Очистка воздуха от масла: очищаем сжатый воздух правильно!
Для повышения надежности функционирования и долговечности пневматических систем управления необходим целый комплекс мероприятий. Очень важной при этом является оптимальная подготовка сжатого воздуха, включающая в себя его очистку от разнообразных загрязнений. Очистка воздуха от масла нужна потому, что загрязнения сжатого воздуха в 3-7 раз снижают долговечность пневматического оборудования и в 80% случаев являются причиной выхода его из строя.
Загрязнения сжатого воздуха
Условно загрязнения сжатого воздуха компрессорного оборудования можно разделить на три больших группы: твердые загрязнения, газообразные загрязнения, вода и компрессорное масло в жидкой, а также паровой фазе.
К появлению этого нежелательного компонента в сжатом воздухе могут привести смазка компрессоров и пневматических устройств, масляные фильтры, а также пары и распыленное масло в окружающей среде.
Пожалуй, наибольшие трудности возникают при удалении тумана компрессионного масла. Это связано с небольшим размером аэрозольных частиц, подавляющее большинство из которых имеет диаметр меньше 1 мкм. В процессе сжатия воздуха, содержащего примеси масла, в камере появляется масляный туман, в состав которого входят капли размером 1,0 мкм и распыленный аэрозоль с размером частиц 0,01 мкм и даже меньше. Также отмечают наличие масляных паров (газовой фазы).
Все эти примеси уносятся вместе с воздушным потоком. Концентрация масляного тумана в сжатом воздухе может доходить до 1 г/м3. В целом она зависит от общих характеристик используемого масла, а также типа и особенностей конструкции компрессоров. Если говорить о масле в общем, то стоит отметить, что его содержание в сжатом воздухе может достигать нескольких десятков граммов на один кубический метр.
Фильтры для очистки
На практике для очистки сжатого воздуха от масла применяют специальные фильтры. При их производстве могут использоваться разнообразные материалы, включая композитные. Наиболее часто применяют: агломераты бронзы и нержавеющей стали, гидрофобные мембраны, пропитанные смолой волокна целлюлозы, керамику и кварцит, полимерные материалы и микроволокна боросиликата с или без связующей добавки.
Выбор конкретного материала производится в зависимости от характера загрязнений и требований к технологическому процессу.
На рынке имеются мембраны, которые могут помочь создать фильтры различной степени очистки воздуха, включая стерильную или ультрачистую
Для удаления масла также могут быть использованы коалесцентные фильтры. Если сжатый воздух, содержащий микрокапли примесей, пропустить через пористую субмикронную мембрану, то возникнет явление коалесценции. Его суть состоит в том, что микрокапли начинают вступать в контакт и объединятся. В результате появляются большие капли, постоянно увеличивающиеся в размерах. Поток воздуха их выталкивает и появляется возможность сбора с другой стороны пористой мембраны.
Выделенную жидкость аккумулируют на дне емкости фильтра до полного удаления или вручную, или автоматически с помощью специальных сливов.
Наиболее эффективные марки коалесцентных картриджей помогают снизить содержания масла в сжатом воздухе до 0,01 ppm (частей на миллион, обычно выраженных в весе). Пары масла с помощью данного оборудования не могут быть удалены, поэтому дополнительно нужно использовать специальные адсорбенты.
Кроме фильтрации для очистки от сжатого воздуха используют также процесс осушки и силовые поля. Существующие установки могут объединять в себе несколько способов очистки.
Избежать попадания в сжатый воздух масла можно в том случае, если используется
Также для производства безмасляного воздуха могут быть использованы спиральные компрессоры.
Процесс очистки сжатого воздуха от масла
В компрессоры попадает воздух, содержащий загрязнения в виде твердых частиц. Возможно также наличие некоторого количества водяного пара, который в случае сжатия может конденсироваться и образовывать загрязнения в жидкой фазе. Не исключено присутствие и газообразных загрязнений.
Сам процесс сжатия сопровождается загрязнением маслом и водой. Степень загрязнения сжатого воздуха маслом зависит от конструкции и текущего состояния компрессора.
Согласно существующим данным, наличие в таком воздухе загрязнений различного происхождения способно в 3-7 сокращать срок службы пневмооборудования.
Масло является очень неприятной примесью, так как его удаление вызывает наибольшие трудности, особенно если оно пребывает в сжатом воздухе в виде аэрозоля с частицами размером 0,01-1 мкм.
Именно из-за небольшого размера использование сил инерции в этом случае не подходит. Поэтому на практике применяют фильтры контактного действия или коалесцентные.
В общем случае фильтровальный элемент имеет несколько слоев. Первый – мелкопористый. Проходя через него, частицы масла соединяются. Происходит их укрупнение (явление коалесценции). Второй слой – грубоволокнистый. В нем происходит расширение воздуха. На выходе скорость движения потока существенно снижается, а капли масла, пребывая под воздействием собственного веса, начинают опускаться на дно специального стакана. В нем предусмотрено наличие крана, с помощью которого происходит периодический отвод водомасляного конденсата.
Некоторые промышленные области не допускают наличия в воздухе аэрозолей, поскольку данный факт ухудшает качество производимой продукции или же делает протекание технологического процесса вообще невозможным.
Именно для таких случаев предусмотрено применение специальных фильтров-глушителей. Они более сложны по конструктивному исполнению и имеют значительные габариты. В связи с этим фильтры-глушители устанавливаются на выхлопном трубопроводе, являющимся общим для всей пневмосистемы.
Также для удаления масла из воздуха могут применяться системы химической очистки. В них используются специальные сменные картриджи.
Установки для очистки атмосферного воздуха
Эта задача может возникать, например, при продувке баков силовых трансформаторов и электрических аппаратов при их монтаже, обслуживании и ремонте. Конечная цель такой операции – это предохранение электроизоляции от увлажнения во время разгерметизации активной части. Таким образом, воздух, который для этого используется, должен быть чистым и не содержать ни масла, ни механических примесей, ни воды. Для очистки на практике применяют специальные установки типа «Суховей-4».

Установка осушки воздуха Суховей-4
Принцип их работы базируется на осушке атмосферного воздуха в двух адсорберах, которые работают циклически. Они заполнены синтетическим сорбентом для очистки осушенного воздуха от механических примесей в фильтре.
Очистка атмосферного воздуха от примесей другого рода может осуществляться механическими, физическими или физико-химическими методами.
Очистка сжатого воздуха от масла, способы.
Для многих предприятий использующих сжатый воздух в качестве энергоносителя, следовательно, использующих компрессорное оборудование, возникает вопрос с очисткой сжатого воздуха от твердых примесей, масла и воды.
Если с очисткой воздуха от твердых примесей и влаги вопросов не так много, то с очисткой от компрессорного масла возникают сложности.
Рассмотрим несколько способов борьбы с маслом в сжатом воздухе:
1. Использования нескольких фильтров
2. Системы каталитической очистки
3. Использование безмасляного компрессора
При использовании масляного компрессора, сжатый воздух содержит частицы компрессорного масла, содержание масла может достигать 3-4 мг/м3. Обычно для очистки от масла используют ряд фильтров, от грубой очистки к более тонкой. Получается, примерно 4-5 фильтров подряд. Данным способом можно добиться концентрации примерно 0,01 мг/м3.
Данный вариант, использовать фильтры сжатого воздуха, дешевле на этапе покупки оборудования. Но в перспективе на несколько лет оказывается не таким и дешевым. Рассмотрим более подробно.
Каждый фильтр содержит фильтрующий элемент, который периодически требует замены. Чем грязнее сжатый воздух, тем быстрее загрязняется фильтрующий элемент, а это значит, замена должна происходить достаточно часто. Стоит отметить, что загрязняясь, фильтрующий элемент, постепенно теряет свою способность фильтровать частицы масла, пыли. В итоге качество сжатого воздуха, который поступает потребителю, становится не лучшего качества, что сказывается на конечном изделии. В среднем замена фильтрующих элементов происходит раз в 4-6 месяцев, при 8 часовой рабочей смене.
Дополнительно следует учесть, что на каждом фильтре происходит потеря давления, от 0,05 до 0,3 атм., в зависимости от производителя и степени очистки. С учетом потерь давления на фильтрах, возможно, потребуется использование более мощного компрессора, для компенсации потерь давления. Посчитав все затраты и риски, использование только фильтров, для
Вторым способом очистки сжатого воздуха являются системы каталитической очистки. В основе работы лежит химико-физический процесс, в результате которого компрессорное масло и другие углеводороды превращаются в воду и углекислый газ. Данные системы позволяют получать сжатый воздух с остаточной концентрацией масла менее 0,01 мг/м3.
Данные системы имеют сменный картридж, имеющий длительный срок службы, примерно 10-15 тысяч часов работы. При этом эффективность работы установки на протяжении всего срока службы картриджа не изменяется. Необходимо заметить, что данная система позволяет очистить сжатый воздух только от масла. Для очистки от твердых примесей и воды, потребуется дополнительная установка фильтров и осушителя. Данные системы зарекомендовали себя довольно успешно. Необходимо отметить, что
Стоимость систем каталитической очистки гораздо выше, нежели использование одних фильтров. К тому же замену сменного картриджа необходимо проводить, примерно, раз 1,5-2 года, при 24 часовой рабочей смене. Стоимость картриджа достаточно высока.
Рассмотрим третий способ борьбы с маслом в сжатом воздухе, использование компрессора безмасляного. При использовании безмасляного компрессора, в сжатом воздухе отсутствуют примеси компрессорного масла, поэтому необходимости очистки от масла просто нет.
Можно выделить несколько типов безмасляных компрессоров, применяемых на производстве:
а) спиральные компрессоры
б) винтовые компрессоры «сухого» сжатия
в) винтовые компрессоры с впрыском воды в камеру сжатия
г) поршневые компрессоры.
Указанные выше компрессоры не используют в процессе сжатия компрессорное масло. Спиральные компрессоры имеют две спирали, одна – внутренняя закреплена неподвижно, вторая – внешняя, вращается вокруг первой. Данные компрессоры характеризуются низким уровнем шума. Малыми затратами на техническое обслуживание. Все обслуживание сводится к регулярному осмотру и периодической замене воздушного фильтра, приводных ремней и уплотнителей между спиралями.
Винтовые компрессоры сухого сжатия, как и обычные компрессоры, имеют винтовую пару. Основное различие процесс сжатия происходит в «сухую». Особенностью данных моделей является высокий температурный режим, как следствие повышенный износ агрегатов. Компрессоры «сухого» сжатия требовательны к окружающим условиям и техническому обслуживанию.
Винтовые компрессоры с впрыском воды в камеру сжатия. Компрессоры так же имеют винтовую пару, но вместо масла в камеру сжатия подается вода, которая служит для отвода тепла. Компрессоры характеризуются низкими требованиями к окружающей среде, не дорогим техническим обслуживанием. Использование воды, позволяет уменьшить количество твердых примесей в сжатом воздухе по сравнению с окружающей средой, в связи с данным фактом уменьшается количество фильтров, необходимых для очистки сжатого воздуха от твердых примесей.
Отсутствие в сжатом воздухе примесей компрессорного масла, полностью избавляет от необходимости использования систем очистки, или комплекса фильтров для сжатого воздуха,уменьшая тем самым затраты связанные с обслуживанием дорогостоящих систем, в том числе и за счет уменьшения потребления электроэнергии.
