро выпускают (распыляют) топливо в цилиндр.
Поддержание высокого давления в системе — другое важнейшее назначение ТНВД, ведь без этого форсунка не сработает и опоздает с распылением горючего до мельчайших частиц, а ведь мгновенное смешивание распыляемого ДТ и воздуха является условием образования однородной топливовоздушной смеси. Другими словами — гарантирует стабильную и культурную работу дизельного двигателя.
Изначально ТНВД выполнял практически все функции по подаче топлива в цилиндры: создавал давление, нагнетал топливо и распределял его по форсункам. Так действовали насосы рядного и распределительного типа.
Затем появилась система впрыска Common Rai
В системе Common Rail, таким образом, топливо подаётся ко всем форсункам одновременно, из общей магистрали под давлением порядка 1 600 – 1 800 бар.
Конструкция топливной рампы CR такова, что топливо, которое ТНВД в неё нагнетает, не запирается в рампе: излишки отводятся через сливной канал. Так обеспечивается циркуляция ДТ в системе, но как только электрический клапан форсунки открывается, топливо распыляется в цилиндр. И по-прежнему высокое давление играет важную роль в мгновенном приготовлении топливовоздушной смеси и последующем полном её сгорании.
Плунжерная пара — главный узел в конструкции ТНВД
Наиболее распространённый вид ТНВД для систем Common Rail — плунжерный. Основный рабочий элемент такого ТНВД — плунжерная пара: поршень (плунжер) и цилиндр (втулка, стакан).
Подпружиненый плунжер двигается благодаря кулачковому валу внутри втулки, набирая и выталкивая из полости над ним топливо. Высокое давление в системе обеспечивает прецезионное сопряжение: минимальный, точно выверенный зазор в 1-3 мм между плунжером и стаканом.
Часто в один корпус ТНВД устанавливают три плунжера. В полости над плунжером размещаются односторонние клапаны — на впуск и на выпуск топлива. Можно провести аналогию плунжерной пары ТНВД с сердцем, которое перекачивает кровь по организму похожим образом.
Важно. Плунжер во время работы смазывается топливом, которое через него проходит.
Конструкция разных видов плунжерных пар отличается. Встречаются ТНВД с плунжерными парами, где плунжер извлекается из корпуса и меняется в сборе.
Основные виды ТНВД
Существует три типа ТНВД.
Рядные и распределительные относятся к ТНВД предыдущих поколений автомобилей, имеют относительно простую конструкцию, не отличаются повышенной чувствительностью к качеству топлива. Среди недостатков — сравнительно шумная работа и высокие потери на трение, особенно у рядных ТНВД.
В системах впрыска Common Rail используются магистральные насосы. Они способны создавать высокое давление и обеспечивать наиболее эффективный впрыск, но весьма привередливы к качеству топлива и дороги в обслуживании и ремонте.
Рассмотрим особенности разных видов ТНВД подробнее.
Рядные ТНВД применялись на легковых автомобилях, выпущенных до 2000 года. Это неприхотливые выносливые насосы, которые смазываются моторным маслом. Количество плунжеров равно количеству цилиндров, топливо подаётся по принципу каждой камере сгорания — свой плунжер. К недостаткам относятся большие потери на внутреннее трение и недостаточно высокое давление для эффективного распыления топлива.
Распределительные ТНВД устанавливаются на дизельные двигатели с количеством цилиндров от трёх до шести. В отличие от рядных насосов, в конструкции распределительных есть только один или два плунжера, и они обеспечивают одинаковое давление при подаче топлива для всех цилиндров. Это более лёгкие компактные насосы. Работают экономичнее, культурнее и мощнее, чем рядные ТНВД. Недостаток — выше требовательность к качеству топлива.
Магистральный насос — самый современный тип ТНВД для систем впрыска Common Rail. Такой насос содержит до трёх плунжеров, а в современных типах — часто только один. Существуют магистральные насосы и роторного типа. Магистральные ТНВД созданы с высокой точностью. Они ещё легче, компактнее, имеют минимальные потери на трение, создают высокое давление и. Но плунжеры таких ТНВД смазываются топливом, поэтому насосы крайне привередливы к качеству ДТ.
Признаки неисправности ТНВД
Владельца должны насторожить такие признаки неисправностей в работе дизельного двигателя, как:
- неуверенный запуск;
- падение мощности;
- увеличение расхода топлива;
- дымный выхлоп.
В этих случаях очень рекомендуется провести комплексную компьютерную диагностику двигателя и проконтролировать параметры наддува, подачи топлива, давления в топливной системе. А также параметры работы датчиков (в частности, расходомера, датчиков положения распредвала / коленвала), системы EGR и вихревых заслонок впускного коллектора.
Такое пристальное изучение всех параметров работы мотора связано с тем, что дизельная топливная аппаратура — это не только форсунки и ТНВД, но и ряд вспомогательных и контролирующих систем.
Бывает, проблема, которую ищут в неполадках с ТНВД, кроется в другом. Например, имеет место:
- поломка подкачивающего насоса;
- грязный топливозаборник в баке;
- выход из строя насоса, перекачивающего топливо из одной части бака в другую;
- изношенный регулятор низкого давления;
- форсунка, льющая топливо в «обратку».
Внутренние поломки ТНВД и их причины
Из-за чего топливный насос высокого давления действительно может выйти из строя раньше времени — так это из-за некачественного топлива. Точнее из-за примесей в составе и попадания воды.
Примеси в составе топлива — смолы, парафины, механические взвеси, сомнительные присадки — ухудшают смазывающие свойства ДТ, что вызывает отложение на подвижных частях насоса.
Вода в случае попадания на подвижные элементы ТНВД (вместе с конденсатом с пустых стенок топливного бака или в составе некачественного ДТ), вызовет коррозию деталей. Плунжер и односторонние клапаны начнут подклинивать, нормальная циркуляция топлива нарушится, износ втулок и сальников ускорится в разы. В результате медленно, но верно, ТНВД выйдет из строя.
Если в топливной системе образовалась воздушная пробка, плунжер будет какое-то время работать без смазывания топливом, «на сухую». Механические детали от трения будут истираться друг об друга, а повышенная температура способна быстро деформировать элемент. Работа ТНВД без смазки способна убить узел в считанные минуты.
К другим, не столько фатальным, поломкам ТНВД относят:
- износ втулок вала в передней крышке корпуса;
- износ сальника вала;
- повреждение уплотнительных колец крышек корпуса / фланца;
- выход из строя регулятора давления (механической или электрической его части).
Как диагностируют и ремонтируют ТНВД
Решение сэкономить на своевременном обращении к специалистам по ремонту и обслуживанию дизельной топливной системы, «поездить пока так», обратиться к знакомым гаражникам — всё это в случае поломки ТНВД выйдет боком и сильно ударит по бюджету.
Топливный насос, точнее, его плунжерная пара — действительно дорогостоящий элемент, и не всегда его можно восстановить. Что уж говорить о самостоятельной переборке системы. Тем более что конструкция отдельных ТНВД просто неразборная.
Важно. Мастера, работающие с дизельной топливной аппаратурой, говорят, что на самом деле среди систем Common Rail «больных» ТНВД мало, чаще проблема кроется в клапане ZME, регуляторе (DRV, PCV…) высокого давления и других сопутствующих элементах. Даже если формально насос в своей работе выходит за параметры диагностического стенда, но работает нормально — нужно дважды подумать, прежде чем вскрывать его и ремонтировать.
Ремонту ТНВД обязательно должна предшествовать компьютерная диагностика, а также стендовая проверка работы форсунок. Если подтверждается, что в неполадках с работой двигателя виноват насос высокого давления, его снимают и отправляют на диагностический стенд, чтобы проверить работу узла в разных режимах «работы двигателя».
