Металлические колеса своими руками | Мастеровой
Компрессоры, станки, генераторы, стеллажи, столы и другое оборудование, которое необходимо перемещать в пределах цеха, участка или мастерской часто устанавливают на колеса. В хозяйственных и строительных магазинах достаточно большой выбор данного товара, но качество изготовления и материалы из которых выполнены эти изделия , часто оставляют желать лучшего. Да и цена на такие колёса может быть существенной. Зачем же покупать эти колеса, когда можно легко изготовить их своими руками? Приступаем к изготовлению металлических колёс своими руками
1. Назрезаем из трубы кольца шириной 30-35мм
Центруем и привариваем втулку к квадрату
Размер колёс может быть какой угодно, всё зависит от ваших потребностей и имеющегося в наличии материала для их изготовления. Колеса готовы! |
Статьи на похожую тему.
- Мотоподъёмник своими руками
- Каркасный дом своими руками
Изготовление деревянного колеса от телеги
В наше время существует множество вариантов того как украсить свой дачный участок. Одним из таких вариантов является деревянное колесо от телеги. Этот элемент может внести изюминку и сделать ландшафтный дизайн территории особенным. Также этот элемент отлично подходит для стиля «кантри». Сейчас мы поэтапно рассмотрим инструкцию изготовления этого элемента из дерева. Хотя работа требует определенных навыков и наличия специального инструмента, все же если эти два фактора имеются, вы сможете сэкономить свои деньги. Вам придется потратиться только на материал.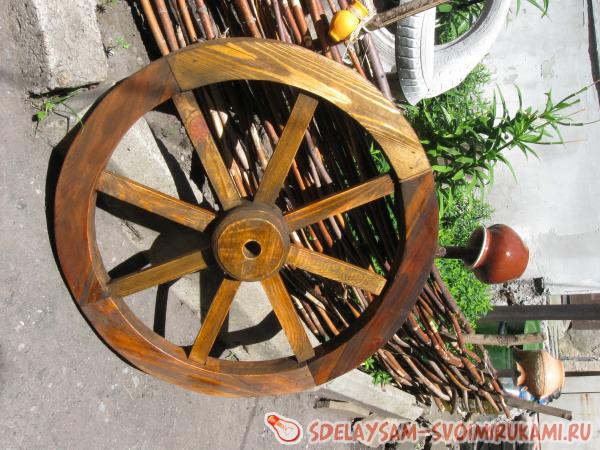