Рассмотрев несколько вариантов очистки сжатого воздуха от масла, самым оптимальным способом является отсутствие масла в сжатом воздухе, а именно использование безмасляного компрессора. Не смотря на то, что инвестиции в оборудование, на первоначальном этапе будут более высокие, в перспективе на 10-15 лет, использование безмасляного компрессора более выгодно, за счет экономии средств на очистке сжатого воздуха от масла.
Способы удаления воздуха из гидравлической жидкости
Присутствие воздуха в жидкости может вызвать различные неполадки в работе гидравлической и смазочной систем:
- Высокий уровень шума и вибраций;
- Нехарактерные для агрегата звуки;
- Замедленное перемещение исполнительных механизмов;
- Повреждение гидроузлов;
- Снижение качества жидкости.
Типовые устройства для удаления пузырьков из жидкости основаны на принципе механического извлечения воздуха. Применение такого оборудования позволяет сократить размеры гидравлического бака и общую стоимость гидросистемы.

Удаление воздуха методом кавитации
Эффект кавитации возникает при положительной разнице между давлением, действующим на жидкость, и давлением насыщения газа, содержащегося в жидкости. Попадание в область высокого давления пузырьков, растворенных в жидкости, приводит к их разрушению. При определенных показателях давления в гидравлическом насосе, данный эффект может вызвать сильные вибрации, высокий уровень шума и термические деградации жидкости.
Пузырьки газа чаще всего находятся на поверхности в пенообразной консистенции, но некоторые пустоты могут оставаться в толще масла. Пузырьки, находящиеся в жидкости или гидробаке, могут быть поглощены насосом, где они сначала увеличиваются в размерах из-за пониженного давления, а затем уменьшаются при попадании в область высокого давления. Процесс является практически адиабатическим, т.е. нагретый пузырек повышает температуру жидкой среды лишь незначительно. Как следствие, высокие температуры сосредоточены только на поверхности области газ-жидкость, что влечет за собой перегрев масла.
Почему воздух попадает в гидросистему?
Причины такого процесса могут быть следующие:
- Сопротивление всасыванию;
- Снижение давления при прохождении жидкости через отверстия, рукава и трубы;
- Турбулентность, возникающая вследствие открытия и закрытия клапана;
- Резкое закрытие клапана или остановка работы насоса, что приводит к сильным вибрациям;
- Резкое открытие клапана, вызывающее падение давления в системе;
- Внешнее воздействие на гидроцилиндр;
- Жидкость залита в гидронасос в недостаточном количестве.
В смазочных системах часть жидкостной массы, проходящей через подшипники и шестерни, может приобретать пенообразную структуру. Подобные процессы являются нежелательными для гидросистем, поскольку могут привести к увеличению шума и сопровождаться кавитацией.
Эффект кавитации также может увеличить степень окисления масла. Повышение температуры, возникающее в результате сжатия, с высокой долей вероятности приведет к возгоранию воспламеняющихся веществ, если они присутствуют в пузырьке газа. Процесс горения продлится наносекунды, но на локальном уровне температура может подняться до 1000 градусов Цельсия и выше. Данное явление получило название «микро-дизель» и может стать причиной окисления масла. Этот эффект, в свою очередь, вызывает резкие перепады давления, а также квитанционную эрозию гидронасоса и прочих узлов гидравлической системы.
Кавитация часто также становится причиной появления промежуточных химических соединений, способных оказать сопротивление восстановительным процессам.
Присутствие пустот в гидравлике также может вызвать следующие проблемы:
- Увеличение температуры масла;
- Снижение качества жидкости и смазывающих свойств;
- Низкая теплопроводность;
- Высокие и нехарактерные шумы;
- Снижение коэффициента упругости;
- Потеря производительности насоса.

Новые технологии для удаления воздуха из жидкости
Лучше всех в разработке технологий для удаления пузырьков преуспела компания «Opus System, Inc», которая создала уникальную систему под названием «Bubble Eliminator». Устройство представляет собой цилиндрическую камеру, в которую помещена конусовидная трубка с круглым поперечным сечением. Жидкость с пустотами перемещается в аппарат под прямым углом и при выходе из трубки образует закрученный поток, циркулирующий через проточный канал. Ускорение потока постепенно уменьшается, вместе с ним и снижается давление масла вдоль центральной оси. В конечной части трубки вихревой поток постепенно замедляется, значение давления возвращается на оптимальный уровень, в результате чего жидкость перемещается на выход.
Показатель центробежной силы определяется значением преодолимого расстояния. В вихревом потоке образуется разница значений центробежной силы, что обеспечивает перемещение жидкости с пустотами в сторону центральной оси. В закрученном потоке, циркулирующем в центре, наблюдается самое низкое давление. Это приводит к образованию воздушного столба из небольших пузырьков. Далее они покидают аппарат через клапан.
Результатом данного процесса является удаление пузырьков из гидравлической системы. Снижение пропорций содержащегося в жидкостной массе газа позволяет жидкости растворять газ в больших объемах. Следовательно, масса всасывает больше пузырьков, которые впоследствии покидают систему при помощи технологии Bubble Eliminator.
Испытания показали, что аппарат можно подсоединять на линии слива и использовать для удаления пустот из гидравлической жидкости. В отличие от других разработок, данная технология не вызывает кавитацию и неисправности агрегатов.
Заключение
Инновационная система для удаления воздуха имеет следующие выгоды перед аналогами:
- Сокращение объема гидробака;
- Минимизация деградации жидкости продлевает срок её службы;
- Отсутствие шумов в гидравлическом насосе;
- Снижение степени сжатия жидкости.
По всем вопросам касаемо работы гидравлического оборудования обращайтесь за консультацией к специалистам компании «Гидротехтрейд».
← Предыдущая статья Следующая статья →РЕМОНТ И ОБСЛУЖИВАНИЕ
ЛЮБОЙ ГИДРАВЛИКИ
О воде в масле и о том, как от нее избавиться – Основные средства
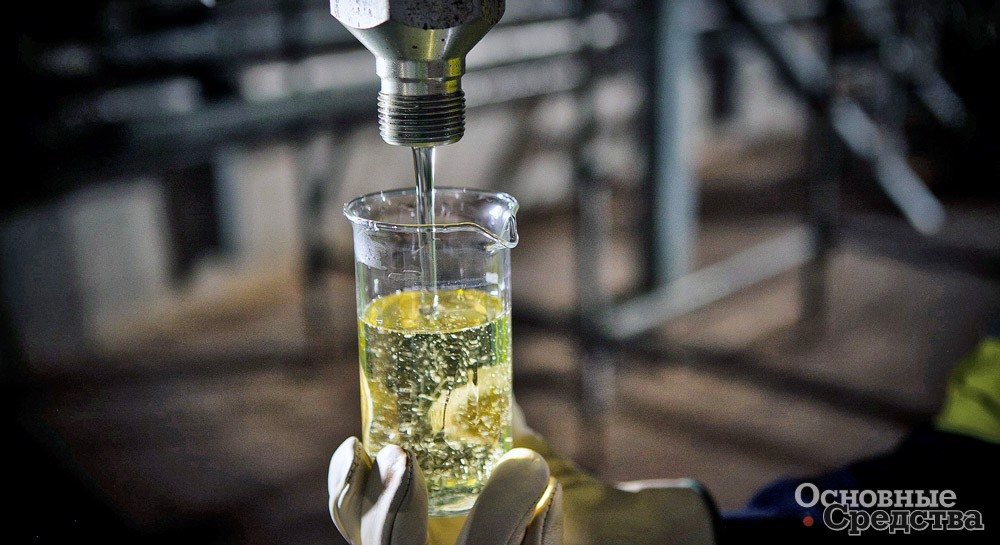
Как сделать масло «масляным»?
Мы уже не раз публиковали материалы по различным вопросам, относящимся к использованию и свойствам смазочных материалов для тяжелой специальной техники. Начиная с данного номера журнала редакция «ОС» планирует предложить вниманию читателей новую серию статей «Смазочные материалы: полезные сведения и рекомендации». Открывает серию публикация по одной из важнейших проблем – удаление воды из масла.
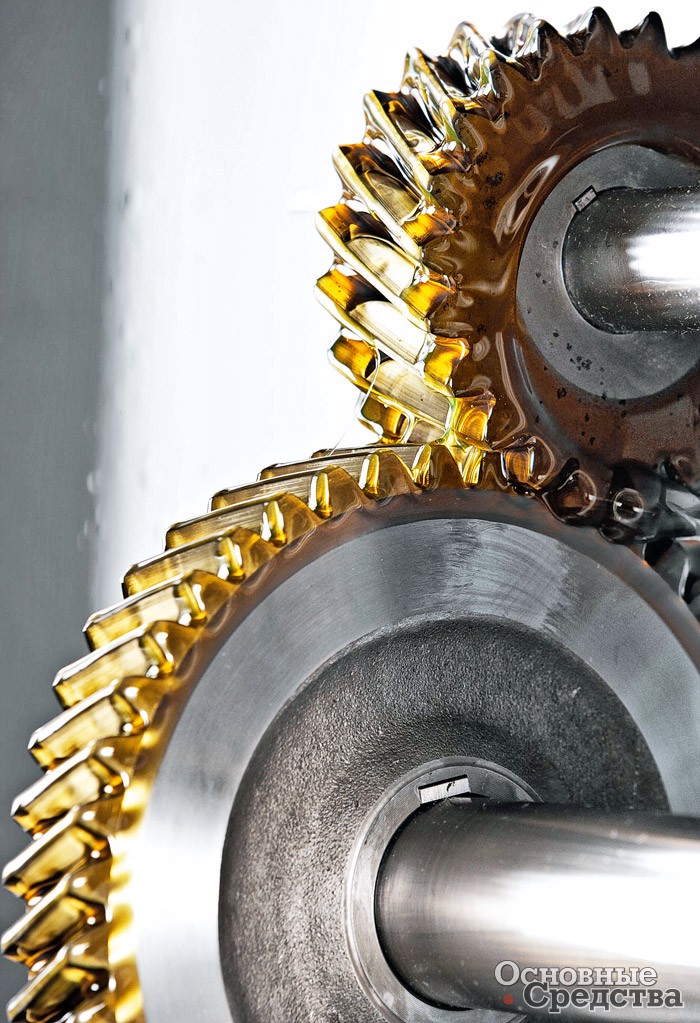
Вода, вода, кругом вода… Так поется в одной старой песне. Вода в природе присутствует повсюду, окружает нас со всех сторон. И если только вы не живете в мертвой, выжженной солнцем пустыне, это неоспоримый факт жизни.
Вода в смазочных, трансмиссионных и гидравлических маслах неблагоприятно влияет на их рабочие характеристики и поэтому считается загрязнением. Поговорим о проблеме очистки масел от попавшей в них воды.
Причины попадания воды в масло и меры по его предотвращению
Воду в масле часто называют подлинным бедствием для машин и механизмов. Как известно, попавшая в масло вода может находиться в различных состояниях: свободном, эмульгированном или растворенном. Даже в свежем масле всегда присутствует некоторое количество воды в растворенном состоянии. Вода может проникать в масло постепенно и незаметно в результате конденсации влаги из атмосферы либо быстро и одномоментно, например, в результате разрушения уплотнения крышки емкости с маслом или попадания в бак струи воды при мойке машины. Увеличивается вероятность попадания воды в смазочные материалы машины, если техника работает под открытым небом, например, на строительстве и в горнодобывающих карьерах, или если машины часто моются, как те, что перевозят пищевые продукты или сырье для их производства. Например, вода может проникать в картер дифференциала моста через уплотнения при въезде в глубокую лужу: разогретое масло и картер остывают, внутри картера создается разрежение, и вода всасывается внутрь через манжеты. Вообще же загрязнение смазочных масел водой имеет место практически во всех отраслях промышленности.