Обычно на этом этапе становится понятно, в чём проблема, каков масштаб бедствия и какие варианты исправления ситуации можно предложить владельцу.
Например, если ТНВД «приговорила» коррозия, можно попробовать его разработать (до очередного подклинивания плунжера), но лучше заменить в сборе, купив новую плунжерную пару.
Замена клапанов на новые тоже не представляет труда в случае такой необходимости. Меняют и уплотнительные кольца, и ремкомплекты.
Важно понимать, что возможность ремонта и замены отдельных элементов связана с особенностями конструкции ТНВД. В современных насосах не предусмотрены процедуры шлифовки или расточки деталей, максимум — можно заменить плунжерную пару. А в самых современных насосах системы CR и это невозможно: случись что, придётся менять весь корпус ТНВД. То есть чем моложе автомобиль, тем выше вероятность в случае поломки заменить весь узел целиком.
После проведённого ремонта и замены изношенных деталей мастер отправляет ТНВД на диагностический стенд снова. Если параметры работы выйдут за предел нормативных, насос снова разбирают, ремонтируют, проверяют.
Полностью исправный ТНВД герметично запаковывают, чтобы исключить попадание воды, и возвращают владельцу. Осталось только установить на двигатель.
Итого
Когда кого-то отговаривают от владения дизельным автомобилем, в основном аргументы «почему не стоит» сводятся как раз к дорогостоящей дизельной аппаратуре. Если речь о подержанном авто с большими пробегами, выход из строя ТНВД повлечёт за собой расходы, к которым готов не всякий автовладелец.
Чтобы не столкнуться с подобной ситуацией, не рискуйте с «паленым» топливом, не используйте присадки и добавки для чего бы то ни было, которые добавляются в бак, особенно если на автомобиле Common Rail. Держите бак по возможности полным, а при первых же признаках неисправностей в подаче топлива обращайтесь к квалифицированным специалистам.
Все эти простые меры позволят поддержать работоспособность ТНВД на нормальном уровне годами.
О том, как устроены дизельные топливные форсунки, почему они ломаются и как их ремонтируют, узнаете из этой статьи.
ТНВД найдёте в нашем каталоге
Посмотреть запчасти в наличии
Метки: Топливная аппаратура, Неисправности топливной системы, Форсунки, ТНВД
проверка, диагностика, снятие с двигателя
Топливный насос высокого давления — один из основных механизмов в системе подачи топлива в дизельных двигателях. Именно этот узел является главным отличием дизельных двигателей от своих бензиновых собратьев. Однако из-за своей сложности и чувствительности к качеству топлива топливный насос высокого давления (сокращенно ТНВД) нередко выходит из строя, что может грозить ремонтом или заменой узла.
Принцип работы ТНВД
Несмотря на обилие различных видов насосов, все ТНВД работают по сходному принципу и обеспечивает подачу порций дизельного топлива в цилиндры двигателя автомобиля под высоким давлением в строго отведенные моменты времени. Размер подаваемых порций топлива определяется нагрузкой цилиндров к коленчатому валу. Основу любого вида ТНВД составляет плунжерная пара, состоящая из непосредственно плунжера (поршня) и втулки (цилиндра).
Выделяется 2 основных разновидности ТНВД по принципу действия:
- ТНВД непосредственного действия с механическим приводом плунжера;
- ТНВД с аккумуляторным впрыском.
По устройству также различаются несколько видов ТНВД:
- рядные — секции насоса расположены в ряд и подают топливо в определенный цилиндр мотора;
- распределительные — одна секция насоса может подавать топливо в несколько разных цилиндров;
- многосекционные (V-образные) — для высокоскоростных дизельных двигателей.
В свою очередь распределительные ТНВД могут быть одноплунжерными и двухплунжерными.
Все ТНВД непосредственного впрыска работают по одному принципу:
- механический привод плунжера;
- одновременно протекающие процессы нагнетания и впрыска;
- давление для впрыска топлива создается движением плунжера.
ТНВД с аккумуляторным впрыском обеспечивают подачу топлива в раздельных циклах: сначала топливо нагнетается в аккумулятор насоса, затем поступает в топливные форсунки. Насосы с электронным управлением форсунками получили название системы Common rail.
Вкратце принцип работы топливного насоса высокого давления выглядит таким образом.
- Топливо из бака поступает в ТНВД благодаря подкачивающему насосу. Давление топлива на входе в насосную секцию ТНВД поддерживается редукционным клапаном.
- Движение плунжера, подающего топливо в цилиндры мотора, обеспечивается кулачковым валом, в свою очередь имеющим привод от коленчатого вала автомобиля.
- Вращение кулачкового вала заставляет двигаться плунжер, который поднимается вверх по втулке. При этом последовательно открываются выпускное и впускное отверстие.
- Создаваемое движением плунжера давление открывает нагнетательный клапан, после чего топливо поступает к топливной форсунке цилиндра дизельного двигателя.
- Избытки топлива через сливной, винтовой, радиальный и осевой каналы сливаются из плунжера в бак посредством дренажного штуцера.
Признаки неисправности ТНВД
ТНВД — дорогостоящий и довольно «капризный» узел дизельного двигателя, крайне требовательный к качеству топлива и смазывающих материалов. Основная причина выхода из строя ТНВД — загрязнение плунжеров насоса, которые установлены во втулки с минимальными допусками, измеряющимися в микронах. Загрязнение плунжерной пары твердыми частицами, содержащейся в некачественном дизельном топливе, может приводить к выходу ТНВД из строя. Не менее опасна и вода, которая может содержаться в топливе. Влага размывает защитную масляную пленку деталей узла, что чревато заклиниванием деталей ТНВД. Также неисправность ТНВД может заключаться в физическом износе деталей и повреждение корпуса насоса.
Неисправность ТНВД обычно приводит к неравномерности подачи топлива в форсунки двигателя и к снижению его поступающего объема. Чтобы понять то, что ТНВД не работает в штатном режиме, не обязательно ждать его поломки. Признаками проблем с ТНВД и с топливной системой в целом являются:
- повышенный расход топлива;
- нестабильная работа двигателя на малых оборотах;
- затруднения с запуском двигателя;
- перегрев мотора;
- утечка горючего;
- падение мощности и отдачи дизельного двигателя;
- увеличенная дымность выхлопа;
- появление посторонних шумов в процессе работы двигателя.
Проверка ТНВД
Симптомы неисправности насоса сходны с поломками деталей двигателя, а также могут иметь схожесть с неисправностью охлаждающей системы автомобиля. Поэтому для диагностирования поломки непосредственно ТНВД необходимо проверить и убедиться в исправности деталей насоса.
В идеале диагностика ТНВД и поиск неисправностей может проводиться только на стенде — устройстве, позволяющем имитировать работу ТНВД в рабочих диапазонах. Однако так как стоимость стенда сравнима с ценой автомобиля, а для диагностики необходимо демонтировать ТНВД с автомобиля, то такие операции проводятся только в автосервисах.