Итак, для выполнения этого элемента нам потребуется:
• Электролобзик;
• Электрорубанок или рейсмус;
• Шлифмашина;
• Фреза;
• Шуруповерт;
• Струпцины;
• Стамеска и киянка;
• Клей ПВА, лак, морилка;
• Саморезы;
• Сверла под саморезы, которые будете использовать, а также перьевое сверло 30 мм;
• Лес (доска толщиной 50 мм и шириной 25 мм).
Первым этапом работы является изготовления лекала. Необходимо заранее начертить чертеж тех размеров колеса, которые вы планируете сделать. Диаметр, который представлен на рисунке составляет 700 мм. Затем изготавливаются четыре лекала, по которым вырезаются полукруги из древесины. Вырезаются данные полукруги электролобзиком.
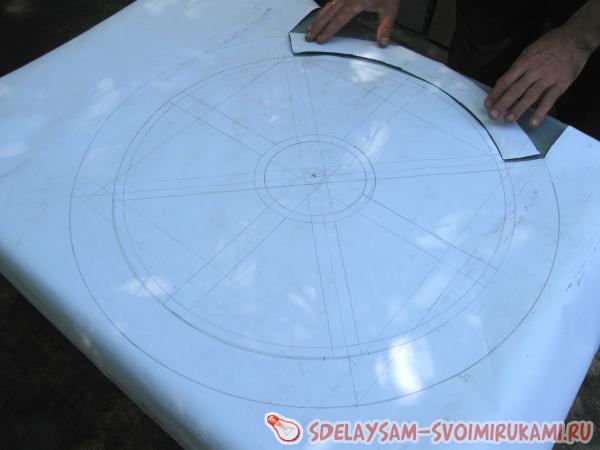
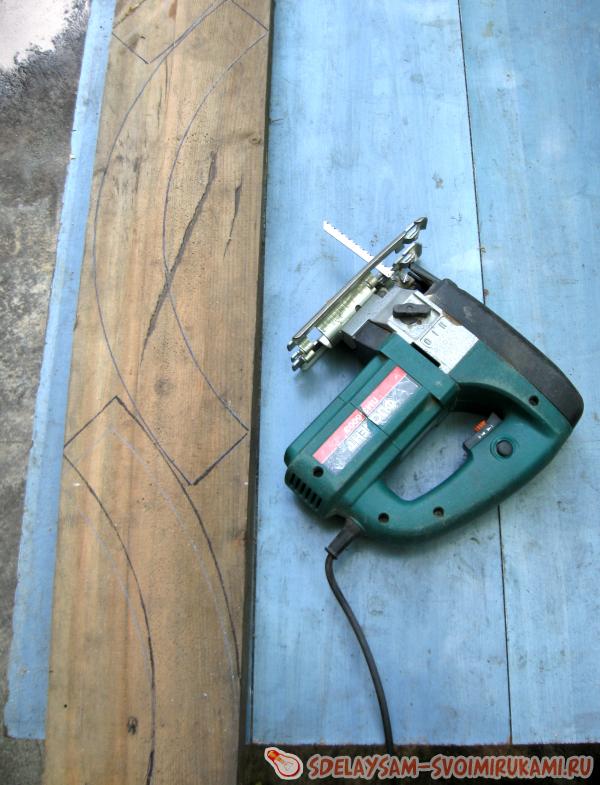
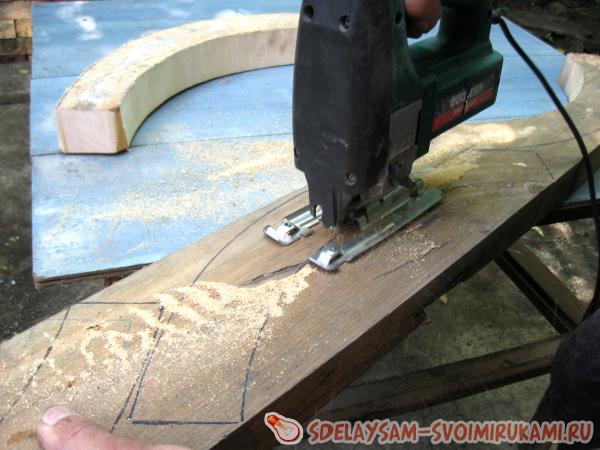
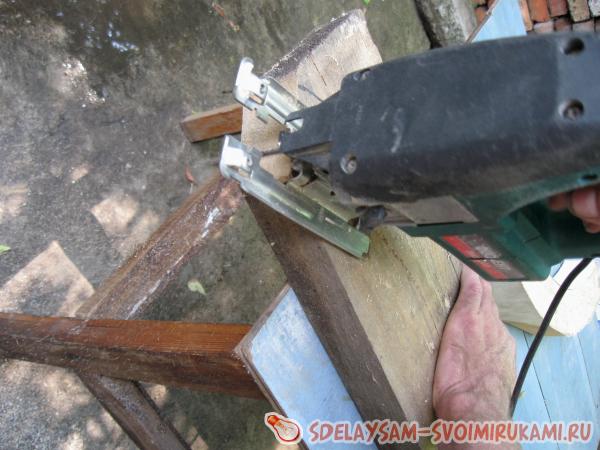
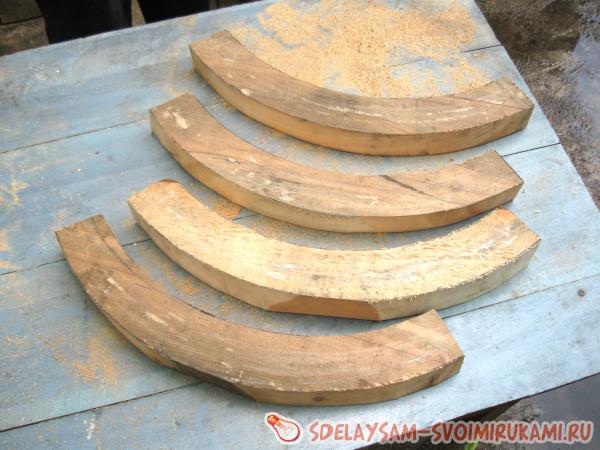
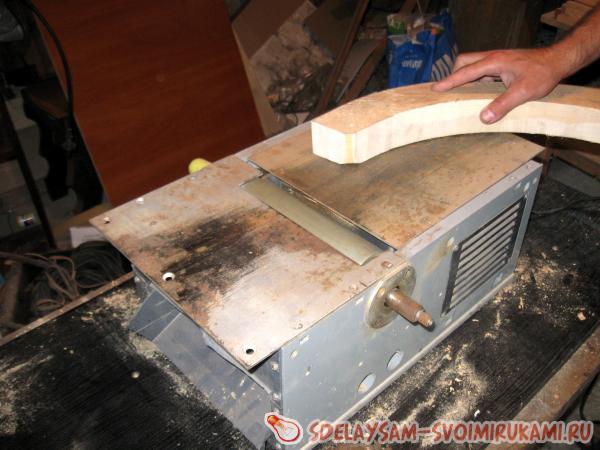
Когда четыре полукруга готовы, их необходимо склеить между собой. Для этого будет лучше использовать клей ПВА. Эти четыре детали можно временно скрепить металлическим профилем или маяком. Пока клей подсыхает, в это время можно заняться остальными запчастями колеса.
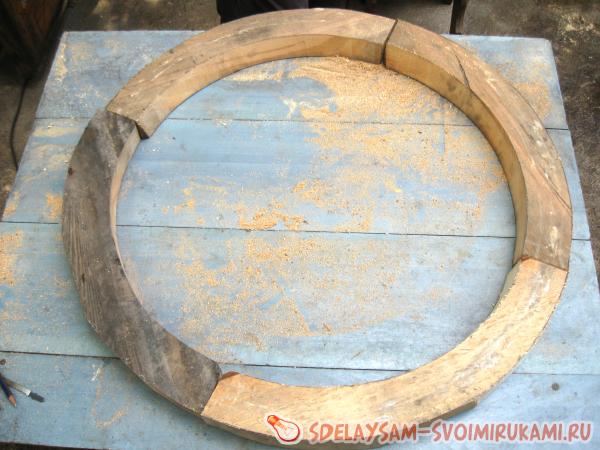
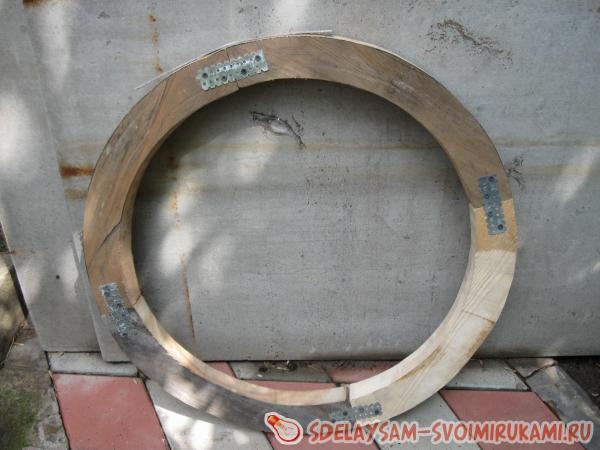
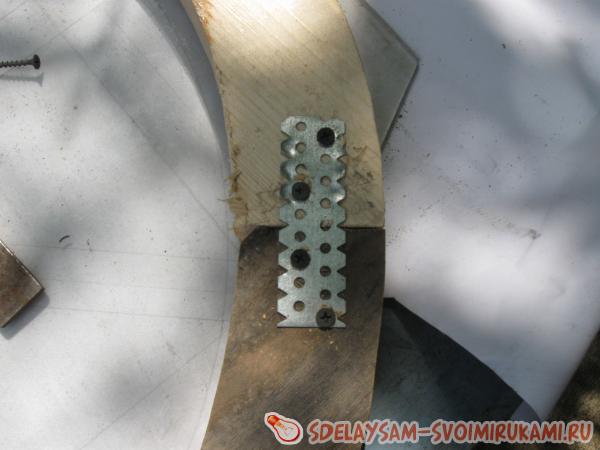
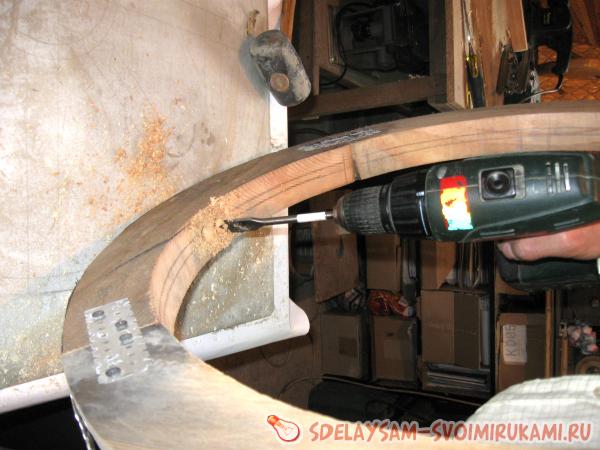
При помощи циркуля чертятся два одинаковых круга диаметром 20 – 25 мм на деревянной доске толщиной 30 мм и бруске толщиной 50 – 60 мм. Также можно приготовить заготовки под спицы. Длина заготовок зависит от размеров вашего колеса. Всего необходимо 8 заготовок.