Если обнаружилось загрязнение масла водой, прежде всего следует постараться выяснить, как она попадает в картер двигателя или трансмиссии, и устранить причину загрязнения. Это избавит вас от повторения этой проблемы в будущем и от новых затрат на материалы, рабочую силу и запчасти, ведь простая замена загрязненного масла не устраняет причины попадания воды в масло.
Мероприятия по предотвращению попадания воды в масло следует начинать еще на складе нефтепродуктов. Бочки и цистерны для масел должны быть защищены от неблагоприятных воздействий окружающей среды, особенно в тех регионах, где высокая влажность воздуха. Даже в помещении емкости с маслом должны быть надежно укрыты от попадания струй воды при мойке помещения или, например, при проверке системы пожаротушения. Емкости с маслом не должны напрямую сообщаться с атмосферой: сапуны емкостей должны быть оснащены фильтрами – поглотителями влаги, особенно если масла хранятся в условиях повышенной влажности.
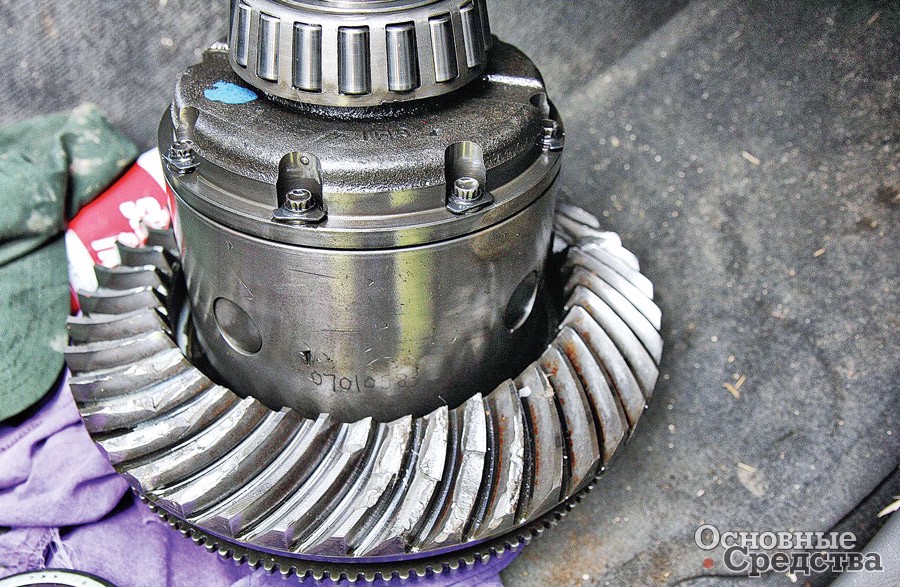
Для машин специалисты рекомендуют такие меры, как использование фильтров-осушителей воздуха в сапунах картеров, чтобы задерживать любые самые незначительные количества влаги, которая могла бы конденсироваться на внутренних поверхностях картера при понижении температуры. В картерах и кожухах не должно быть никаких открытых отверстий и лючков, их следует загерметизировать. В осенний и весенний периоды, когда велика влажность и разница между рабочими температурами агрегатов машин и окружающего воздуха, а также между дневной и ночной температурами, при понижении температуры до точки росы влага из воздуха начинает конденсироваться внутри картеров агрегатов, а днем, если температура будет низкой, влага не улетучивается из картера.
Если вода попадает в масло из-за неисправности уплотнений валов, штоков и крышек, уплотнения следует заменить как можно быстрее. Следует обучать операторов и специалистов по сервису правильным приемам мойки машин: струя воды не должна быть чрезмерно мощной, необходимо следить, чтобы струи воды не попадали непосредственно на уплотнения валов, штоков, заправочные горловины и сапуны узлов машины.
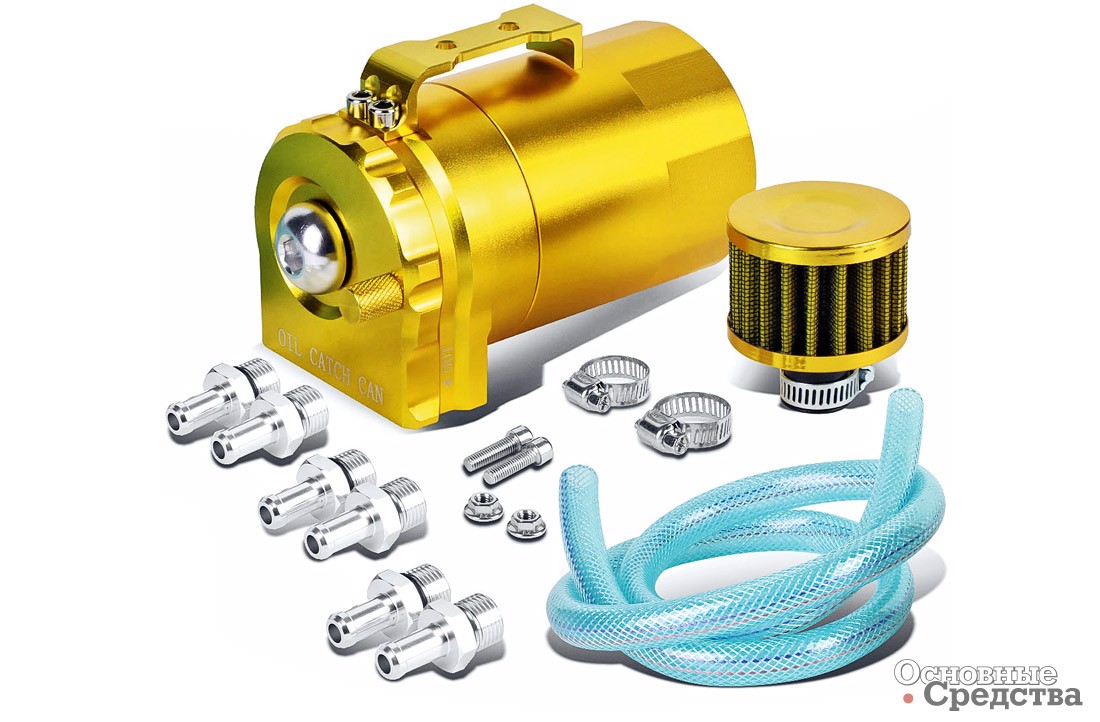
Рекомендуется следить за состоянием масла в мерных стеклах – указателях уровня масла в картере и периодически проверять фильтры-отстойники, не забывать сливать отстой через сливные краны. Если сливного крана нет или он неисправен, рекомендуется отремонтировать или установить новый. Можно порекомендовать сливать отстой из картеров агрегатов машины регулярно, каждый день и записывать количество слитого отстоя. Агрегаты, из которых отстоя сливается больше всего, необходимо тщательно проверить и выяснить причину, заменить в них фильтры – осушители сапунов.
В картерах больших стационарных машин (например, дизель-генераторов) иногда рекомендуют поддерживать избыточное давление, чтобы исключить поступление воздуха (и влаги в нем) извне. Однако данную рекомендацию следует использовать осторожно: во-первых, может начать выдавливать масло наружу через уплотнения, а во-вторых, централизованная система подачи воздуха обходится недешево, и если в системе возникнет хотя бы небольшая утечка воздуха, расходы на эксплуатацию этой системы возрастут еще больше.
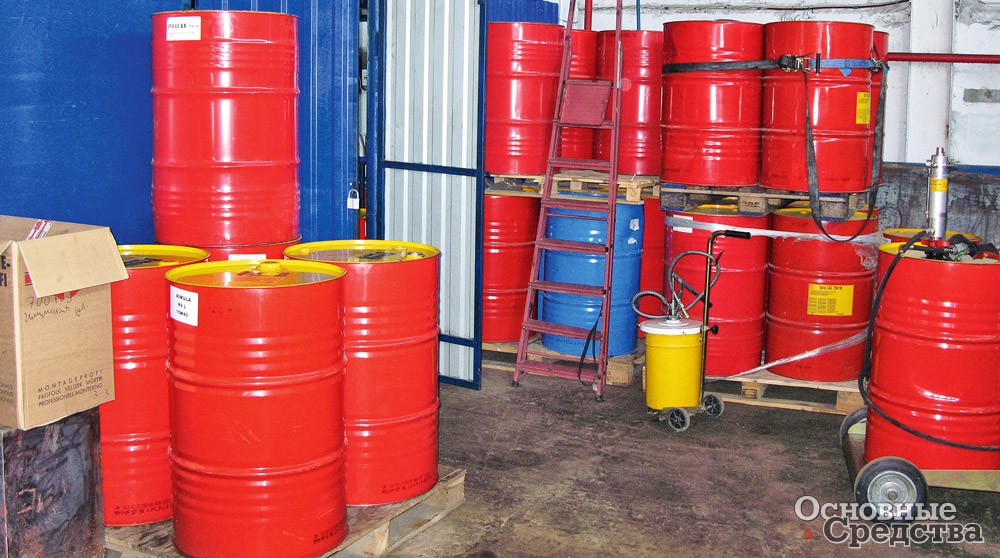
«Точка насыщения масла водой»
Вода практически всегда присутствует в масле просто потому, что масло соприкасается с атмосферным воздухом. Воду, растворенную в масле на молекулярном уровне, нельзя увидеть невооруженным глазом. Масло внешне может выглядеть совершенно чистым, прозрачным и красивым. Однако если содержание воды в масле близко к «точке насыщения» (т. е. содержание растворенной воды в масле близко к максимальному количеству, которое способно удержать масло), при понижении температуры растворенная вода может переходить в эмульгированное или свободное состояние и создавать молочно-белое помутнение в масле. Поскольку эмульгированная и свободная вода наносит более существенный вред, чем растворенная, то содержание воды всегда должно быть ниже предела насыщения. Однако и растворенная вода может причинить ущерб.
Значение «точки насыщения» зависит от типа и температуры масла, его срока службы и состава пакета присадок. Для каждого типа масла существует свой предел насыщения, при котором растворенная вода переходит в эмульгированное или свободное состояние. Эмульгированная или свободная вода также может переходить в растворенное состояние при повышении температуры масла.