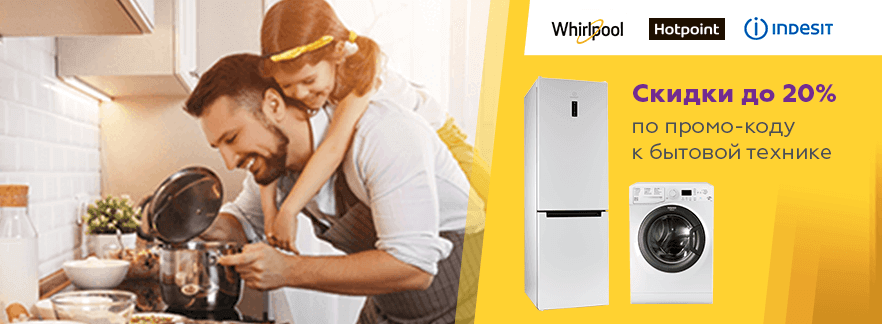
В «боевых» условиях проверить ТНВД достаточно сложно, но, все-таки возможно. Однако нужно понимать, что в домашних условиях получится диагностировать только некоторые неисправности ТНВД, а полную картину даст только проверка на стенде.
- Проверить плунжерные пары на наличие в них воды можно сняв ремень ГРМ и осторожно покрутив шкивом. Если шкив проворачивается с переменным усилием (из-за вращения кулачкового вала), то вода во втулках ТНВД отсутствует. Если шкив не проворачивается, то в системе ТНВД находится вода, что при запуске двигателя приведет к заклиниванию.
- Давление в плунжерной паре можно проверить с помощью тестера ТАД-01А, КИ-4802 или любого другого подобного инструмента. Такой прибор можно изготовить даже самостоятельно, для этого потребуется мощный манометр. Тестер вкручивается в ТНВД на место топливной трубки или в центральное отверстие головки насоса. Показатели измерения должны составлять не менее 300 кг/см2. В обратном случае плунжерная пара изношена и нуждается в замене или восстановлении.
- В дизельных автомобилях с электронным управлением ТНВД поломка может заключаться в обрыве датчика оборотов, расположенного на корпусе насоса. В таком случае топливо не поступает из ТНВД в форсунки цилиндров мотора. Для проверки датчика необходимо с помощью мультиметра измерить сопротивление на разъеме датчика, расположенного на крышке ТНВД. В случае отсутствия сопротивления произошел разрыв.
- Если неисправность ТНВД заключается в утечке топлива, то, как правило, виноваты уплотнительные кольца узла. Чтобы проверить ТНВД на утечку необходимо при работающем двигателе покачать ось рычага ТНВД. Если при этом наблюдается утечка топлива, то резиновый уплотнитель в месте утечки нужно заменить. Если утечки возникают не на оси, а в других местах узла, например, в местах посадки плунжерных пар, то для диагностики придется разбирать ТНВД.
Все эти способы помогают проверить ТНВД на наличие поломок. Однако неисправностей насоса гораздо больше, поэтому в большинстве случаев приходится демонтировать ТНВД и разбирать узел в поисках механических и иных повреждений в деталях узла.
Снятие ТНВД с двигателя
Снятие ТНВД может понадобиться не только для поиска и ремонта неисправных деталей, но и для проверки форсунок и регулировки газораспределительного механизма. Снятие ТНВД — довольно трудоемкая задача, с которой справится далеко не каждый автовладелец. Как минимум для проведения такой операции необходимо иметь немалый опыт в самостоятельном ремонте автомобиля.
Снятие ТНВД проводится в несколько этапов. В зависимости от вида насоса могут иметься различия в последовательности и некоторых деталях процесса. Для снятия ТНВД кроме стандартных ключей понадобятся специальные приспособления — шестерни для проворачивания коленчатого вала, фиксаторы, стапели, съемники приводных шестерен, шлицевые ключи и специальные приспособления для демонтажа. Поэтому при снятии насоса желательно использовать набор инструментов для ремонта ТНВД.
- Для начала следует слить всю охлаждающую жидкость в автомобиле.
- Далее отсоединяется минусовая клемма аккумулятора.
- Снимается вентилятор и кожух вентилятора, усложняющие доступ к корпусу ТНВД.
- Затем снимается крышка головки блока цилиндров.
- Далее снимается кожух ремня ГРМ.
- Затем демонтируется впускной коллектор.
- Далее первый цилиндр двигателя необходимо установить в положение верхней мертвой точки (максимальное расстояние между цилиндром и коленвалом). Для блокировки цилиндра в таком положении используется приспособление 11 2 300.
- Затем необходимо демонтировать ремень ГРМ со шкивов распределительного вала и вала ТНВД.
- Далее необходимо отсоединить топливный трубопровод и сливной провод от насоса. Также отсоединяется шланг для слива масла.
- Далее требуется отсоединить распределительные трубопроводы от форсунок цилиндров с помощью приспособления 13 5 020.
- Далее отсоединяются детали электропроводки.
- Затем нужно снять крепеж ТНВД. Для снятия центральной гайки ТНВД сначала демонтируется колпачковая гайка, а затем откручивается центральная гайка рожковым ключом на 18.
- Далее выворачиваются болты на корпусе ТНВД.
- Для отсоединения ТНВД от звездочки используется выталкивающий винт и приспособление 13 5 120, которое предварительно вкручивается на место центральной гайки. При снятии ТНВД приспособление должно оставаться на центральном шкиве до момента установки насоса обратно во избежание падения звездочки.
После того, как ТНВД отделен от центрального шкива и звездочки, его можно осторожно вынуть. Дальнейший разбор для поиска неисправных деталей также производиться с помощью специализированного набора для ремонта ТНВД.
2.2 Основные неисправности тнвд и способы их устранения
Топливную аппаратуру необходимо ремонтировать только в специальных мастерских. При разборке и сборке нужно помнить, что плунжерные пары секций ТНВД поршень и корпус насоса низкого давления, шток и втулка насоса низкого давления, поршень и цилиндр ручного топливоподкачивающего насоса представляют собой точно подобранные пары и раскомплектованию не подлежат.
Основные дефекты деталей ТНВД и способы устранения:
– корпус топливного насоса высокого давления изготавливают из сплава алюминия АЛ9, обломы и трещины, захватывающие отверстия под штуцера и подшипники и находящиеся в труднодоступных местах, являются выбраковочными признаками; все остальные трещины и обломы устраняют наплавкой или заваркой в среде аргона; износ отверстия под толкатели плунжеров устраняют обработкой под ремонтный размер, при размере этого отверстия более допустимого корпус бракуют, износ отверстия по подшипники державки грузиков устраняют гальваническим натиранием или постановкой ДРД, износ отверстия под ось промежуточной шестерни, под ось рычага реек и под ось рычага пружины устраняют постановкой ДРД с последующим развертыванием до размеров рабочего чертежа;
Детали плунжерной пары изготавливают из стали 25Х5МА.