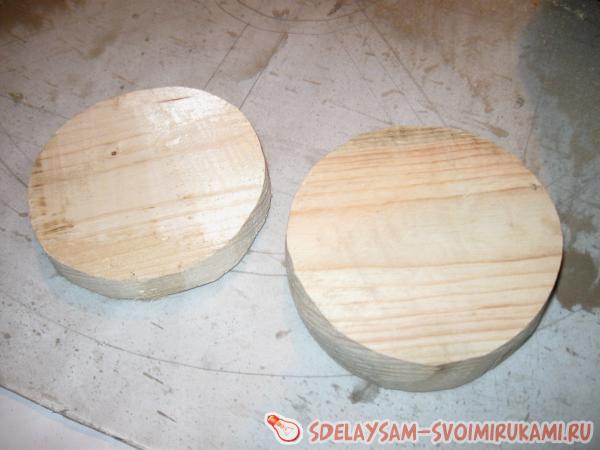
Когда колесо скрепилось, и клей застыл, с внутренней стороны колеса необходимо сделать 8 гнезд, в которые впоследствии будут вставляться спицы. Эта операция выполняется при помощи киянки и стамески. Чтобы было проще выдалбливать шип, можно использовать перьевое сверло или фрезу со специальной насадкой для выбирания гнезд. Размер гнезд должен соответствовать размеру спиц. Причем будет лучше, если спицы не будут свободно заходить в гнезда, а наоборот их придется забивать киянкой.
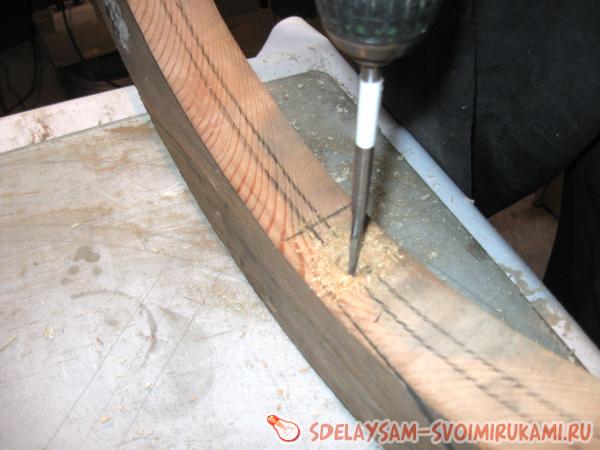
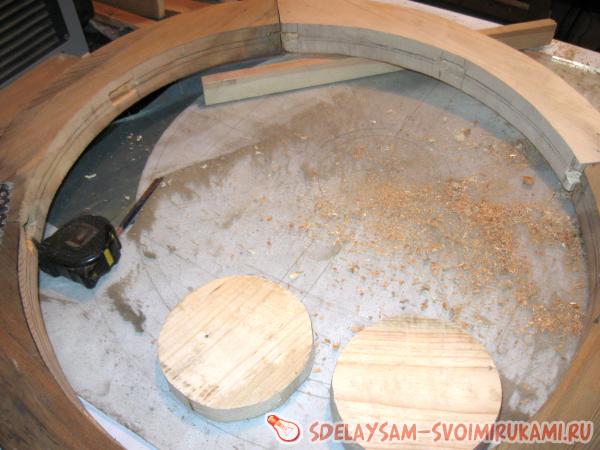
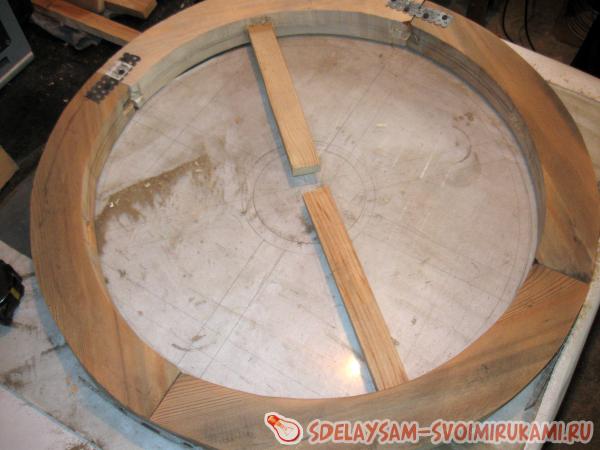
Далее необходимо тщательно промазывать гнезда клеем ПВА, и забить в них деревянные спицы. Когда спицы закреплены, прилаживаем колесо к чертежу, для того чтобы определить точную середину и приклеить два круга с обеих сторон. Чтобы дополнительно скрепить внутренний круг со спицами, можно использовать саморезы. Так как между спицами будут образовываться зазоры, их необходимо заполнить деревянными клинышками, которые можно сделать при помощи стамески или лобзика.