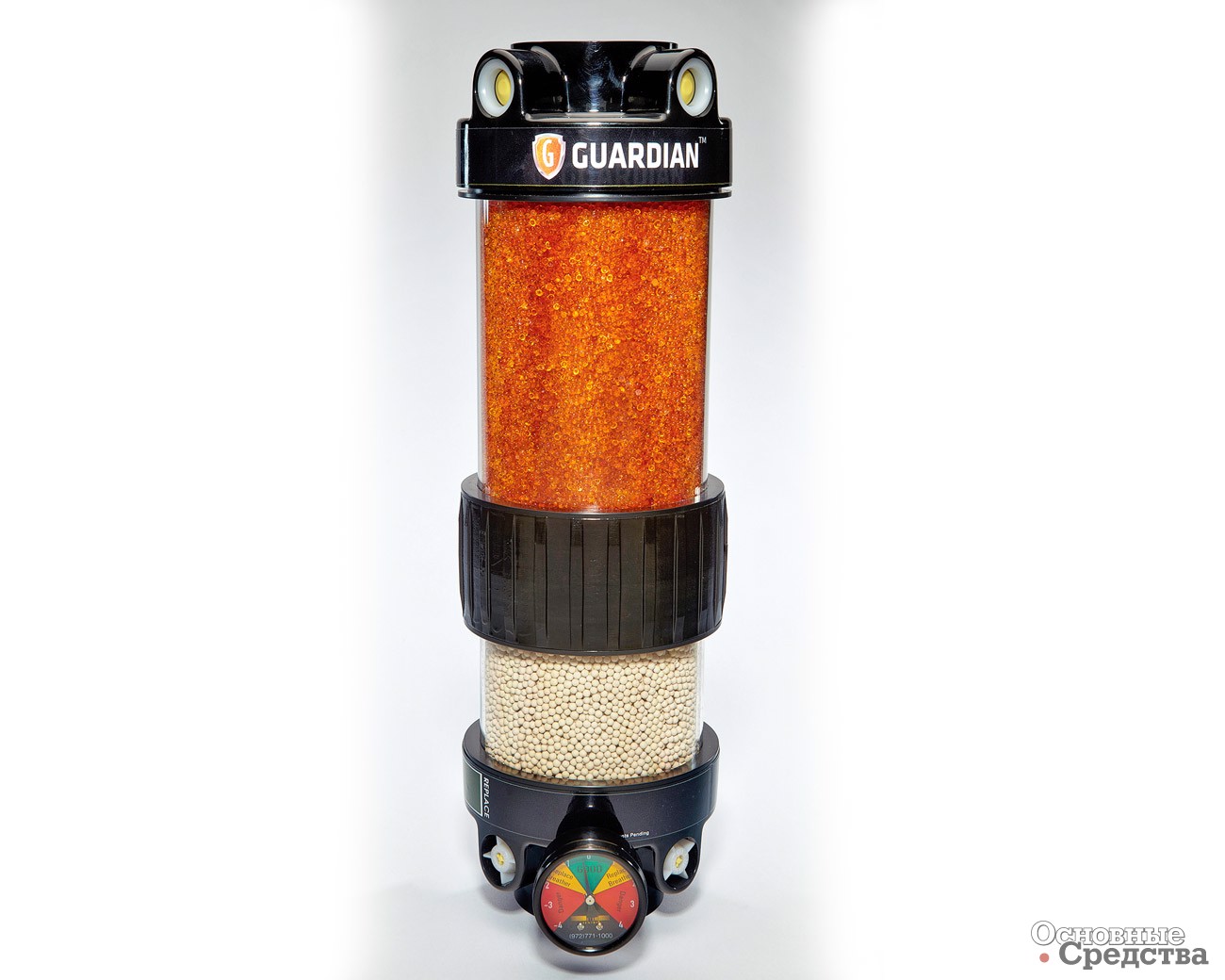
Например, полигликолевые масла, которые составляют около одной трети всех синтетических масел и обозначаются по классификации DIN буквами PG. Полигликолевые масла используются в качестве моторных, авиационных и в других сферах. Полигликоли изготавливаются из смеси этилена и пропилена, обычно в соотношении 50:50 или 60:40. От этого соотношения зависит гигроскопичность и способность масла растворять воду. Если соотношение равно 1:1, масло может абсорбировать до 10% влаги при обычной температуре и относительной влажности 80%. Поэтому следует хорошо проанализировать все условия эксплуатации, прежде чем выбирать полигликолевое масло для использования в машине.
Чем выше температура масла, тем выше значение точки насыщения, и следовательно, больше воды может содержаться в масле в растворенном состоянии. Чем больше срок службы масла, тем большее количество воды можно в нем растворить. Это объясняется присутствием ионизированных продуктов окисления масла, которые действуют как «крючки», удерживающие молекулы воды в растворе. Масла с высоким содержанием присадок, такие, как моторные и трансмиссионные, имеют более высокую точку насыщения по сравнению с маслами, у которых содержание присадок невысокое (например, турбинные масла), поскольку присадки, многие из которых имеют ионизированные молекулы, также имеют свойство удерживать молекулы воды в растворенном состоянии в масле.
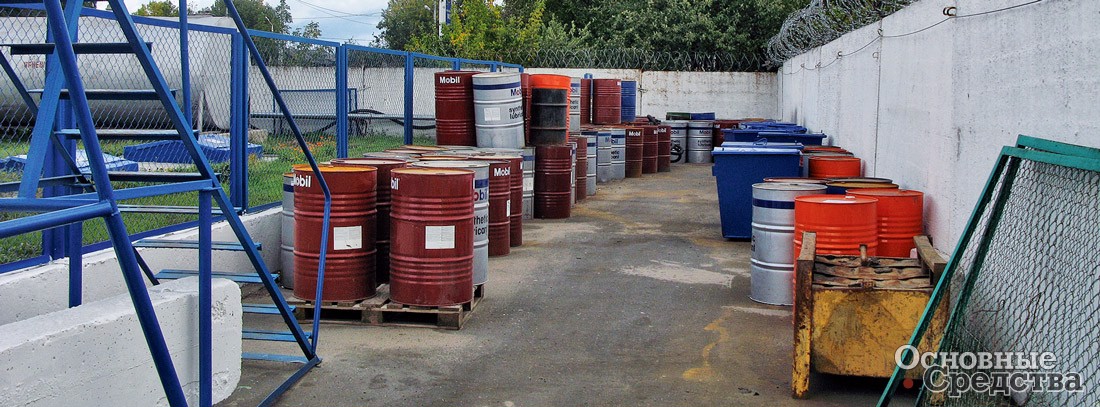
Вредное воздействие воды
Вода оказывает вредное влияние как на само масло, так и на машину. Вода способствует окислению базового масла, изменению его вязкости и пенообразованию (аэрации), что в свою очередь приводит к уменьшению прочности масляной пленки и ускорению износа трущихся деталей. Вода также может оказывать негативное воздействие на пакет присадок: вымывать некоторые присадки, неустойчивые к действию влаги, способствовать гидролизу (расщеплению) присадок, что приводит к образованию высококоррозионных кислот и истощению присадок. Вода является источником возникновения в масле таких загрязнений, как парафины, суспензии, углеродные и окисные нерастворимые загрязнения и даже микроорганизмы.
Вода нанесет серьезный ущерб любому узлу машины, в который попадет вместе с маслом. В двигателях внутреннего сгорания, которые работают на высоких скоростях и при высоких температурах, состояние масла следует контролировать очень тщательно. Вода усиливает процессы ржавления и коррозии, в результате водородной коррозии возникает вспучивание и охрупчивание стали, а также питтинг в результате паровой кавитации. Если же в масле содержатся кислоты, то при совместном воздействии воды с кислотами коррозионное воздействие на черные и цветные металлы усиливается.
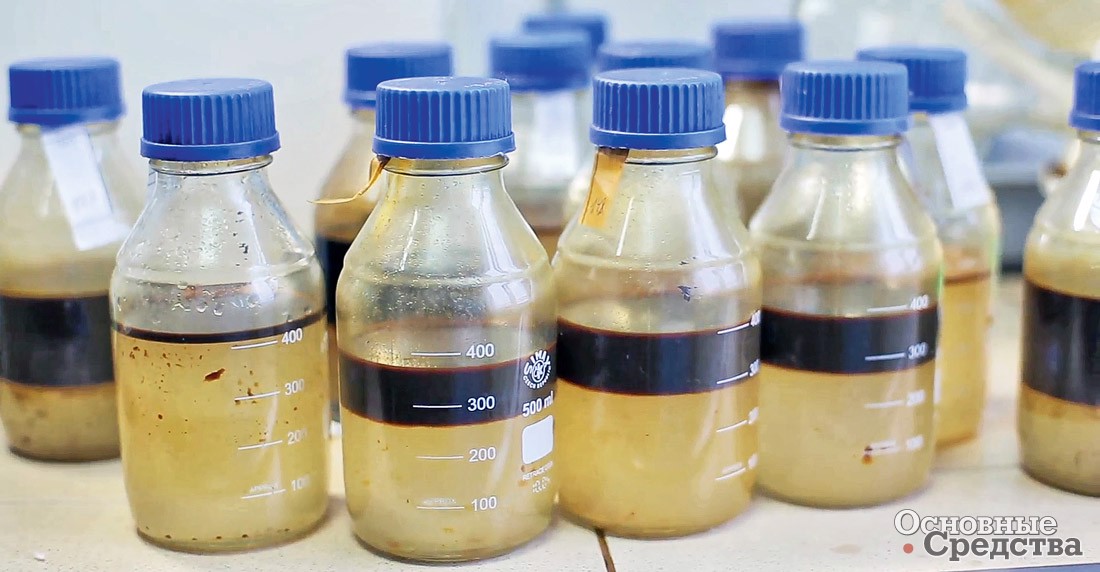
Определение содержания воды в масле
Специалисты рекомендуют сокращать содержание воды в масле до самого низкого уровня, какого только можно достигнуть при разумных затратах, предпочтительно, чтобы содержание воды было ниже точки насыщения при рабочей температуре масла. Существует много способов и приборов для определения содержания воды в масле, а также рабочих характеристик масла. Характеристики понадобятся вам при определении пригодности масла для дальнейшего использования. Выбор метода зависит от того, содержание какой формы воды в масле нужно определить – только растворенной или воды во всех формах, т. е. кроме измерения содержания растворенной воды будет учтено и содержание несвязной воды.
Распространен метод инфракрасной спектроскопии с преобразованием Фурье (FTIR). Довольно точное определение содержания воды в масле обеспечивает титрование по методу Карла Фишера (ГОСТ Р 54284–2010; ASTM D6304). В практике используются еще простые методы, позволяющие предварительно оценить наличие воды в масле. Из наиболее широко используемых подобных методов можно назвать визуальный осмотр, «испытание на потрескивание» (ГОСТ 2477–2014) и метод виброцентрифуги (ГОСТ Р ИСО 3734–2009).
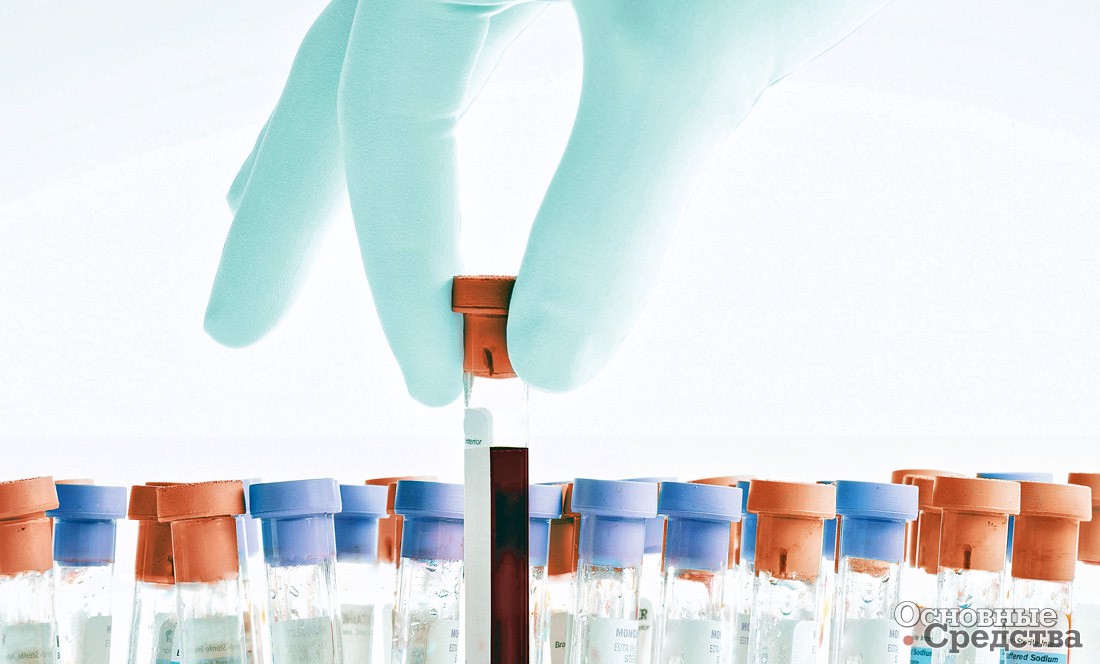
Проба на потрескивание заключается в нагревании испытуемого масла в стеклянной пробирке до заданной температуры. Имеющиеся в масле следы влаги переходят в парообразное состояние. При дальнейшем нагревании пузырьки пара, поднимаясь к поверхности масла, разрываются и потрескивают.