– такой дефект, как заедание плунжера во втулке, является выбраковочным признаком; заедание отсутствует, если плунжер будет свободно опускаться в разных положениях по углу поворота во втулке при установке пары под углом 45 градусов; износ рабочих поверхностей плунжерной пары, как и следы коррозии на торцовой поверхности втулки, что ведет к потере герметичности, устраняют перекомплектовкой; для этого сам плунжер и его втулку притирают и доводят до шероховатости 0,1 мкм при допустимой овальности 0,2 мкм и конусности 0,4 мкм; затем плунжеры разбивают на размерные группы (интервал 4 мкм) и подбирают по соответствующим втулкам; далее плунжер и втулку притирают, промывают в бензине и больше не обезличивают;
– к дефектам втулки плунжера относят скалывание и выкрашивание металла у отверстий, задиры, царапины, износ рабочей поверхности, увеличение диаметра впускного и отсечного окон, трещин и ослабление в местах посадки (скалывание, выкрашивание металла и трещины являются неисправимыми дефектами). Износ рабочей поверхности втулки плунжера измерить с точностью до 0,001 мм, овальность, конусообразность и увеличение отверстия втулки – микрометрическим или индикаторным прибором для измерения внутренних поверхностей с ценой деления до 0,001 мм и конусными калибрами;
– к дефектам плунжера относят выкрашивание металла на кромках винтового паза, износ кромок паза, задиры и царапины на рабочей поверхности, износ рабочей поверхности и трещины. Искажение геометрии плунжера выявить миниметром с точностью до 0,001 мм при установке его стрелки на нуль по исходному образцу или калибром в виде конусной втулки;
– величину зазора в плунжерной паре проверить на опрессовочном стенде с падающим грузом. Перед испытанием детали пары тщательно промыть в профильтрованном дизельном топливе. Плунжерную пару установить в гнездо стенда, плунжер – в положение максимальной подачи. Надплунжерное пространство заполнить профильтрованным дизельным топливом. Установить на торец втулки уплотнительную пластину, зажав ее винтом, затем отпустить защелку груза. Под действием его через зазор в паре постепенно начинает выдавливаться топливо, и чем больше зазор, тем быстрее. Величина нагрузки на плунжер должна соответствовать величине давления топлива 195–205 кгс/см2. Полное поднятие плунжера до момента отсечки под действием нагрузки, сопровождаемое выжиманием топлива через зазоры между втулкой и плунжером, должно происходить не менее чем за 20 с. Если время поднятия плунжера до отсечки превышает 40 с, то установить смоченную профильтрованным дизельным топливом плунжерную пару в вертикальное положение на торец втулки, предварительно подложив лист чистой бумаги. После пятиминутной выдержки при поднятии пары за хвостовик плунжера втулка должна опускаться с плунжера под действием собственной массы;
– толкатель плунжера установлен в отверстие корпуса насоса с номинальным зазором 0,025–0,077 мм. Предельно допустимый зазор при эксплуатации 0,20 мм. Замерить наружный диаметр толкателя плунжера микрометром или скобой размером 30,91;
– в узле ролик толкателя – втулка ролика – ось ролика основным дефектом является износ сопрягаемых поверхностей. Номинальный суммарный зазор 0,029–0,095 мм, предельно допустимый 0,30 мм (замерить индикаторной головкой). Если износ превышает указанный предел, толкатель разобрать и отремонтировать; при этом замеры производятся раздельно.
Предельно допустимый зазор в соединении ось ролика – втулка ролика при износе поверхностей – 0,12 мм, в соединении втулка ролика – ролик толкателя – 0,18 мм. Наружные поверхности деталей замерить микрометром, внутренние – нутрометром с индикатором.
При повторной сборке толкателя сохранить величину исходного натяга (0,005–0,031 мм) в соединении ось ролика толкателя – толкатель плунжера по отверстию, в которое запрессовывается ось ролика.
Величину исходного натяга обеспечить подбором оси ролика по отверстию в корпусе толкателя из разных комплектов. Предельно допустимый наружный диаметр ролика толкателя – 19,90 мм при номинальном диаметре 19,955–20,000 мм;
– на поверхности кулачкового вала не допускаются выкрашивание металла, задиры, срывы резьб, следы коррозии. Предельно допустимая высота профиля кулачка должна быть не менее 41,7 мм при номинальной высоте 41,95–42,05 мм. Замеры производить скобой 41,7;
– диаметр шейки под внутренние кольца подшипников должен быть не менее 20 мм при номинальном диаметре 20,002–20,017 мм, натяг по уплотняющей кромке манжеты – не менее 0,50 мм;
Нагнетательный клапан в сборе с седлом изготавливают из стали ШХ -15.
– основные дефекты нагнетательного клапана: риски, задиры, следы износа и коррозия на конусных поверхностях, на направляющей поверхности и на торце седла, на разгрузочном пояске клапана устраняют притиркой на плите притирочными пастами; при этом седло клапана крепят в цанговой державке за резьбовую поверхность; шероховатость торцовой поверхности седла должна составлять Ra 0,16 мкм, а направляющего отверстия и уплотняющего конуса Ra 0,08 мкм; после подбора и притирки клапанную пару не обезличивают; отсутствие заедания клапана в седле определяется его свободным перемещением под действием собственного веса в разных положениях по углу поворота после выдвижения клапана из седла на 1/3 длинны;
– на поверхности нагнетательного клапана не допускаются трещины, вмятины, следы коррозии. Износ клапана проявляется в потере герметичности по уплотняющему конусу и в заедании клапана в седле. Для обнаружения дефектов используйте лупу десятикратного увеличения. При потере герметичности притрите совместно седло и клапан по конусу пастой с размером зерна не более 3 мкм, при заедании клапана в седле детали промыть дизельным топливом. Если заедание не устраняется, пару заменить;
– предельно допустимый зазор в сопряжении палец рычага реек – паз рейки составляет 0,18 мм при номинальном зазоре 0,025–0,077 мм, предельно допустимый зазор в сопряжении ось поводка поворотной втулки 10 (см. рис. 8) – паз рейки топливного насоса равен 0,3 мм при номинальном зазоре 0,117–0,183 мм. Для замера пазов применять нутро-метр.
Основные дефекты деталей регулятора частоты вращения и способы их устранения:
– заменить верхнюю и заднюю крышки регулятора при наличии на них трещин. Если засорен сетчатый масляный фильтр, в задней крышке регулятора продуть сетку сжатым воздухом. Если фильтр имеет дефекты, заменить его. Эксплуатационный расход масла через фильтр должен быть не менее 1,6 л/ч при давлении 1–3 кгс/см2;
– для определения пригодности к дальнейшей эксплуатации державку грузов регулятора в сборе с грузами осмотреть и измерить без разборки, так как при выпрессовке детали могут быть повреждены и может нарушиться спаренность грузов, которые подобраны с разницей статического момента не более 2 кг/см2.
Частичную или полную разборку узла производить только при износе, превышающем допустимый, или при разрушении деталей.
Зазор между рычагом пружины регулятора и осью рычага, запрессованной в корпус насоса, не должен превышать 0,3 мм. Увеличение длины пружины регулятора допускается в процессе эксплуатации до 59,5 мм при номинальной длине 57–58 мм.
Основные дефекты деталей насоса низкого давления и ручного топливоподкачивающего насоса и способы их устранения:
– насос низкого давления и ручной насос заменить при наличии трещин на корпусе, изломов, механических повреждений, коррозии, ведущей к потере подвижности сопрягаемых деталей;
– особое внимание обратить на состояние узла шток–втулка насоса низкого давления, так как от величины износа в сопряжении зависит количество перетекаемого топлива в полость кулачкового вала. Зазор в указанном сопряжении не должен превышать 0,012 м. Величину зазора проверить, не извлекая втулки из корпуса насоса, путем определения времени падения давления воздуха от 5 до 4 кгс/см2 в аккумуляторе объемом 30 см3.
2.2 Основные неисправности тнвд и способы их устранения
Топливную аппаратуру необходимо ремонтировать только в специальных мастерских. При разборке и сборке нужно помнить, что плунжерные пары секций ТНВД поршень и корпус насоса низкого давления, шток и втулка насоса низкого давления, поршень и цилиндр ручного топливоподкачивающего насоса представляют собой точно подобранные пары и раскомплектованию не подлежат.
Основные дефекты деталей ТНВД и способы устранения:
– корпус топливного насоса высокого давления изготавливают из сплава алюминия АЛ9, обломы и трещины, захватывающие отверстия под штуцера и подшипники и находящиеся в труднодоступных местах, являются выбраковочными признаками; все остальные трещины и обломы устраняют наплавкой или заваркой в среде аргона; износ отверстия под толкатели плунжеров устраняют обработкой под ремонтный размер, при размере этого отверстия более допустимого корпус бракуют, износ отверстия по подшипники державки грузиков устраняют гальваническим натиранием или постановкой ДРД, износ отверстия под ось промежуточной шестерни, под ось рычага реек и под ось рычага пружины устраняют постановкой ДРД с последующим развертыванием до размеров рабочего чертежа;
Детали плунжерной пары изготавливают из стали 25Х5МА.