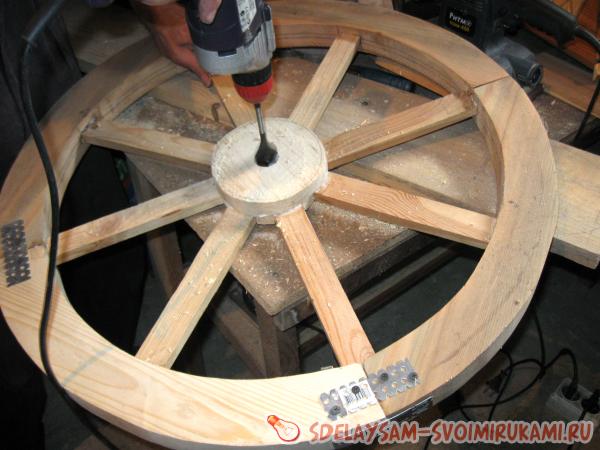
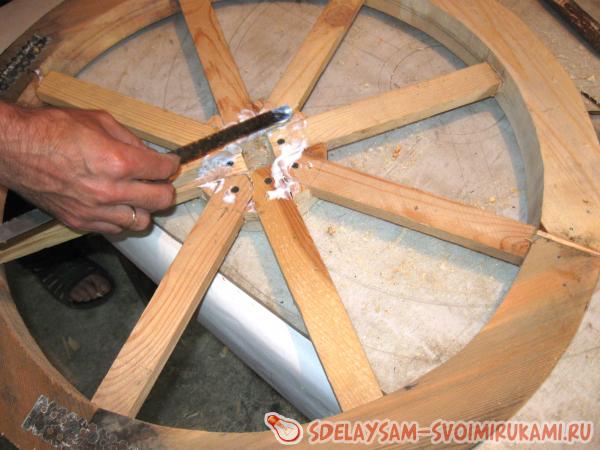
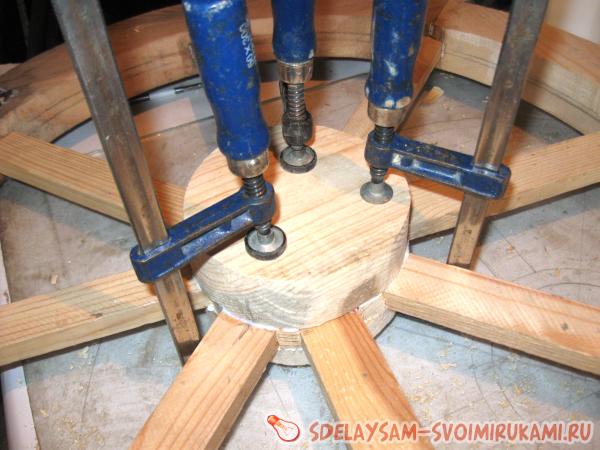
Чтобы украсить колесо и придать ему немного ажурного вида, можно использовать фрезу с фигурной насадкой. Для примера можно обратить внимание на иллюстрацию, где внутренний круг обработан фигурной фрезой. Как вариант, то же самое можно сделать и со всеми спицами. В конце при помощи шуруповерта и перьевого сверла 30 мм в середине колеса проделывается сквозное отверстие.
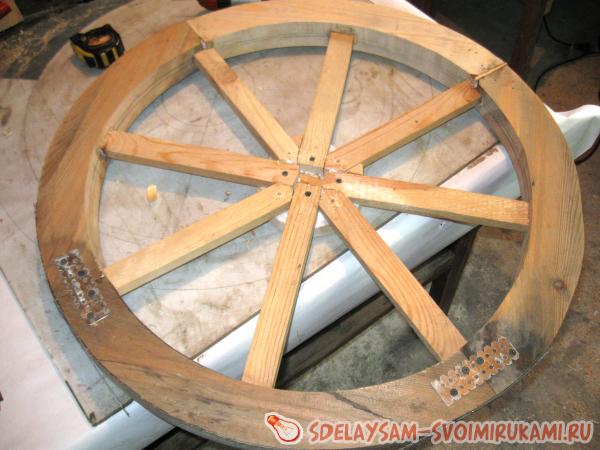
Далее при помощи шлифмашины удаляются все неровности с поверхности древесины. Некоторые места будет сложно обработать шлифмациной, поэтому придется также использовать и обычную наждачную бумагу вручную. Например, между спицами. Чтобы облегчить этот процесс, то можно заранее использовать электрорубанок, рейсмус и шлифмашину до скрепления деталей, так как шлифовать изделие уже в собранном виде не совсем удобно. Также можно учесть, что это садовое украшение, и что колесо будет находиться на улице. Поэтому нет необходимости досконально вышлифовывать поверхность и делать изделие идеально гладким.
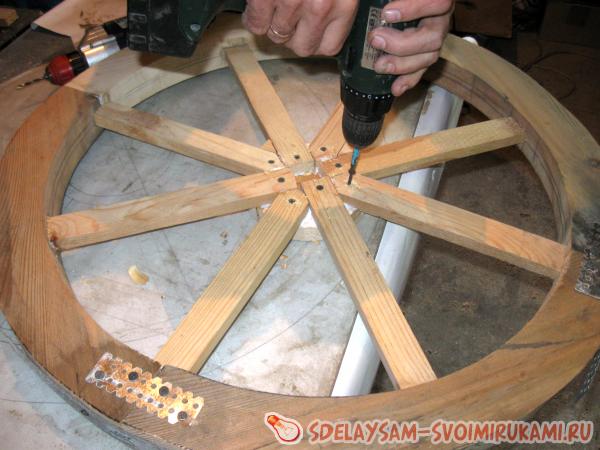
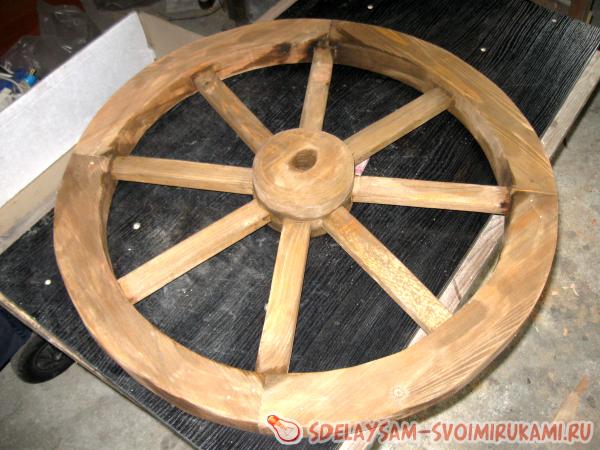
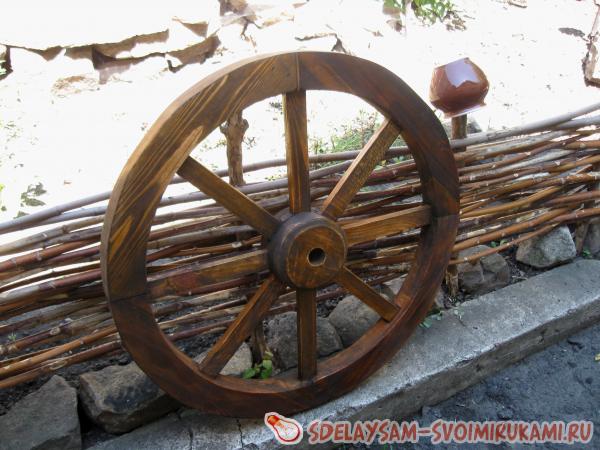
Можете не сомневаться что данный элемент, прекрасно сможет украсить ваш приусадебный участок. Эта изюминка сможет внести уют и спокойствие в ландшафтный дизайн любой территории. Особенно красиво деревянное колесо будет сочетаться рядом глиняными горшками с цветами, облокотившись на каменную стену. Это украшение прекрасно сочетается с натуральными природными материалами.