При использовании метода центрифугирования равные объемы масла и насыщенного водой толуола помещают в конусообразную пробирку для центрифугирования. После центрифугирования записывают объем высоковязкой воды и уровень осадка в нижней части пробирки.
Отметим, что применение метода центрифугирования для определения воды и осадка часто приводит к неправильным результатам, особенно когда для получения представительной пробы используют высокоскоростную мешалку. Настоящий метод не всегда дает удовлетворительные результаты, и количество определенной воды, как правило, ниже ее фактического содержания.
Более точными лабораторными методами определения содержания воды в масле являются метод дистилляции (ИСО 3733) и метод экстракции (ИСО 3735).
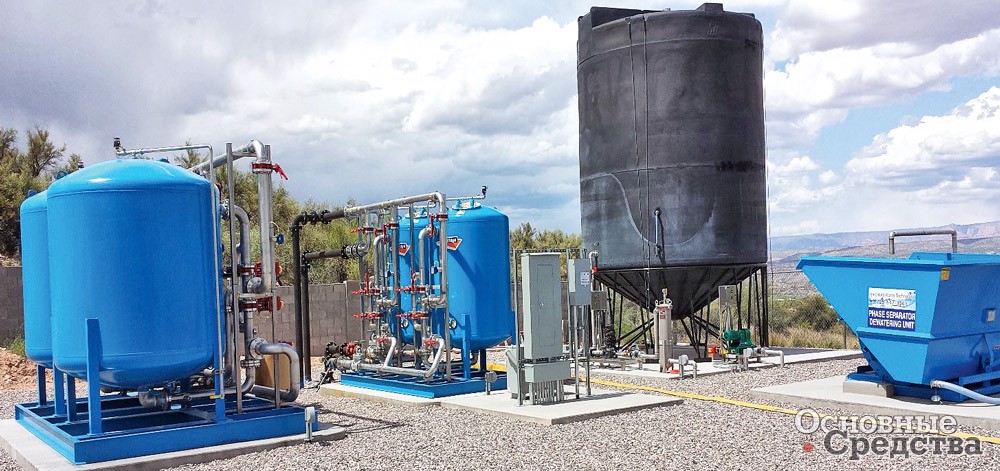
Технологии очистки масел от воды
Итак, как поступить, если в масло все же попала вода и просто утилизировать его нежелательно, чтобы не терять значительные средства. Перечислим ряд методов очистки масла от воды, их преимущества и недостатки.
Какая из технологий окажется наиболее эффективной в каждом данном конкретном случае, будет зависеть от того, какой процент содержания влаги в масле необходимо в итоге обеспечить, какой объем воды нужно удалить из масла и каков объем масла, каков тип базового масла (минеральное, синтетическое и т. д.) и какая производительность процесса очистки требуется. Как правило, чем больше воды попало в масло, тем сложнее будет ее удалить.
Отстаивание. Поскольку у воды удельный вес больше, чем у масла (за некоторыми исключениями), вода, присутствующая в масле в свободном состоянии («несвязная»), под действием силы тяжести стремится оседать на дно емкости, если ей дать достаточно времени и не взбалтывать. Увеличение температуры масла и использование резервуара-отстойника конусной формы помогают повысить эффективность метода разделения отстаиванием. Чтобы увеличить эффективность отстаивания загрязнений, необходимо понизить вязкость масла, поэтому иногда резервуары для отстаивания масел оборудуют подогревательными устройствами. Обычно применяют трубчатые, секционные или змеевиковые подогреватели, в которых теплоносителем служит водяной пар или горячая вода.
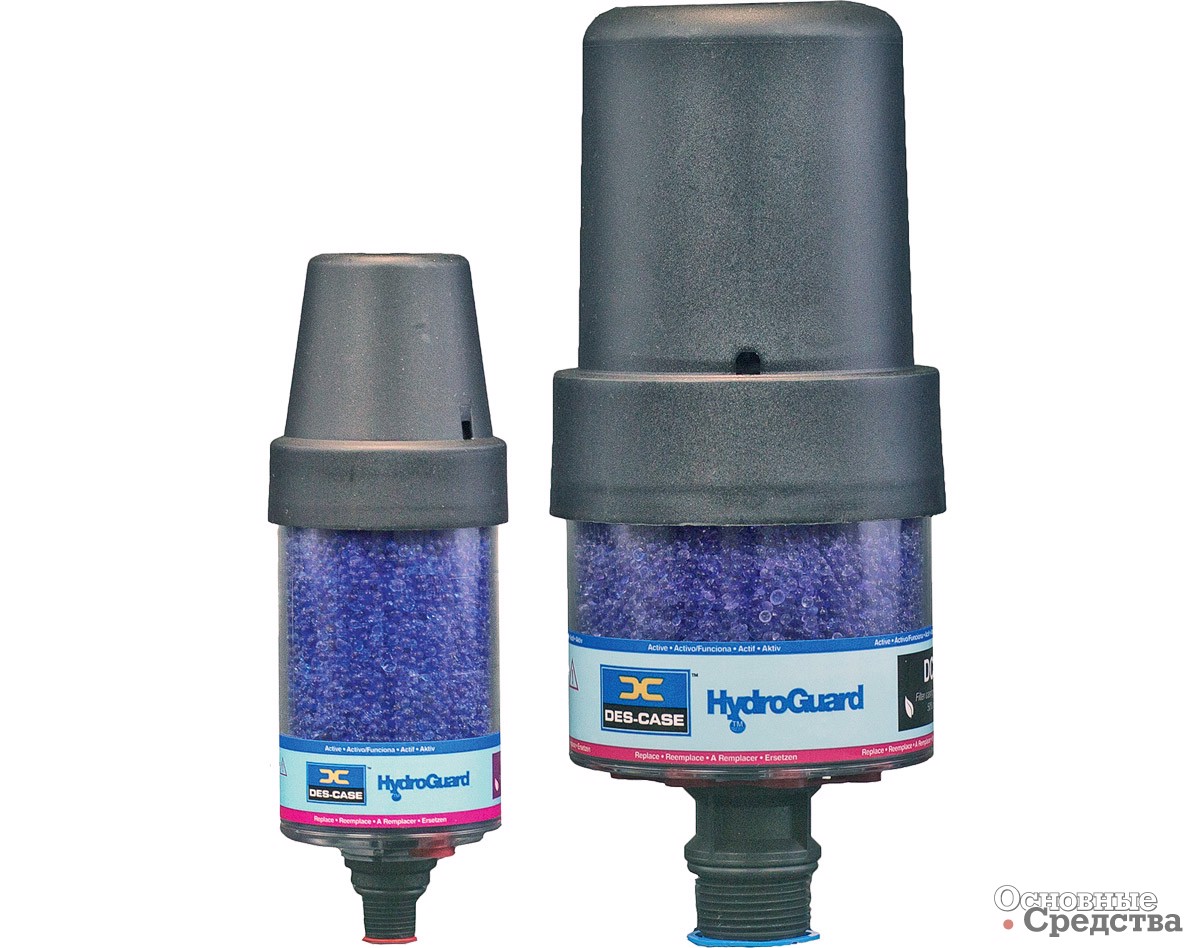
Будет ли оптимальным способ кратковременного подогрева масла, чтобы удалить из него воду и поддержать работоспособное состояние, остается пока вопросом, открытым для обсуждения. Но большинство специалистов сходятся во мнении, что позволить воде оставаться в масле намного более вредно для масла, чем его кратковременный нагрев. Поэтому выпускаются портативные системы удаления воды из масла с нагревательными элементами. В статичных системах, например в больших резервуарах, важно обеспечить плотность энергии таких нагревательных элементов ниже 0,775 Вт/cм2, чтобы свести к минимуму негативное тепловое воздействие на масло.
В некоторых случаях масло освобождается от примеси воды самостоятельно, потому что работает при повышенных температурах и вода из него испаряется. Масло в двигателе внутреннего сгорания демонстрирует наглядный пример такого самоочищения.
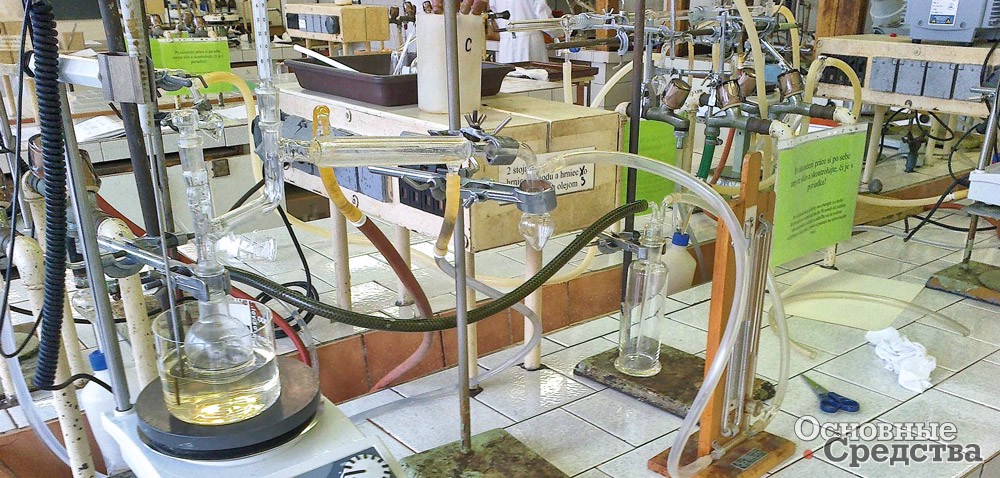
Недостаток метода с нагревом масла заключается в том, что нагрев необходимо тщательно контролировать, особенно это относится к минеральным маслам, чтобы избежать разрушения масла. Однако относительные затраты на очистку масла этим методом меньше, чем при использовании технологий центробежной и вакуумной сепарации (о них будет сказано ниже), поэтому данный метод может быть эффективным способом удаления воды из масла при определенных условиях.
Время, необходимое для отделения воды от масла, также зависит от состава пакета присадок, срока службы масла и типа базового масла. Например, для турбинного масла с небольшим содержанием присадок разделение способом отстаивания может быть оптимальным и позволит избавиться от большей части воды. Присутствие побочных продуктов окисления и арктических присадок, а также загрязнений уменьшает эффективность разделения масла и воды методом отстаивания. Некоторые масла обладают свойством удерживать воду в виде эмульсии и не давать ей отделяться – для таких масел способ отстаивания будет малоэффективным.