– такой дефект, как заедание плунжера во втулке, является выбраковочным признаком; заедание отсутствует, если плунжер будет свободно опускаться в разных положениях по углу поворота во втулке при установке пары под углом 45 градусов; износ рабочих поверхностей плунжерной пары, как и следы коррозии на торцовой поверхности втулки, что ведет к потере герметичности, устраняют перекомплектовкой; для этого сам плунжер и его втулку притирают и доводят до шероховатости 0,1 мкм при допустимой овальности 0,2 мкм и конусности 0,4 мкм; затем плунжеры разбивают на размерные группы (интервал 4 мкм) и подбирают по соответствующим втулкам; далее плунжер и втулку притирают, промывают в бензине и больше не обезличивают;
– к дефектам втулки плунжера относят скалывание и выкрашивание металла у отверстий, задиры, царапины, износ рабочей поверхности, увеличение диаметра впускного и отсечного окон, трещин и ослабление в местах посадки (скалывание, выкрашивание металла и трещины являются неисправимыми дефектами). Износ рабочей поверхности втулки плунжера измерить с точностью до 0,001 мм, овальность, конусообразность и увеличение отверстия втулки – микрометрическим или индикаторным прибором для измерения внутренних поверхностей с ценой деления до 0,001 мм и конусными калибрами;
– к дефектам плунжера относят выкрашивание металла на кромках винтового паза, износ кромок паза, задиры и царапины на рабочей поверхности, износ рабочей поверхности и трещины. Искажение геометрии плунжера выявить миниметром с точностью до 0,001 мм при установке его стрелки на нуль по исходному образцу или калибром в виде конусной втулки;
– величину зазора в плунжерной паре проверить на опрессовочном стенде с падающим грузом. Перед испытанием детали пары тщательно промыть в профильтрованном дизельном топливе. Плунжерную пару установить в гнездо стенда, плунжер – в положение максимальной подачи. Надплунжерное пространство заполнить профильтрованным дизельным топливом. Установить на торец втулки уплотнительную пластину, зажав ее винтом, затем отпустить защелку груза. Под действием его через зазор в паре постепенно начинает выдавливаться топливо, и чем больше зазор, тем быстрее. Величина нагрузки на плунжер должна соответствовать величине давления топлива 195–205 кгс/см2. Полное поднятие плунжера до момента отсечки под действием нагрузки, сопровождаемое выжиманием топлива через зазоры между втулкой и плунжером, должно происходить не менее чем за 20 с. Если время поднятия плунжера до отсечки превышает 40 с, то установить смоченную профильтрованным дизельным топливом плунжерную пару в вертикальное положение на торец втулки, предварительно подложив лист чистой бумаги. После пятиминутной выдержки при поднятии пары за хвостовик плунжера втулка должна опускаться с плунжера под действием собственной массы;
– толкатель плунжера установлен в отверстие корпуса насоса с номинальным зазором 0,025–0,077 мм. Предельно допустимый зазор при эксплуатации 0,20 мм. Замерить наружный диаметр толкателя плунжера микрометром или скобой размером 30,91;
– в узле ролик толкателя – втулка ролика – ось ролика основным дефектом является износ сопрягаемых поверхностей. Номинальный суммарный зазор 0,029–0,095 мм, предельно допустимый 0,30 мм (замерить индикаторной головкой). Если износ превышает указанный предел, толкатель разобрать и отремонтировать; при этом замеры производятся раздельно.
Предельно допустимый зазор в соединении ось ролика – втулка ролика при износе поверхностей – 0,12 мм, в соединении втулка ролика – ролик толкателя – 0,18 мм. Наружные поверхности деталей замерить микрометром, внутренние – нутрометром с индикатором.
При повторной сборке толкателя сохранить величину исходного натяга (0,005–0,031 мм) в соединении ось ролика толкателя – толкатель плунжера по отверстию, в которое запрессовывается ось ролика.
Величину исходного натяга обеспечить подбором оси ролика по отверстию в корпусе толкателя из разных комплектов. Предельно допустимый наружный диаметр ролика толкателя – 19,90 мм при номинальном диаметре 19,955–20,000 мм;
– на поверхности кулачкового вала не допускаются выкрашивание металла, задиры, срывы резьб, следы коррозии. Предельно допустимая высота профиля кулачка должна быть не менее 41,7 мм при номинальной высоте 41,95–42,05 мм. Замеры производить скобой 41,7;
– диаметр шейки под внутренние кольца подшипников должен быть не менее 20 мм при номинальном диаметре 20,002–20,017 мм, натяг по уплотняющей кромке манжеты – не менее 0,50 мм;
Нагнетательный клапан в сборе с седлом изготавливают из стали ШХ -15.
– основные дефекты нагнетательного клапана: риски, задиры, следы износа и коррозия на конусных поверхностях, на направляющей поверхности и на торце седла, на разгрузочном пояске клапана устраняют притиркой на плите притирочными пастами; при этом седло клапана крепят в цанговой державке за резьбовую поверхность; шероховатость торцовой поверхности седла должна составлять Ra 0,16 мкм, а направляющего отверстия и уплотняющего конуса Ra 0,08 мкм; после подбора и притирки клапанную пару не обезличивают; отсутствие заедания клапана в седле определяется его свободным перемещением под действием собственного веса в разных положениях по углу поворота после выдвижения клапана из седла на 1/3 длинны;
– на поверхности нагнетательного клапана не допускаются трещины, вмятины, следы коррозии. Износ клапана проявляется в потере герметичности по уплотняющему конусу и в заедании клапана в седле. Для обнаружения дефектов используйте лупу десятикратного увеличения. При потере герметичности притрите совместно седло и клапан по конусу пастой с размером зерна не более 3 мкм, при заедании клапана в седле детали промыть дизельным топливом. Если заедание не устраняется, пару заменить;
– предельно допустимый зазор в сопряжении палец рычага реек – паз рейки составляет 0,18 мм при номинальном зазоре 0,025–0,077 мм, предельно допустимый зазор в сопряжении ось поводка поворотной втулки 10 (см. рис. 8) – паз рейки топливного насоса равен 0,3 мм при номинальном зазоре 0,117–0,183 мм. Для замера пазов применять нутро-метр.
Основные дефекты деталей регулятора частоты вращения и способы их устранения:
– заменить верхнюю и заднюю крышки регулятора при наличии на них трещин. Если засорен сетчатый масляный фильтр, в задней крышке регулятора продуть сетку сжатым воздухом. Если фильтр имеет дефекты, заменить его. Эксплуатационный расход масла через фильтр должен быть не менее 1,6 л/ч при давлении 1–3 кгс/см2;
– для определения пригодности к дальнейшей эксплуатации державку грузов регулятора в сборе с грузами осмотреть и измерить без разборки, так как при выпрессовке детали могут быть повреждены и может нарушиться спаренность грузов, которые подобраны с разницей статического момента не более 2 кг/см2.
Частичную или полную разборку узла производить только при износе, превышающем допустимый, или при разрушении деталей.
Зазор между рычагом пружины регулятора и осью рычага, запрессованной в корпус насоса, не должен превышать 0,3 мм. Увеличение длины пружины регулятора допускается в процессе эксплуатации до 59,5 мм при номинальной длине 57–58 мм.