Деревянное колесо своими руками
Для многих дачников загородный участок является не только местом, где выращиваются овощи и фрукты, но и территорией для отдыха. Заядлые огородники стараются его всячески облагородить, украсить, сделать уютным и удобным для проживания. Поэтому и появляются на дачах всякие декоративные мельницы, пруды, колодцы, телеги — всё, что радует глаз и напоминает о настоящей русской деревне. Очень часто используются в оформлении участка старые деревянные колёса от телеги. Из них делают люстры, прицепляют к самодельным тележкам или просто вешают на стену сарая. Единственный минус – настоящее деревянное колесо сегодня найти очень трудно. Их все уже давно продали предприимчивые крестьяне своим городским соседям. Ничего не остаётся, как попробовать сделать деревянное колесо от телеги своими руками. Что из этой затеи получилось у нас, вы узнаете, прочитав эту статью.
Нам повезло – настоящее колесо от телеги мы смогли раздобыть. Но одного оказалось мало – колёса удачно вписываются в дизайн дачного участка. Поэтому мы решили попробовать сделать ещё одно деревянное колесо своими руками. Если получится – можно потом и тележку декоративную построить, и люстру оригинальную смастерить.
Итак, посмотрели на старинный экземпляр и принялись за работу.
ДЕРЕВЯННОЕ КОЛЕСО СВОИМИ РУКАМИ
Начнём с изготовления ступицы. Это самый сложный элемент изделия. В домашних условиях его сможет сделать только очень опытный мастер. Мы пошли простым путём: взяли деревянный брусок размером 10 на 10 см, длиной 60 см и отправились к токарю. Хорошо, что остались ещё люди, обладающие такой профессией. Из этого бруска нам выточили 6 круглых болванок, похожих на хоккейные шайбы, диаметром 9,5 см, шириной 8 см. Внутри просверлили отверстие диаметром 5 см – ступица готова. Конечно, это именно декоративная ступица – чтобы надеть её на ось, нужно было бы вытачивать специальные выступы. Но такой цели не стояло, деревянное колесо нужно для украшения участка.
На следующем этапе мы сделали чертёж деревянного колеса в натуральную величину. На миллиметровую бумагу перенесли размер ступицы, определили диаметр изделия – 60 см, количество спиц выбрали 8. Нарисовали всё на бумаге и замерили размеры получившихся деталей.
Приступим к изготовлению спиц. На чертеже они получились равными 19 см. Возьмём деревянный брусок размером 5 на 5 см и отрежем от него 8 частей длиной 23 см. По два см с каждой стороны мы оставим на шканты, с помощью которых соединим спицу со ступицей и косяком колеса. Обработаем бруски рубанком, придав им товарный вид.
Теперь сделаем на спицах шканты. С каждой стороны бруска отметим по 2 см и ножовкой сделаем пропилы по 1,5 см. Острым ножом срежем лишнюю древесину и оформим выступы цилиндрической формы диаметром 2 см.
Чтобы придать деревянному колесу хоть какой-нибудь дизайн, обработаем спицы фрезерным станком. Закрепим брусок на табуретке с помощью струбцины и срежем кромки с четырёх сторон.
Следующий шаг – изготовление так называемых косяков деревянного колеса. Согласно чертежу, их у нас будет 8 штук. Возьмем белый лист бумаги и перенесём на него рисунок одного косяка. Это будет шаблон.
Подберём доску толщиной 5 см. Ширины доски должна быть не меньше длины косяка. Приложим лист с рисунком к доске и обведём чертёж карандашом, прикладывая небольшое усилие. Можно воспользоваться копировальной бумагой, но в нашем случае мы обошлись без неё. Убрав листок, обведём контур косяка, отпечатавшийся на доске. Электролобзиком аккуратно выпилим 8 штук и обработаем их шлифовальной машиной.
Косяки имеют сложную геометрическую форму, качество их изготовления напрямую влияет на внешний вид деревянного колеса. В идеале все 8 штук должны быть идентичными.
Теперь нужно подготовить косяки к соединению со спицами. Для этого в нижней плоскости изделия в центре пересечения двух диагоналей просверлим отверстие диаметром 2 см и глубиной тоже 2 см.
С помощью транспортира разметим ступицу на 8 равных частей и тоже просверлим 8 отверстий диаметром 2 см.
Дальше проводим примерку деревянного колеса. Вставим спицу в косяк, потом в ступицу и соединим все части между собой. Меняя элементы местами, нужно добиться, чтобы изделие выглядело ровным и все детали подходили друг к другу. На этом этапе проводим окончательную доводку элементов: подтачиваем, подпиливаем, рассверливаем.
Убедившись, что все детали подходят друг к другу, пронумеровываем их, чтобы не перепутать, и начинаем сборку. Соединяем элементы при помощи мебельного клея.
Косяки, чтобы колесо было прочным, закрепляем между собой при помощи мебельных шкантов. Для этого просверливаем в боковых гранях отверстия, вставляем в них шкант и соединяем детали между собой.
Не спеша, собираем деревянное колесо. К сожалению, отсутствие опыта сказалось на сборке – косяки не замкнули окружность, не хватило 2 см. Всё-таки при их выпиливании нужно быть более точным. Пришлось вырезать деревянный клин по размеру, намазать его мебельным клеем и закрепить струбциной на сутки.
Дальше шлифовальной машиной уберём все выпуклости, сделаем колесо от телеги ровным и гладким. Щели можно замазать герметиком по дереву.
Деревянное колесо готово к покраске. Мы своё изделие обработали сначала чёрной морилкой, состарив его, а в завершении покрыли двумя слоями бесцветного лака.
Чтобы колесо со временем не рассохлось, скрепим его жестяной лентой, прикрутив её на саморезы.
Деревянное колесо от телеги готово. Поставим его к декоративному забору. Учитывая совершённые ошибки, со временем можно сделать своими руками ещё несколько штук – место применения для них всегда найдётся. Если статья понравилась, поделитесь ей в соцсетях.
Мастерим деревянное колесо своими руками
Сегодня будем мастерить деревянное колесо своими руками, кстати, это колесо вполне сгодится, как и для интерьера дачи или дома, так и для функционального колеса от телеги или гужевой повозки, принцип работы будет примерно одинаков.
Инструмент и материал для изготовления колеса.
Инструмент:
— Шуруповерт или фигурная отвертка
— Строительная рулетка (метр)
— Циркулярная пила, или электролобзик, или ножовка по дереву
— Строительный уголок 90 градусов
— Карандаш или шариковая ручка
— Транспортир, обычный школьный
Материал:
— Деревянный брус
— Фанера пол листа
— Белые саморезы по дереву
Как вы наверное поняли в инструменте вы можете использовать, в идеале циркулярную пилу, если нет, то электролобзик, ну а если и его нет, то можете воспользоваться и ножовкой по дереву, будет долго, но возможно.