Иногда достаточно просто открыть сливной кран и слить отстоявшуюся воду и грязь из картера агрегата машины. Эффективность этой операции, однако, будет зависеть от того, на какой срок можно оставить машину в нерабочем состоянии, чтобы дать воде отстояться, и будет ли температура масла достаточно низкой, чтобы как можно большее количество воды в масле перешло в несвязное состояние. При больших объемах масла можно порекомендовать использовать специальные емкости, в которых масло может остывать, вода будет переходить из состояния эмульсии в свободное и оседать вместе с грязью.
Главным недостатком метода отстаивания является то, что он позволяет отделить лишь несвязную воду и отчасти в форме эмульсии, а вода в растворенном состоянии вся остается в масле. Преимуществом же является низкая стоимость этого процесса.
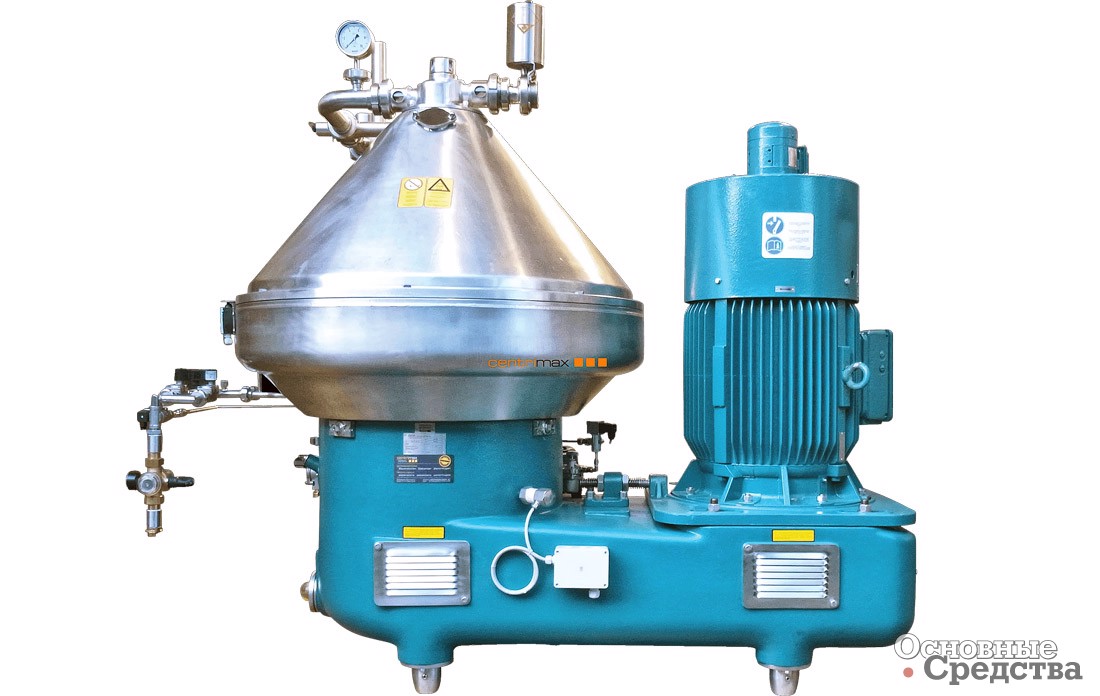
Разделение с помощью центрифуги. Принцип очистки методом центрифугирования основан на отделении от масла более тяжелых составляющих в процессе вращения, когда возникают высокие ускорения силы тяжести и вода, имеющая больший удельный вес, перемещается к периферии центрифуги. Чем больше разница значений удельного веса загрязняющего вещества и масла, тем более эффективно протекает процесс. Поэтому центрифуга лучше работает с маслами, у которых малый удельный вес и низкая вязкость, такими, как турбинные масла, а не с более тяжелыми трансмиссионными маслами.
С помощью центробежного сепаратора несвязная вода отделяется быстрее, чем методом отстаивания. Центробежный сепаратор – отличное средство для полнопоточной очистки технических жидкостей от загрязнений, и в том числе от воды. Эффективность отделения в какой-то степени зависит от состава пакета приставок, поскольку определенное количество воды содержится в масле в форме эмульсии.
Недостатками центрифугирования является то, что этот метод сравнительно дорог и от масла отделяется только вода в свободном состоянии. Частично можно отделять воду в эмульсированном состоянии в зависимости от соотношения устойчивости эмульсии и величины центробежной силы, которую развивает сепаратор, если обрабатывать масло при низкой температуре. Как и при отстаивании, чем ниже температура масла, тем большая часть воды будет находиться в эмульгированном и свободном состояниях, и следовательно, тем эффективнее будет процесс разделения воды и масла. Центробежные сепараторы не способны удалить из масла растворенную воду. В итоге, учитывая, что метод центрифугирования позволяет удалять из масла также иные тяжелые загрязнения и обеспечивает довольно высокую производительность по сравнению с другими технологиями, он считается экономически эффективным для применения в определенных ситуациях.
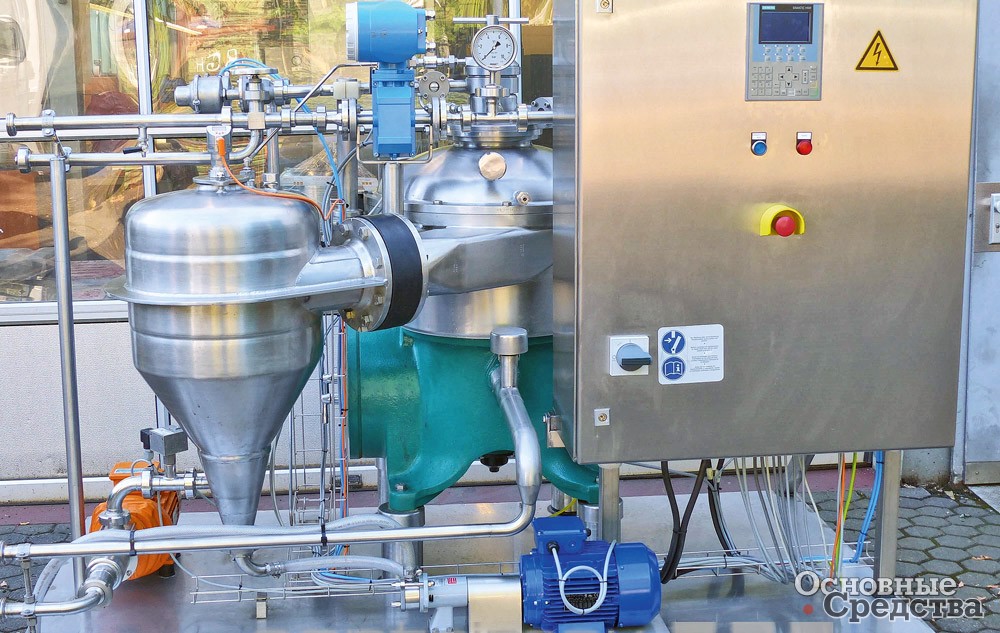
Вакуумная дегидратация (обезвоживание). Еще один способ – пропустить масло через вакуумный дегидратор (который иначе называется вакуумным дистиллятором). При вакуумной дегидратации в специальной установке снижают парциальное давление паров воды, что способствует отделению и удалению воды из масла. Снижение давления дает возможность воде (и другим летучим веществам) закипать при значительно более низких температурах.
Установки для перегонки под вакуумом работают таким образом: масло нагревается примерно до +65–70 °С, создается разрежение примерно 635–711 мм. рт. ст. При таком разрежении вода закипает при температурах 50–55 °С и начинает эффективно выпариваться из масла. Базовое масло и присадки в нем при таком нагреве практически не подвергаются ни тепловому разрушению, ни окислению. В большинстве дегидраторов над маслом пропускают нагретый и осушенный воздух. Водяной пар, выходящий из масла, поступает в сухой воздух. Чтобы увеличить производительность процесса и площадь воздействия, масло разливают тонким слоем по большой поверхности: масло последовательно протекает по целому ряду поверхностей внутри вакуумной камеры либо стекает в камере в виде «дождя с зонтика», и через него проходит осушенный воздух.
Серьезным преимуществом этого процесса является возможность удалять из масла до очень низкого уровня несвязную, эмульгированную и растворенную воду и другие загрязняющие жидкости с низкой температурой кипения: топливо, хладагенты и растворители. Из масел с низким содержанием присадок, таких как турбинные масла, вакуумный дегидратор способен удалить до 80–90% растворенной воды и обеспечить уровень содержания воды в масле всего в несколько миллионных долей (ppm). Особенно полезен этот метод в ситуациях, когда используются большие объемы масла и велик риск попадания в него влаги. Чем больше объем масла и воды и чем ниже требующийся уровень содержания воды в масле, тем более рентабельной будет вакуумная дегидратация.
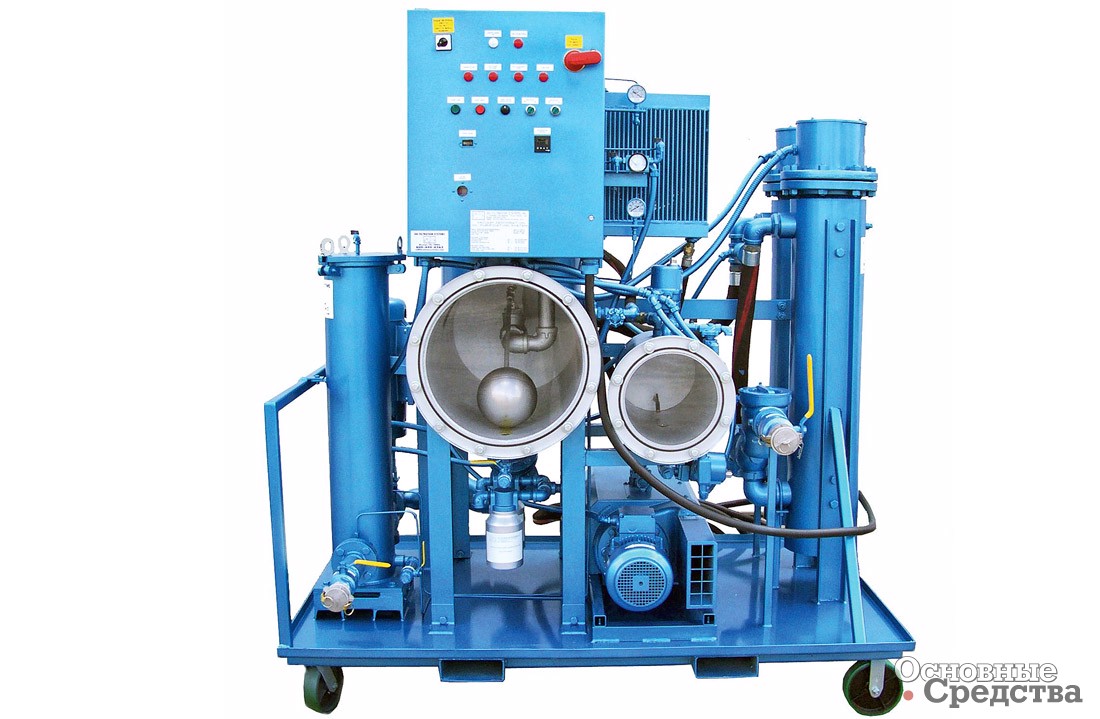
Основным недостатком вакуумных дегидраторов являются их высокая стоимость и сравнительно низкая производительность. Именно из-за высокой стоимости многие компании предпочитают не приобретать в собственность, а брать эти установки в аренду по мере необходимости или просто заменить масло, в которое попала вода. При использовании этой технологии существует определенный риск испарения из масла отдельных присадок.