Основные дефекты деталей насоса низкого давления и ручного топливоподкачивающего насоса и способы их устранения:
– насос низкого давления и ручной насос заменить при наличии трещин на корпусе, изломов, механических повреждений, коррозии, ведущей к потере подвижности сопрягаемых деталей;
– особое внимание обратить на состояние узла шток–втулка насоса низкого давления, так как от величины износа в сопряжении зависит количество перетекаемого топлива в полость кулачкового вала. Зазор в указанном сопряжении не должен превышать 0,012 м. Величину зазора проверить, не извлекая втулки из корпуса насоса, путем определения времени падения давления воздуха от 5 до 4 кгс/см2в аккумуляторе объемом 30 см3.
Рисунок 6. Схема установки для испытания пары шток-втулка: 1 – корпус насоса; 2 – ограничитель перемещения штока; 3 – соединитель для подвода воздуха к корпусу насоса; 4 – воздушный аккумулятор; 5 – манометр; 6, 7, 8. 9 – краны; 10 – масловлагоотделитель;/– в атмосферу;//– из системы;///– к насосу
технологический насос автомобиль
Установить корпус насоса в приспособление, заполнить аккумулятор сжатым воздухом до давления не менее 5,5 кгс/см2, герметично отключить его от магистрали сжатого воздуха и замерить время, в течение которого произойдет падение давления в аккумуляторе от 5 до 4 кгс/см2. Полученное время сравнить с аналогичными показаниями плотности эталонной прецизионной пары, имеющей зазор в сопряжении 0,012 мм. Пару заменить или отремонтировать, если плотность у нее меньше эталонной.
Если узел шток – втулка заменяется, поверхность резьбы и торец в корпусе насоса низкого давления очистить от остатков клея. Новую втулку штока установить в корпус насоса на клее, составленном на основе эпоксидной смолы. Для обеспечения прочности и герметичности соединения клеем очищенные контактирующие поверхности корпуса насоса и втулки предварительно обезжирить. После затяжки втулки штока с моментом 1 кгс-м проверить легкость перемещения штока в ней. При необходимости уменьшить момент затяжки.
После сборки проверить производительность насоса на установке, которую собрать по схеме: топливный бак – фильтр грубой очистки топлива – вакуумметр – топливоподкачивающий насос – манометр – мерный резервуар. Элементы схемы соединить прозрачными трубопроводами с внутренним диаметром не менее 8 мм. Для создания разрежения на входе в насос и противодавления на выходе установить краны.
Проверку производить, на летнем дизельном топливе при его температуре 25 – 30 °С. В отсутствии воздуха в системе убедиться по чистоте струи топлива в прозрачных трубопроводах. Насос должен засасывать топливо из бака, установленного на 1 м ниже насоса. Производительность насоса должна быть не менее 2,5 л/мин при частоте вращения кулачкового вала 1290–1310 об/мин, разрежении у входного штуцера 170 мм. рт. ст. и противодавлении 0,6 – 0,8 кгс/см2. При полностью перекрытом выходном кране и частоте вращения кулачкового вала 1290–1310 об/мин насос должен создавать давление не менее 4 кгс/см2. При полностью перекрытом входном кране и указанной частоте вращения кулачкового вала минимальное разрежение, создаваемое насосом, должно быть равно 380 мм рт. ст. Ручной топливоподкачивающий насос проверить на стенде, собранном по схеме: топливный бак – фильтр грубой очистки – топливный насос. Насос должен подавать топливо из бака, установленного ниже ручного насоса на 1 м. Проверить насос на герметичность, подводя воздух под поршень при давлении 2–3 кгс/см2в течение 5–6 секунд с предварительным смачиванием подпоршневой полости дизельным топливом.
Неисправности ТНВД, их причины и последствия
Дизельные двигатели не просты в эксплуатации, но экономичны и имеют высокий ресурс. Но и у них узлы и агрегаты периодически выходят из строя, требуя восстановления. Это также касается топливных насосов. Практика показывает, что ремонт ТНВД чаще всего требуется вследствие износа его деталей. Нередко, это происходит задолго до того, как они выработали свой ресурс. Причиной обычно является топливо, в котором содержится вода или механические примеси.
Наиболее частые неисправности
Износ деталей топливного насоса приводит к ослаблению натяжения и увеличению зазоров в сопряжениях. Происходит нарушение взаимного расположения деталей, изменяется их поверхностная твёрдость, накапливаются загрязнения. В результате, автовладельцам приходится иметь дело с различными неисправностями, в числе которых:
- Неравномерность в подаче топлива;
- Запаздывание момента начала и конца впрыска;
- Нарушение подвижности рейки, связанные с этим деформации.
- Необходимо отметить, что в работе ТНВД большую роль играют плунжерные пары.
По сути, они является основой ТНВД и их выход из строя приводит к целому ряду неприятных последствий. Довольно часто наблюдается заклинивание плунжеров. Зависая, они в свою очередь вызывают нарушение подвижности рейки.
Распространённым поводом для ремонта ТНВД является нарушение топливоподачи. Возникает данная проблема, когда выходят из строя плунжерные пары и их поводки, нагнетательные клапаны, хомутики и зубья рейки. Неисправности в топливоподаче могут быть вызваны и другими причинам. При неравномерной подаче топлива повышается его расход, а мощность двигателя снижается.
Моменты начала и конца впрыска прямо влияют на работу мотора. При износе плунжерных пар, момент впрыска может запаздывать. Помимо потери мощности и экономичности это приводит к повышению температуры, дымлению и затруднению запуска. Аналогичная проблема возникает, когда износились, например, шарикоподшипники или кулачковый вал.
Перечисленные неисправности, при отсутствии ремонта, влекут за собой выход из строя сопутствующих механизмов и могут вызвать как значительное отклонение функциональных характеристик ТНВД, так и его полный отказ. Причём, восстановление эксплуатационных качеств может быть довольно затратным. Не исключено, что потребуется полная замена насоса.
Избежать такого развития ситуации помогают профилактические меры — использование качественного топлива, регулярное техническое обслуживание, своевременная диагностика и текущий ремонт.
Основные неисправности ТНВД и способы их устранения — Мегаобучалка
Топливную аппаратуру необходимо ремонтировать только в специальных мастерских. При разборке и сборке нужно помнить, что плунжерные пары секций ТНВД поршень и корпус насоса низкого давления, шток и втулка насоса низкого давления, поршень и цилиндр ручного топливоподкачивающего насоса представляют собой точно подобранные пары и раскомплектованию не подлежат.
Основные дефекты деталей ТНВД и способы устранения:
– корпус топливного насоса высокого давления изготавливают из сплава алюминия АЛ9, обломы и трещины, захватывающие отверстия под штуцера и подшипники и находящиеся в труднодоступных местах, являются выбраковочными признаками; все остальные трещины и обломы устраняют наплавкой или заваркой в среде аргона; износ отверстия под толкатели плунжеров устраняют обработкой под ремонтный размер, при размере этого отверстия более допустимого корпус бракуют, износ отверстия по подшипники державки грузиков устраняют гальваническим натиранием или постановкой ДРД, износ отверстия под ось промежуточной шестерни, под ось рычага реек и под ось рычага пружины устраняют постановкой ДРД с последующим развертыванием до размеров рабочего чертежа;
Детали плунжерной пары изготавливают из стали 25Х5МА.