Чертеж деревянного колеса
Надеюсь по чертежу у вас не возникнет вопросов, по периметру все бруски ровняются 37 см., а внутренние спицы колеса ровняются 39 см. По ходу сборки может быть придётся спицы немного укоротить, но не факт.
Этапы изготовления колеса своими руками
Первый этап
Итак, первым этапом будет приобретение необходимого бруса, есть два варианта, либо вы покупаете уже готовый брус необходимого размера, либо обрабатываете брус на циркулярке. В нашем случае приобретен уже готовый брус размером 3 метра длинна, 9 см. ширина и 4.5 см. толщина, этого бруса при правильной раскройке хватит, аж на два колеса.
Второй этап
Вторым этапом будет изготовление заготовок на корпус колеса и спицы, начнем с корпуса, всего нужно 8 заготовок, их надо подогнать под размер — 37 см. длинна, 4 см. ширина и 2 см. толщина, особое внимание уделите торцовке (отпиливание) длинны, они должны быть идеальны, иначе будущая конструкция просто не сойдется вместе.
Изготавливаем спицы
Теперь надо изготовить спицы, их как вы уже поняли тоже должно быть 8 штук, только размер немного отличается — 39 см. длинна, 2 см. ширина и 2 см. толщина. В спицах можно сделать одну хитрость, так как они у нас будут смыкаться и соединяться в одно целое, а потом центроваться, то можно четыре спицы отрезать по 39 см., а остальные четыре по 37 см. так будет легче соединять.
Сейчас нам надо отрезать торцы корпуса для дальнейшей стыковки, на этом этапе будьте внимательны. Возьмите одну заготовку и с одного торца поставьте отметку ровно на 1.7 см. (17 мм.)
Ту же процедуру проделайте с другой стороны заготовки и проведите линию от поставленной отметки к углу, должно получиться как на фото.
По отмеченной линии аккуратно отрежьте углы, только не торопитесь, от этих спилов зависит, то на сколько ровно будут прилегать друг к другу заготовки.
Изготавливаем крепежные детали
Все обработанные детали пока откладываем в сторонку и приступаем к изготовлению крепежных деталей, материал в нашем случае будет фанерный лист, но вы можете использовать и остатки от деревянного бруса. Всего нужно сделать 8 деталей для крепежа корпуса, 8 деталей для спиц колеса и одну деталь центровку (крепеж для спиц в центре). Размер детали крепежа корпуса — внешние стороны по 7 см., а внутренние стороны по 5 см., а угол спила ровно 45 градусов. Размер детали крепежа спиц 8 см. длинна, 2.5 см. ширина, смотрите на фото, что у вас должно получиться.
Центровку для спиц мы будем делать обрисовав банку шпатлевки по кругу.
Отрезаем электролобзиком по кругу, получается вот такая прелесть.
Собираем корпус и спицы
Сейчас нам надо вернутся к деталям корпуса, подготовьте ровную поверхность и приложите все детали друг к другу, угол к углу, если вы сделали все правильно, то у вас должна получится вот такая окантовка колеса.
Если все сошлось, то берем крепежные заготовки для корпуса и прикручиваем их белыми саморезами.
Прикручиваем по всему периметру поочередно, лучше по часовой стрелке, чтобы не запутаться.
Делим каждую деталь корпуса пополам и прикладываем к середине спицы, должно получится так.
Крепим спицы крепежными заготовками.
Ну и последним штрихом будет закрутить центровку к спицам, тем самым закрепив всю конструкцию в целом.
Надеемся, что вам не сложно было смастерить деревянное колесо своими руками по данной инструкции. Обработать готовую поверхность можно лаком, краской, морилкой, воском или любым другим по вашему желанию способом.
Фотография готового изделия
А теперь можно и полюбоваться итоговым фото захватив вид сверху.
Делаем деревянные колеса на деревянных дисках
У меня залежалась партия колес, которые я испортил, просверлив в них отверстия неверного диаметра насквозь колеса и подобрав неудачный цвет. Пришло время исправлять свою ошибку.
Модель колеса, которую я буду модернизировать, представляет собой ободок, визуально разграничивающий лицевую часть на диск и шину. Центр колеса (диск) я высверлю и изготовлю вкладку-диск, а обод оставлю прежним. Темный цвет будет имитировать резину. Удержать руками круглое колесо оказалось тяжело, рука опасно соскользнула под сверло. Обязательно покажу придуманный мной способ для решения этой проблемы.
Для наглядности я добавил видео, а ниже, как обычно, пошаговый мастер-класс с фото.
Итак, высверливаю у старых колес центральную часть, используя сверло форстнера диаметром 26 мм.
Далее, приступаем к изготовлению вкладки-диска. Берем дощечку из бука толщиной 12 мм и рисуем на ней четыре окружности диаметром 26 мм. Размечаем на них центр и расчерчиваем линейкой на четыре сектора-дольки.
Теперь в центре окружности высверливаем несквозную «лунку» под центральную ось.
Далее, по внешнему радиусу окружности сверлю четыре сквозных отверстия диаметром 14 мм, формируя будущий крестообразный диск. При желании, отверстий можно сделать больше, например расчертить не на 4, а на 8 секторов и высверлить 8 отверстий. Форма диска будет более сложной.
Для скругления краев диска я использую рейку со шкантом. Надеваю на него заготовку диска, фиксирую струбциной.
Включаю шлифовальный станок, подвожу заготовку диска и прокручиваю на 360 градусов.
Далее, дорабатываю декоративный объем лицевой части диска.
Для скрепления диска и обода использую маленькие круглые палочки. Подобрав сверло по диаметру палочки, сверлю «глухие» лунки-отверстия в местах соприкосновения диска и обода. Таким образом, чтобы половина была на диске, а половина на ободе. Капаю немного клея, вставляю палочки. После высыхания клея палочки подрезаю «заподлицо», зашлифовываю до гладкости.
Колеса на классных деревянных дисках готовы! Устанавливаю их на машинку.
Спасибо, что дочитали! Не забывайте подписываться на блог, чтобы первыми читать новые интересные публикации и статьи!
До новых мастер-классов!