Воздушная осушка масла. Технология, альтернативная вакуумной дегидратации, – удаление воды путем воздушной осушки масла. При воздушной осушке воздух или азот вводится в поток подогретого масла, перемешивается с маслом и абсорбирует воду и газы, содержащиеся в масле. Затем смесь масла с воздухом расширяется, чтобы из нее вышел воздух/ азот вместе с впитанными, загрязняющими масло веществами. Обычно вода, выделенная таким способом из масла, имеет нормальное качество, ее можно сливать в общую канализацию, не подвергая дополнительной очистке и обработке. Отработавший воздух/ азот фильтруется, чтобы свести к минимуму выбросы паров масла в окружающую среду.
Недостатком способа воздушной осушки, как и у вакуумных дегидраторов, является высокая стоимость. Однако преимуществом этого метода является то, что затраты на эксплуатацию установки все же меньше, чем при использовании обычного вакуумного дегидратора, потому что у воздушного осушителя меньше движущихся деталей. То, что этим методом можно удалять из масла не только несвязную и эмульгированную, но и растворенную воду до уровня менее 100 миллионных долей (ppm) и другие газовые примеси и загрязнения, делает технологию воздушной осушки эффективной альтернативой вакуумной дегидратации.
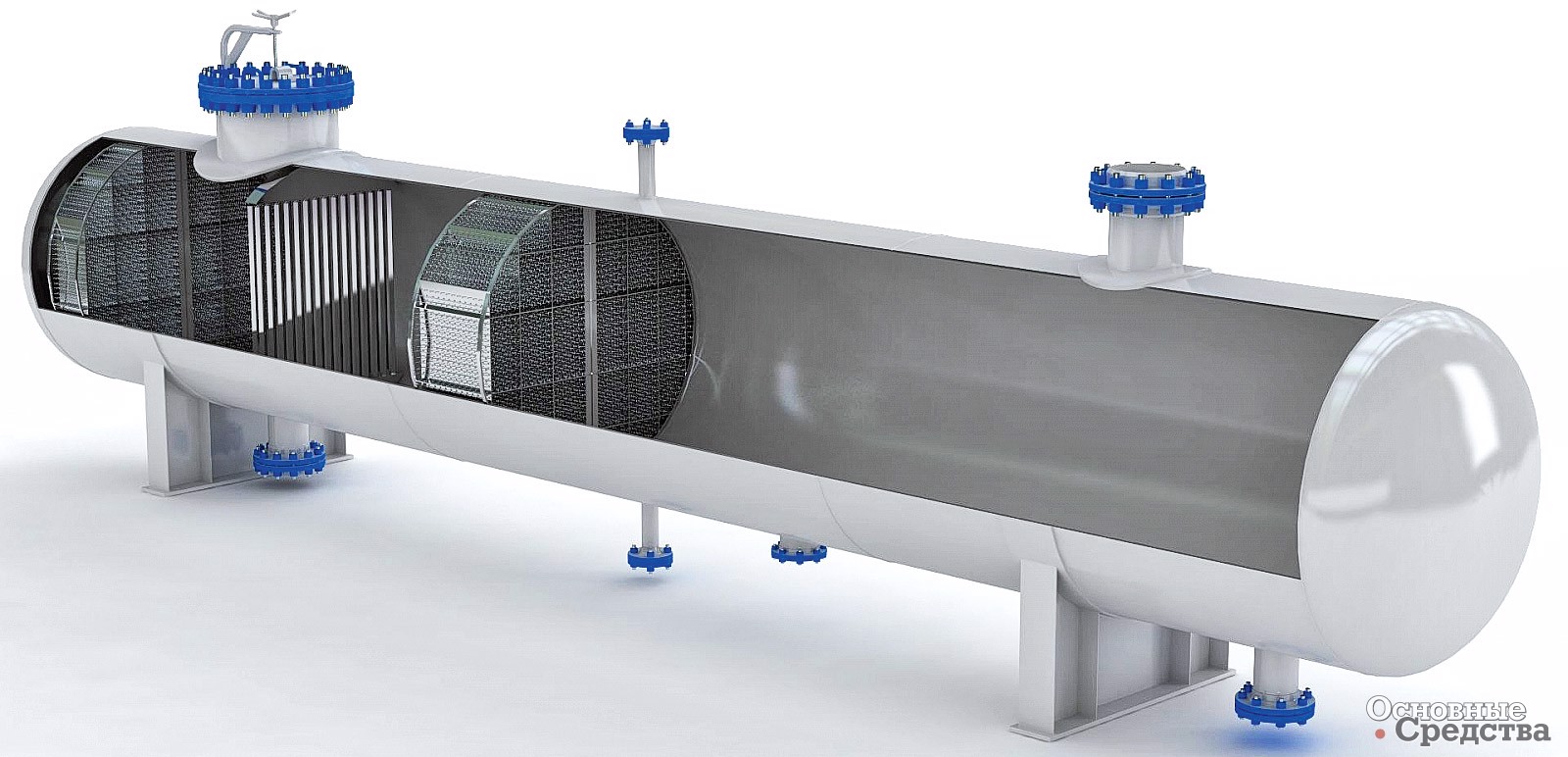
Осушка пространства над жидкостью в резервуаре. Установка для продувки масел воздухом состоит из нескольких резервуаров, насосов для перекачки масла и компрессора для подачи воздуха. Резервуары оборудованы подогревателями и покрыты теплоизоляцией для поддержания необходимой температуры масла. Эти установки работают, откачивая воздух из пространства над жидкостью в резервуаре, осушая его и затем закачивая равный (или увеличенный в некоторых случаях) объем воздуха назад в резервуар, чтобы сохранить в нем прежнее давление. Процесс протекает за счет влагообмена между маслом и воздухом и за счет усиления испарения влаги из масла в газовое пространство резервуара. Воздух затем перекачивается в осушитель для обработки.
Продувку масел воздухом ведут при 80 °С. С понижением температуры способность воздуха поглощать влагу резко падает, и продолжительность процесса обезвоживания значительно увеличивается, а при повышении температуры существенно возрастает вероятность вспенивания масла, что может привести к его выбросу из резервуара.
Продувка воздухом позволяет обезвоживать масла в более короткие сроки, чем при других способах осушки. Большое преимущество этой технологии в том, что установка не взаимодействует с маслом. При использовании этого способа потери масла с удаляемой водой исключаются. С помощью этой технологии можно удалять из масла несвязную, эмульгированную и растворенную воду.

Абсорбция. В конструкцию некоторых масляных фильтрующих элементов включают дополнительный слой, состоящий из влагопоглощающего полимера-суперабсорбента на основе целлюлозы. Этот слой предназначен для того, чтобы поглощать из масла путем абсорбции как эмульгированную, так и несвязную воду. Такие фильтры выглядят как обычные навинчиваемые или патронные (со сменным элементом) фильтры.
Главным недостатком отделения воды от масла методом абсорбции является ограниченная емкость гигроскопичных фильтрующих элементов. Полимеры сильно разбухают, впитывая воду. После заполнения фильтрующего элемента открывается перепускной клапан фильтра, и неочищенное масло идет через байпас. Поэтому прежде чем выбрать данный способ очистки масла от воды, следует рассчитать возможное количество воды, содержащейся в масле, – емкость гигроскопичных фильтрующих элементов должна быть достаточной для удержания подсчитанного объема воды. Такие фильтрующие элементы удобны и лучше всего работают в составе компактных фильтров для систем, где проблемы с попаданием воды в масло минимальны. Например, небольшой картер трансмиссии может оборудоваться системой охлаждения масла с таким фильтром. Кроме того, фильтры с полимерами-суперабсорбентами не способны отфильтровывать и задерживать растворенную воду.
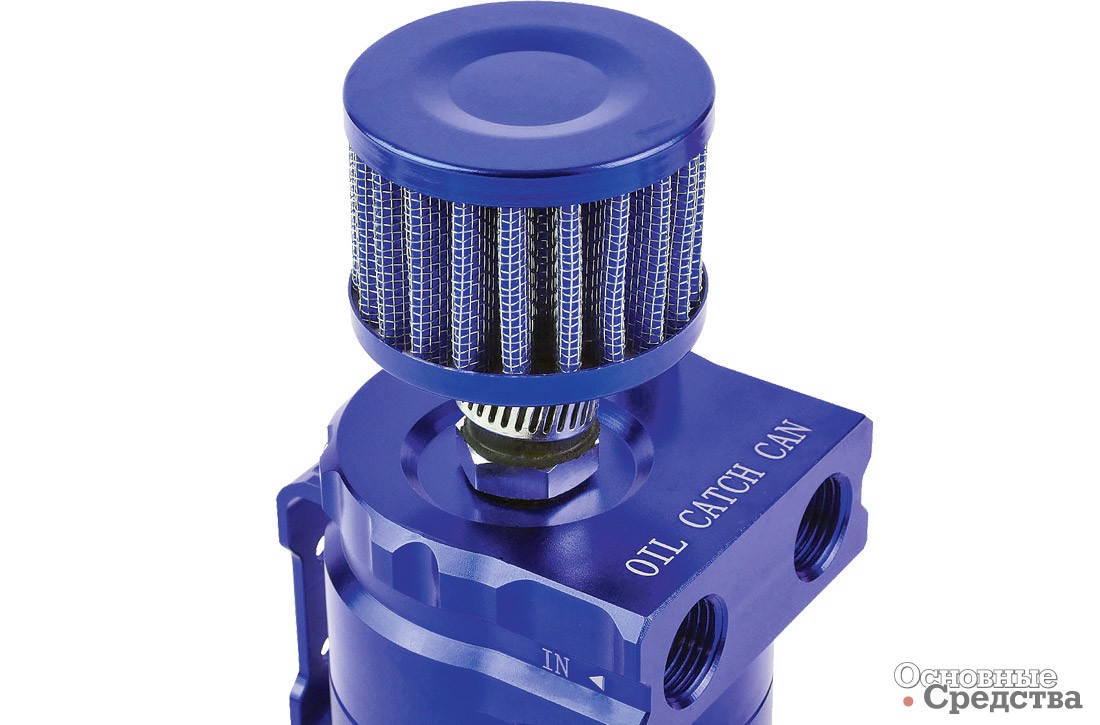
Положительный аспект заключается не только в способности подобных фильтров задерживать еще и твердые частицы, но и в том, что фильтры с влагопоглощающим слоем являются довольно рентабельным средством очистки для масляных систем малого объема, которые требуют удаления даже самого малого количества влаги.
Коагуляция. Слипание и укрупнение коллоидных частиц называется коагуляцией. Добиться протекания данного процесса можно с помощью добавления в масло специальных агентов (электролитов и неэлектролитов), механического воздействия (перемешивание и встряхивание), нагревания или сильного охлаждения, пропускания электрического тока или воздействия лучевой энергии. В каждом из случаев коагуляция возникает за счет ослабления связи загрязняющих частиц с окружающей их дисперсной средой.
Коагуляционные сепараторы помогают микроскопическим каплям воды соединяться вместе, образуя большие и тяжелые скопления, которые легче опускаются на дно и отделяются от масла. Это происходит потому, что при одинаковом объеме воды у крупных капель меньшая поверхность контактирует с маслом, чем в случае, когда капли мелкие и их очень много. Коагуляцию проводят следующим образом. Сначала масло нагревается до температуры 75–90 °С и обрабатывается при перемешивании 10%-ным водным раствором коагулятора на протяжении 20–30 минут. Затем его отстаивают около двух суток и удаляют отстой. Коагуляционные сепараторы более эффективны, когда вязкость масла низка.