– такой дефект, как заедание плунжера во втулке, является выбраковочным признаком; заедание отсутствует, если плунжер будет свободно опускаться в разных положениях по углу поворота во втулке при установке пары под углом 45 градусов; износ рабочих поверхностей плунжерной пары, как и следы коррозии на торцовой поверхности втулки, что ведет к потере герметичности, устраняют перекомплектовкой; для этого сам плунжер и его втулку притирают и доводят до шероховатости 0,1 мкм при допустимой овальности 0,2 мкм и конусности 0,4 мкм; затем плунжеры разбивают на размерные группы (интервал 4 мкм) и подбирают по соответствующим втулкам; далее плунжер и втулку притирают, промывают в бензине и больше не обезличивают;
– к дефектам втулки плунжера относят скалывание и выкрашивание металла у отверстий, задиры, царапины, износ рабочей поверхности, увеличение диаметра впускного и отсечного окон, трещин и ослабление в местах посадки (скалывание, выкрашивание металла и трещины являются неисправимыми дефектами). Износ рабочей поверхности втулки плунжера измерить с точностью до 0,001 мм, овальность, конусообразность и увеличение отверстия втулки – микрометрическим или индикаторным прибором для измерения внутренних поверхностей с ценой деления до 0,001 мм и конусными калибрами;
– к дефектам плунжера относят выкрашивание металла на кромках винтового паза, износ кромок паза, задиры и царапины на рабочей поверхности, износ рабочей поверхности и трещины. Искажение геометрии плунжера выявить миниметром с точностью до 0,001 мм при установке его стрелки на нуль по исходному образцу или калибром в виде конусной втулки;
– величину зазора в плунжерной паре проверить на опрессовочном стенде с падающим грузом. Перед испытанием детали пары тщательно промыть в профильтрованном дизельном топливе. Плунжерную пару установить в гнездо стенда, плунжер – в положение максимальной подачи. Надплунжерное пространство заполнить профильтрованным дизельным топливом. Установить на торец втулки уплотнительную пластину, зажав ее винтом, затем отпустить защелку груза. Под действием его через зазор в паре постепенно начинает выдавливаться топливо, и чем больше зазор, тем быстрее. Величина нагрузки на плунжер должна соответствовать величине давления топлива 195–205 кгс/см2. Полное поднятие плунжера до момента отсечки под действием нагрузки, сопровождаемое выжиманием топлива через зазоры между втулкой и плунжером, должно происходить не менее чем за 20 с. Если время поднятия плунжера до отсечки превышает 40 с, то установить смоченную профильтрованным дизельным топливом плунжерную пару в вертикальное положение на торец втулки, предварительно подложив лист чистой бумаги. После пятиминутной выдержки при поднятии пары за хвостовик плунжера втулка должна опускаться с плунжера под действием собственной массы;
– толкатель плунжера установлен в отверстие корпуса насоса с номинальным зазором 0,025–0,077 мм. Предельно допустимый зазор при эксплуатации 0,20 мм. Замерить наружный диаметр толкателя плунжера микрометром или скобой размером 30,91;
– в узле ролик толкателя – втулка ролика – ось ролика основным дефектом является износ сопрягаемых поверхностей. Номинальный суммарный зазор 0,029–0,095 мм, предельно допустимый 0,30 мм (замерить индикаторной головкой). Если износ превышает указанный предел, толкатель разобрать и отремонтировать; при этом замеры производятся раздельно.
Предельно допустимый зазор в соединении ось ролика – втулка ролика при износе поверхностей – 0,12 мм, в соединении втулка ролика – ролик толкателя – 0,18 мм. Наружные поверхности деталей замерить микрометром, внутренние – нутрометром с индикатором.
При повторной сборке толкателя сохранить величину исходного натяга (0,005–0,031 мм) в соединении ось ролика толкателя – толкатель плунжера по отверстию, в которое запрессовывается ось ролика.
Величину исходного натяга обеспечить подбором оси ролика по отверстию в корпусе толкателя из разных комплектов. Предельно допустимый наружный диаметр ролика толкателя – 19,90 мм при номинальном диаметре 19,955–20,000 мм;
– на поверхности кулачкового вала не допускаются выкрашивание металла, задиры, срывы резьб, следы коррозии. Предельно допустимая высота профиля кулачка должна быть не менее 41,7 мм при номинальной высоте 41,95–42,05 мм. Замеры производить скобой 41,7;
– диаметр шейки под внутренние кольца подшипников должен быть не менее 20 мм при номинальном диаметре 20,002–20,017 мм, натяг по уплотняющей кромке манжеты – не менее 0,50 мм;
Нагнетательный клапан в сборе с седлом изготавливают из стали ШХ -15.
– основные дефекты нагнетательного клапана: риски, задиры, следы износа и коррозия на конусных поверхностях, на направляющей поверхности и на торце седла, на разгрузочном пояске клапана устраняют притиркой на плите притирочными пастами; при этом седло клапана крепят в цанговой державке за резьбовую поверхность; шероховатость торцовой поверхности седла должна составлять Ra 0,16 мкм, а направляющего отверстия и уплотняющего конуса Ra 0,08 мкм; после подбора и притирки клапанную пару не обезличивают; отсутствие заедания клапана в седле определяется его свободным перемещением под действием собственного веса в разных положениях по углу поворота после выдвижения клапана из седла на 1/3 длинны;
– на поверхности нагнетательного клапана не допускаются трещины, вмятины, следы коррозии. Износ клапана проявляется в потере герметичности по уплотняющему конусу и в заедании клапана в седле. Для обнаружения дефектов используйте лупу десятикратного увеличения. При потере герметичности притрите совместно седло и клапан по конусу пастой с размером зерна не более 3 мкм, при заедании клапана в седле детали промыть дизельным топливом. Если заедание не устраняется, пару заменить;
– предельно допустимый зазор в сопряжении палец рычага реек – паз рейки составляет 0,18 мм при номинальном зазоре 0,025–0,077 мм, предельно допустимый зазор в сопряжении ось поводка поворотной втулки 10 (см. рис. 8) – паз рейки топливного насоса равен 0,3 мм при номинальном зазоре 0,117–0,183 мм. Для замера пазов применять нутро-метр.
Основные дефекты деталей регулятора частоты вращения и способы их устранения:
– заменить верхнюю и заднюю крышки регулятора при наличии на них трещин. Если засорен сетчатый масляный фильтр, в задней крышке регулятора продуть сетку сжатым воздухом. Если фильтр имеет дефекты, заменить его. Эксплуатационный расход масла через фильтр должен быть не менее 1,6 л/ч при давлении 1–3 кгс/см2;
– для определения пригодности к дальнейшей эксплуатации державку грузов регулятора в сборе с грузами осмотреть и измерить без разборки, так как при выпрессовке детали могут быть повреждены и может нарушиться спаренность грузов, которые подобраны с разницей статического момента не более 2 кг/см2.
Частичную или полную разборку узла производить только при износе, превышающем допустимый, или при разрушении деталей.
Зазор между рычагом пружины регулятора и осью рычага, запрессованной в корпус насоса, не должен превышать 0,3 мм. Увеличение длины пружины регулятора допускается в процессе эксплуатации до 59,5 мм при номинальной длине 57–58 мм.
Основные дефекты деталей насоса низкого давления и ручного топливоподкачивающего насоса и способы их устранения:
– насос низкого давления и ручной насос заменить при наличии трещин на корпусе, изломов, механических повреждений, коррозии, ведущей к потере подвижности сопрягаемых деталей;
– особое внимание обратить на состояние узла шток–втулка насоса низкого давления, так как от величины износа в сопряжении зависит количество перетекаемого топлива в полость кулачкового вала. Зазор в указанном сопряжении не должен превышать 0,012 м. Величину зазора проверить, не извлекая втулки из корпуса насоса, путем определения времени падения давления воздуха от 5 до 4 кгс/см2 в аккумуляторе объемом 30 см3.