Самодельные колеса — вездеходы
Не секрет, что к некоторым деревням без проблем добраться можно лишь летом. Осенью, зимой или весной возникают большие сложности – то болото, то снежные заносы, только современный полноприводный автомобиль справляется с поставленными задачами. Но это очень дорогое удовольствие, большинству жителей глубинки не по карману. Расскажем, как переделать старую резину и сделать из обыкновенного Жигуленка настоящий вездеход.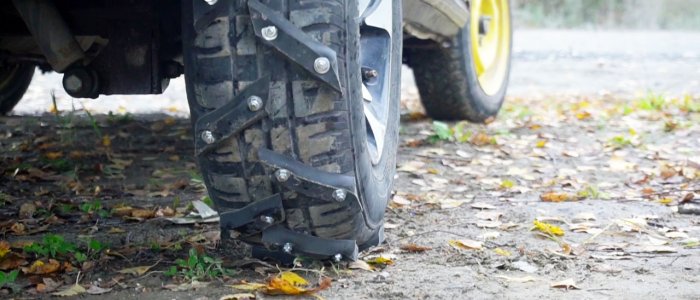
Что необходимо подготовить
Для фиксации элементов необходимы метизы М6 соответствующей дины. Зацепы делаются из ремня профиля «D» (верхняя ширина 32 мм, нижняя 19,2 мм). Ремень на куски рубится топором, для точности дины кусков удар делается кувалдой. Отверстия просверливаются обыкновенной дрелью и сверлом по металлу, гайки легче закручивать шуруповертом. Флиппер делается из старых камер, приклеивается к покрышкам резиновым клеем. Для отрезания болтиков требуется болгарка с абразивным диском.
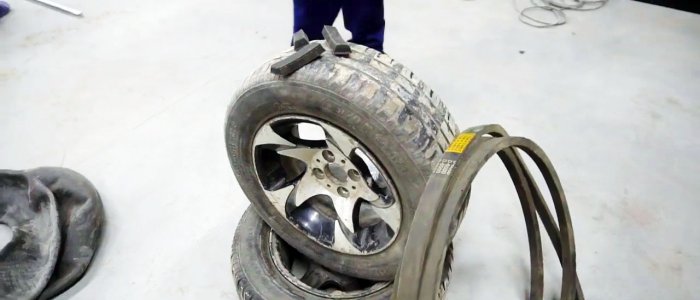
Процесс изготовления
Топором на ровной доске нарубите заготовки ремня. Длина примерно 15 см, конкретные значения зависят от ширины покрышки и угла наклона отрезков. Лезвие топора располагайте под углом 45 градусов к оси ремня. Количество зависит от расстояния между отдельными элементами, в среднем оно должно составлять 20 см.
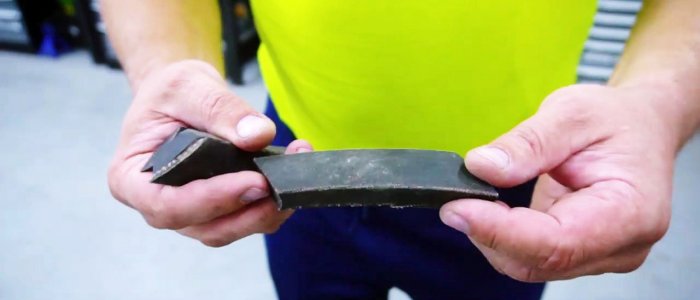
Для того чтобы все отрезки были одинаковой длины, сделайте на доске метку и используйте ее как шаблон. Топор установите в нужном месте и ударом кувалды по обуху отрубите кусок ремня. Просверлите отверстия в ремне и покрышке, располагайте их на расстоянии примерно 1 см от торцов и по оси симметрии.
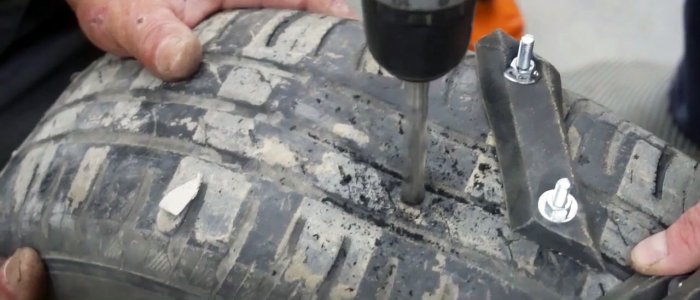
Вначале высверлите отверстия на всех кусках ремня, а затем используйте каждый как шаблон для высверливания отверстий в покрышке. Каждый элемент «елочки» прикручивайте отдельно сразу после подготовки отверстий. Расстояние между кусочками ремня можно устанавливать на глаз или приспособить под шаблон любую доску соответствующей ширины.
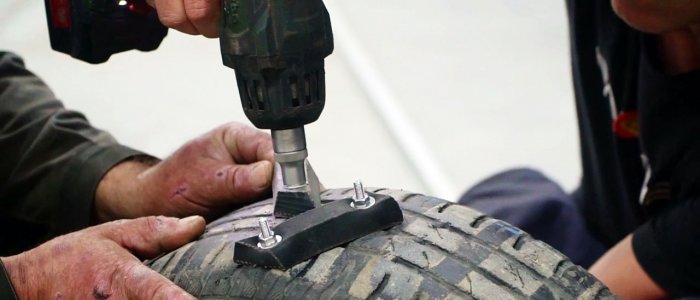
По описанному алгоритму установите «елочку» по всему колесу. Подготовьте две покрышки на задние колеса. Старую камеру разрежьте по радиусу. Надо сделать подобие флиппера – это специальная лента, защищающая камеру от повреждения шляпками болтиков, которые держат по периметру покрышки куски ремня. Намажьте внутреннюю сторону покрышки резиновым клеем.
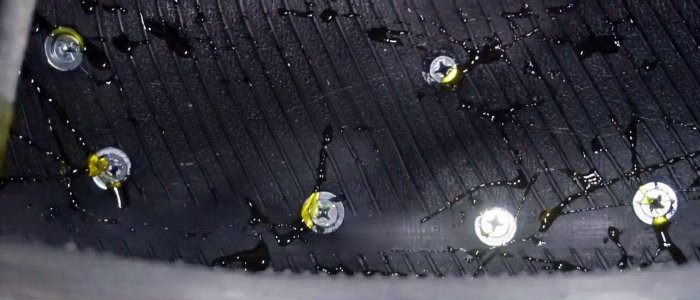
Аккуратно вставьте флиппер, разровняйте его. Оставьте на сутки для застывания клея. Болгаркой отрежьте выступающие части болтиков по окружности колес.
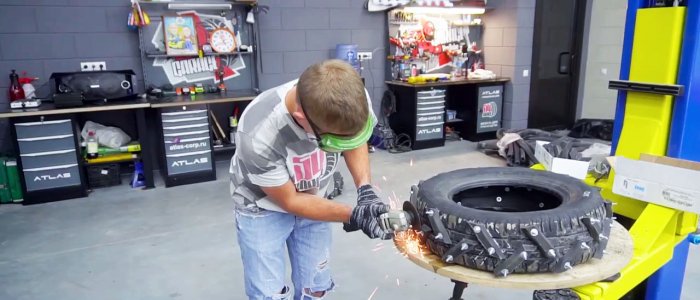
Соберите колеса и установите их на автомобиль. Проведите тест-драйв. Вы будете удивлены результатами, по проходимости такой жигуленок намного превосходит самые современные джипы.