Рисунок 6 – Схема установки для испытания пары шток-втулка: 1 – корпус насоса; 2 – ограничитель перемещения штока; 3 – соединитель для подвода воздуха к корпусу насоса; 4 – воздушный аккумулятор; 5 – манометр; 6, 7, 8. 9 – краны; 10 – масловлагоотделитель; / – в атмосферу; // – из системы; /// – к насосу.
Установить корпус насоса в приспособление, заполнить аккумулятор сжатым воздухом до давления не менее 5,5 кгс/см2, герметично отключить его от магистрали сжатого воздуха и замерить время, в течение которого произойдет падение давления в аккумуляторе от 5 до 4 кгс/см2. Полученное время сравнить с аналогичными показаниями плотности эталонной прецизионной пары, имеющей зазор в сопряжении 0,012 мм. Пару заменить или отремонтировать, если плотность у нее меньше эталонной.
Если узел шток – втулка заменяется, поверхность резьбы и торец в корпусе насоса низкого давления очистить от остатков клея. Новую втулку штока установить в корпус насоса на клее, составленном на основе эпоксидной смолы. Для обеспечения прочности и герметичности соединения клеем очищенные контактирующие поверхности корпуса насоса и втулки предварительно обезжирить. После затяжки втулки штока с моментом 1 кгс-м проверить легкость перемещения штока в ней. При необходимости уменьшить момент затяжки.
После сборки проверить производительность насоса на установке, которую собрать по схеме: топливный бак – фильтр грубой очистки топлива – вакуумметр – топливоподкачивающий насос – манометр – мерный резервуар. Элементы схемы соединить прозрачными трубопроводами с внутренним диаметром не менее 8 мм. Для создания разрежения на входе в насос и противодавления на выходе установить краны.
Проверку производить, на летнем дизельном топливе при его температуре 25 – 30 °С. В отсутствии воздуха в системе убедиться по чистоте струи топлива в прозрачных трубопроводах. Насос должен засасывать топливо из бака, установленного на 1 м ниже насоса. Производительность насоса должна быть не менее 2,5 л/мин при частоте вращения кулачкового вала 1290–1310 об/мин, разрежении у входного штуцера 170 мм. рт. ст. и противодавлении 0,6 – 0,8 кгс/см2. При полностью перекрытом выходном кране и частоте вращения кулачкового вала 1290–1310 об/мин насос должен создавать давление не менее 4 кгс/см2. При полностью перекрытом входном кране и указанной частоте вращения кулачкового вала минимальное разрежение, создаваемое насосом, должно быть равно 380 мм рт. ст. Ручной топливоподкачивающий насос проверить на стенде, собранном по схеме: топливный бак – фильтр грубой очистки – топливный насос. Насос должен подавать топливо из бака, установленного ниже ручного насоса на 1 м. Проверить насос на герметичность, подводя воздух под поршень при давлении 2–3 кгс/см2 в течение 5–6 секунд с предварительным смачиванием подпоршневой полости дизельным топливом.
Сборка ТНВД
Сборку ТНВД необходимо проводить в обратном порядке. Для установки подшипников на кулачковый вал использовать приспособление И-801.27.000. Подбором регулировочных прокладок под крышкой переднего подшипника кулачкового вала необходимо обеспечить свободный ход вала не более 0,1 мм.
Организационная часть
В данном проекте работы по ремонту ТНВД организуются на специализированном рабочем месте. В условиях такой организации работ на данном рабочем месте выполняется ремонт одного узла или совокупность заранее определенных технологических операций, что позволяет повысить производительность труда, снизить требования к уровню квалификации рабочих и уменьшить за счет этого стоимость ремонта. Эта форма организации работ применяется на ремонтных заводах и в крупных мастерских.
Неисправности ТНВД и причины их возникновения
Дизельные двигатели ценятся за неприхотливость в эксплуатации, экономичный расход топлива, простоту обслуживания. При нормальной работе двигатель действительно выдает отличную приемистость, экономичность. В то же время, дизельный двигатель, по сравнению с бензиновыми аналогами, весьма чувствителен к некоторым факторам, главный из которых – качество используемого топлива. Система подачи топлива дизельного двигателя устроена таким образом, что горючее и воздух подаются в цилиндр поочередно: в первую очередь поступает воздух, а в момент завершения такта сжатия топливо, под высоким давлением, впрыскивается в цилиндр.
Причины возникновения неисправностей ТНВД
Основная причина, по которой топливный насос подвергается поломкам и неисправностям, заключается в износе составляющих ТНВД. На практике износ проявляется в ослаблении натяги в зафиксированных посадках, а между подвижными деталями увеличивается зазор. Нарушенное расположение деталей ведет к их постепенной хрупкости, в образовавшиеся пустоты попадает грязь и другие отложения. В свою очередь, быстрый износ деталей возникает в тех случаях, когда используется низкокачественное топливо, содержащее даже незначительные примеси.
Минимальное количество воды, содержащееся в топливе, способно привести не только к возникновению неисправностей, но и к полному выходу системы из строя. Не менее губительным будет содержание частиц пыли или механических примесей. Ведь функционирование ТНВД происходит при высоком давлении и температуре, поэтому любые посторонние частицы способны нанести вред плунжерным парам. Своевременное обслуживание ТНВД, замена фильтров, промывка топливной системы позволят существенно снизить риск возникновения неисправностей в узлах автомобиля.
Понять, что топливный насос высокого давления (ТНВД) подвергся неисправности можно по характерным признакам, сопровождающим эксплуатацию автомобиля. К таковым относятся:
- увеличение расхода топлива;
- нарушена подача топлива от ТНВД к форсунке;
- с шестерни ТНВД соскальзывает ремень ГРМ;
- обнаружена течь топлива из ТНВД;
- затруднен запуск двигателя;
- посторонние шумы в ТНВД;
- повышенная дымность при работе автомобиля.
Основные неисправности ТНВД
Остановимся более подробно на некоторых неисправностях ТНВД, встречающихся чаще других типов поломок. Так, одна из наиболее частых неисправностей заключается в нарушении синхронности, равномерности подачи топлива. Причина возникновения данной проблемы заключается в износе составных узлов топливной системы: плунжерных пар, клапанов нагнетания, изменением пропускных характеристик форсунок, изношенных зубьев рейки, поводков плунжеров и т.д. При возникновении неисправности в подаче топлива возникают проблемы с мощностью двигателя, увеличивается расход топлива. Кроме этого, цилиндры двигателя при неравномерной подаче топлива выдают перебои в работе, особенно на малых оборотах. Блок двигателя подвергается ощутимой вибрации.
Запаздывание и неравномерность момента начала впрыска ТНВД – еще одна часто возникающая неисправность в работе насоса. Проблема запаздывания является результатом износа целого ряда составляющих топливной системы. Перечислить все детали сейчас не представляется возможным, однако, наиболее ключевые из них это: ось ролика и корпус толкателя, шарикоподшипники, гнезда корпуса колеса и другие составные части систем.
Наиболее сложной и опасной неисправностью ТНВД считается нарушение подвижности рейки и сопутствующие этому деформации, поломки. К неисправностям рейки ТНВД относятся заклинивание, отсоединение от регулятора, ослабление хомутиков поводков плунжеров. Чаще всего заедание рейки происходит из-за попадания грязи, абразивных частиц или воды, провоцирующей коррозию деталей. Особую сложность представляет неисправность топливных систем двигателей с двухступенчатой системой впрыска горючего, а так же двигатели с электронным управлением. Предотвратить возникновение неисправностей позволяет своевременный технический осмотр транспортного средства. Диагностика, регулировка ТНВД и форсунок – лучшая профилактика поломок.
Информация взята с сайта http://www.dizelexpert.ru/