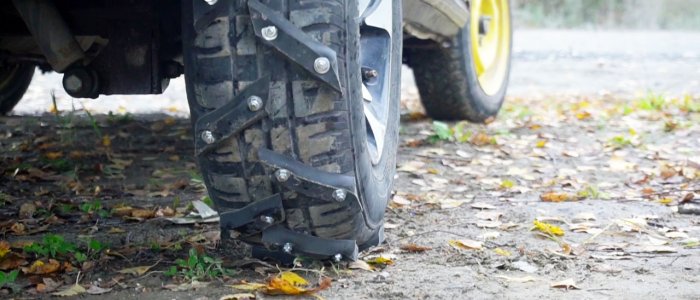
Заключение
На такой резине нельзя ездить по дорогам с твердым покрытием, скорость движения не должна превышать 50 км/ч. Надо помнить, что прочность фиксации не отвечает требованиям к скоростной резине, такие покрышки можно применять только кратковременно для проезда плохих участков дороги.
Смотрите испытания на грязи в видео
Полные испытания всех проходных свойства данных колес на заднеприводном автомобиле обязательно смотрите в видеоролике.
Шиномонтажный станок своими руками

Привет всем любителям самоделок. Владельцам автомобилей знакома ситуация с заменой резины с зимнюю на летнюю или наоборот. В интернете есть много вариантов для данной цели, как станки, так и отдельные приспособления. В этой статье я расскажу как сделать шиномонтажный станок своими руками, который поможет каждому автолюбителю разбортировать или забортировать колеса на своём авто, в независимости бескамерка это или нет. Также данное приспособление сэкономит ваши деньги и прибавит опыта в сварочных работах.
Перед тем, как перейти к прочтению статьи, предлагаю посмотреть видео с тестированием данного шиномонтажного станка.
Для того, чтобы сделать шиномонтажный станок, понадобится:
* Сварочный аппарат, электроды
* Средства индивидуальной защиты: краги, сварочная маска
* Профильная труба 40*20
* Металлическая щетка
* Болты М12 и гайки к ним
* Подшипник ротора электродвигателя
* Магнитные уголки для сварки
* Углошлифовальная машинка и отрезной диск
* Камера автомобильная
* Строительный уголок
* Труба металлическая 60 мм
* Металлический уголок 50 мм
Вот и все, что нужно для сборки такой самоделки.
Шаг первый.
Первым делом необходимо сделать из трубы стойку, к которой будет крепиться все остальное «хозяйство». Берем металлическую трубу диаметром 60 мм и внизу к ней привариваем два уголка 50 мм на сторону, чтобы внутрь вошел профиль 40*20, располагаем уголки под углом относительно друг друга около 120°. В верхней части уголков сверлим отверстия и привариваем гайки под болты М12, они в дальнейшем будут удерживать профильные трубы.
Для большей прочности привариваем уголок, соединяющий два предыдущих. С другой стороны трубы привариваем еще один уголок 50 мм и просверливаем в нем отверстия под два болта М12 и к самому уголку с внутренней стороны привариваем гайки.
Шаг второй.
Теперь делаем основание, которое будет служить подложкой для колеса, на котором будет производиться спуск остаточного давления в колесе. Делаем из профиля 40*20 отрезки для основания. Берем сварочный аппарат, электроды, краги, защитную маску и привариваем детали каркаса. Для того, чтобы понять, как это должно выглядеть , можно воспользоваться фотографией, размеры сваренного основания должны быть чуть больше диаметра колеса.


По краям привариваем профиль под углом 45°, а для прочности устанавливаем перегородку из той же профильной трубы, также для упора колеса крепим к основанию уголок 50 мм.
Шаг третий.
Для удобства спуска остаточного давления в колесе делаем рычаг. На трубу привариваем ушки с отверстием под болт М12 в двух местах, снизу и сверху. На трубу диаметром 32 мм привариваем ушки, отступив от начала около 15 см. После чего трубу диаметром 28 мм отрезаем до длины 15 см при помощи углошлифовальном машинки. При работе с УШМ не забываем о защитных очках и перчатках, а также будьте аккуратны и держите инструмент крепко.
Просверливаем в трубе отверстия под болт М12 и скручиваем две готовые части вместе. В самому верху трубы, немного отступив от самого края, просверливаем отверстие под болт, а в ее нижней части привариваем уголок, которым и будем спускать колеса. В верхнее ушко устанавливаем рычаг, сделанный из 28-ой трубы, с предыдущей трубой он соединяется при помощи болта М12. Выглядит вся конструкция рычага так.
К верхней части трубы привариваем два уголка, а также из автомобильной камеры вырезаем круглый кусок резины, который закроет острые края уголков. В уголке просверливаем отверстие, при помощи которого будет стопориться колесо. К уголкам привариваем трубу меньшего диаметра, это будет служить упором в процессе забортирования/разбортирования.


Шаг четвертый.
К длинной трубе привариваем к одному из концов подшипник и уголок, на фотографии все куда понятнее.

Для данных целей отлично подошел подшипник с электродвигателя, правда от какого именно, не известно, была отпилена часть вала ротора с самим подшипником и приварена к трубе, после чего и сам уголок. К другому концу трубы привариваем закругленный наконечник, в данном случае была отпилена ножка кик-стартера мопеда, которая как раз подошла, при необходимости зашлифовываем острые края наждачной бумагой мелкой зернистости.
Шаг пятый.
После всех предыдущих действий остается сделать упоры. При помощи углошлифовальной машинки отпиливаем необходимые отрезки профилей 40*20 и устанавливаем в заранее изготовленные посадочные места с болтом для фиксации, для более лучшего крепления просверливаем в профиле отверстие под болт, так он точно никуда не денется.


В удобном для вас месте устанавливаем крепежные ушки, в моем случае были приварены две точки крепления на столбах пристройки.
На этом у меня все, данный шиномонтажный станок полностью готов и работает в полной мере.


Желаю всем удачи и спасибо за внимание.
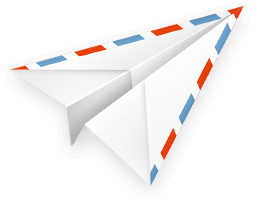
Получайте на почту подборку новых самоделок. Никакого спама, только полезные идеи!
*Заполняя форму вы соглашаетесь на обработку персональных данных
Становитесь автором сайта, публикуйте собственные статьи, описания самоделок с оплатой за текст. Подробнее здесь.