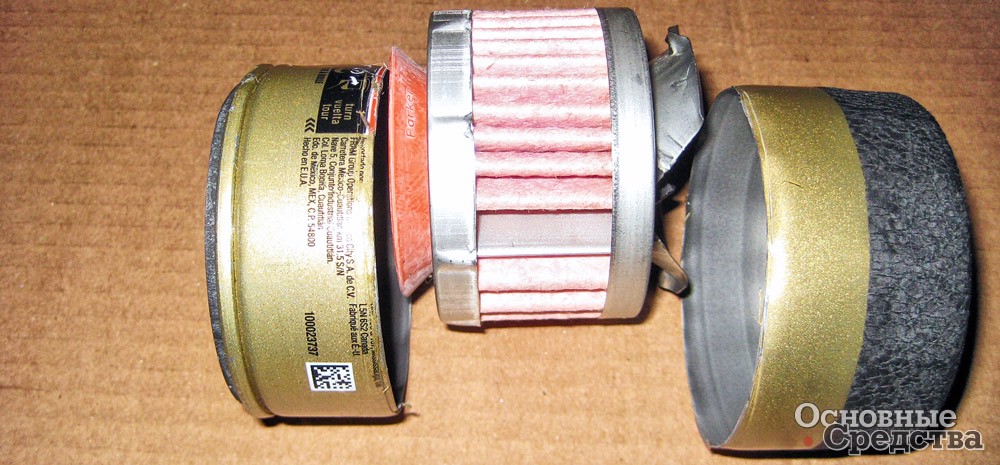
Следует отметить, что коагуляторы позволяют отделять от масла эмульсированную воду только отчасти и не могут отделять растворенную воду.
Здесь приводится сводная таблица, отражающая возможности упомянутых методов очистки масла от воды.
Метод отделения воды от масла | Тип удаляемой воды | Примечания | ||
---|---|---|---|---|
Несвязная | Эмульгированная | Растворенная | ||
Отстаивание | + | +/– | – | Низкая стоимость процесса |
Центрифугирование | + | +/– | – | Высокая стоимость Высокая производительность |
Коагулирование | + | +/– | – | Отстаивание длится двое суток |
Полимеры-суперабсорбенты | + | + | – | Ограниченная емкость Высокая рентабельность |
Вакуум-дистилляция | + | + | + | Высокая стоимость Низкая производительность Высокое качество очистки |
Воздушная осушка | + | + | + | Высокая стоимость Высокое качество очистки |
Осушка воздуха над жидкостью в резервуаре | + | + | + | Высокая скорость процесса |
Присадки
Иногда высказывается мнение, что проблему повышенного содержания воды в масле можно устранить путем добавления в масло специальных присадок. Скажем сразу: это заблуждение.
Во-первых, добавлять в масло присадки самостоятельно не стоит никогда. Рецептуру, содержание присадок в масле подбирают специалисты компании-производителя. Соотношение количества базового масла и присадок в составе продукта должно точно соответствовать рецептуре, чтобы масло имело необходимые рабочие и защитные характеристики.
Если вы не устраните причину попадания воды в масло, от добавки присадок будет мало пользы. Введение присадки может дать кратковременный положительный эффект, но полностью проблему не устранит. Добавляя антиокислительные и антикоррозионные присадки и не решая при этом проблему проникновения воды в масло, вы получите то, что новые присадки будут расходоваться и в конечном счете не принесут пользы.
Итак, необходимо прежде всего устранить причину проникновения воды в масло, а затем, если объем системы смазки невелик, часто оказывается более экономически выгодно просто слить масло и заправить свежее. Если масла в системе много и просто утилизировать его дорого, можно сначала очистить масло от воды одним из описанных выше способов, а затем сделать анализ масла и рассмотреть вопрос о пополнении состава пакета присадок.
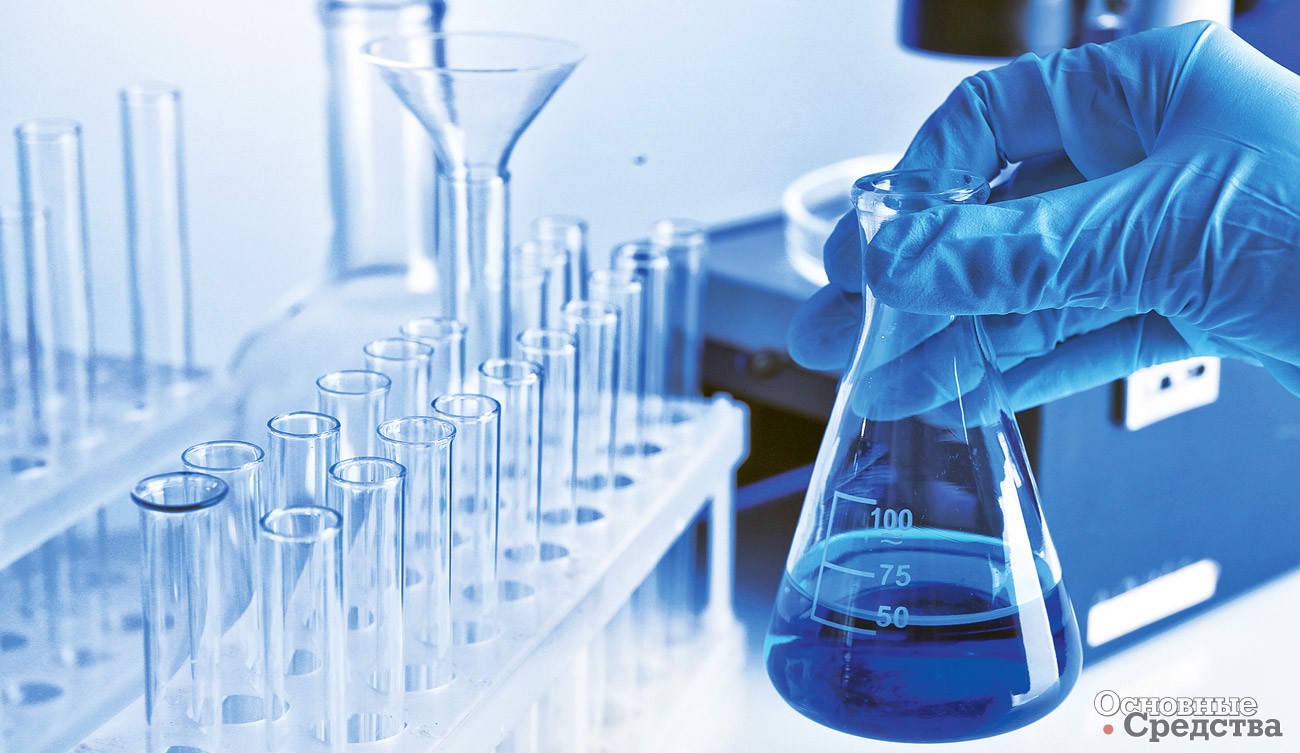
Контроль содержания воды в масле машины – это как контроль содержания холестерина в крови человека: если не контролировать регулярно, нельзя ожидать хороших результатов. Правильная организация этого процесса может потребовать изменения всего сложившегося порядка работы на объекте – от внесения больших изменений в регламент действий работников и до внесения небольших изменений в конструкции машин. Но если учесть, какие неприятности и потери может принести вода в масле, станет ясно, что усилия по изменению порядков на производстве того стоят.
Удаление масла из системы
Во время работы холодильной установки из компрессоров масло попадает в систему. Пленка масла ухудшает теплопередачу в теплообменных аппаратах. При замасливании конденсатора повышаются температуры и давления конденсации, а испарителя — понижаются температуры кипения. При этом холодопроизводительность установки уменьшается, а удельный расход электроэнергии увеличивается. Масло отделяется от аммиака перед конденсатором.
Наиболее эффективным способом отделения масла в Холодильных установках с поршневыми компрессорами является пропуск пара через слой жидкого аммиака в барботажном маслоотделителе.
В холодильных установках с компрессорами,
имеющими циркуляционную систему
смазки (ротационные, винтовые), когда
температура пара после сжатия не
достигает высоких значений, применяют
циклонные маслоотделители.
При эксплуатации холодильных установок необходимо периодически выпускать масло из конденсаторов, ресиверов, испарителей, отделителей жидкости и других аппаратов.
При интенсивной работе холодильной установки периодичность выпуска масла следующая;
из маслоотделителей (через маслосборник) каждые 5 дней;
из промежуточных сосудов через 6 дней, из конденсаторов, ресиверов, отделителей жидкости один раз в месяц;
Рис. . Схема включения маслосборника.
из охлаждающих приборов камер при каждом снятии снеговой шубы горячими парами холодильного агента.Выпуск масла осуществляют через специальные маслосборники (рис. ).
Для выпуска масла из аппаратов открывают вентиль 2 и понижают давление в маслосборнике МС до давления всасывания. Закрыв вентиль 2, открывают вентиль 1 и перепускают масло из аппаратов в маслосборник. Для отсасывания паров аммиака из масла постепенно открывают вентиль 2. После отсасывания в течение 20 мин вентиль 2 закрывают и выпускают масло в ведро через шланг, присоединенный к вентилю 3. При этом соблюдают меры безопасности, машинист должен быть в резиновых перчатках и противогазе, включают вытяжную вентиляцию. Избыточное давление в маслосборнике не более 0,05 МПа (0,5 кгс/см2).
Выпущенное масло собирают в специальную емкость и подвергают регенерации
(рис. ).
Рис. . Схема установки для регенерации масла;
1 — термометр; 2—пробка; 3 — нагревательный змеевик; 4—корпус маслоотстойника; 5 — вентиль для выпуска загрязнений; 6 — насос; 7 — электродвигатель; 8 — вентиль; 3 — манометр; 10 — фильтр-пресс; II — приемная емкость; 12 — сливной желоб.
Выпуск воздуха из системы
В систему холодильной установки при эксплуатации воздух проникает при ремонте аппаратов и компрессоров, а также при заправке системы холодильным агентом, маслом, при давлении всасывания ниже атмосферного через неплотности в трубопроводах и сальниках компрессора. Независимо от того, в какой части холодильной установки воздух попал в систему, он скапливается в конденсаторе и линейном ресивере, где образуется гидравлический затвор, препятствующий прорыву воздуха в испарительную систему.
Основные признаки наличия воздуха в системе — повышенное давление в конденсаторе и вибрация стрелки манометра, установленного на конденсаторе и компрессоре.
Повышение давления в конденсаторе приводит к увеличению температуры нагнетания в компрессоре, уносу масла и к аварийной ситуации. Если парциальное давление воздуха равно 0,1 МПа, то перерасход энергии составит 6%.
Во время эксплуатации холодильной установки необходимо своевременно выпускать воздух из системы.
При наличии воздуха в конденсаторе в количестве до 20% коэффициент теплоотдачи уменьшается в 4—5 раз. Таким образом, наличие воздуха в системе приводит к повышению температуры и давления конденсации вследствие ухудшения теплоотдачи.
Рис. . Зависимость массовой концентрации воздуха в смеси с аммиаком от давления смеси Рем и ее температуры tсм.
На установках, не имеющих воздухоотделителей, воздух выпускают, когда компрессоры не работают. В конденсатор сначала подают охлаждающую воду, а затем выпускают воздух в сосуд с водой через шланг, присоединенный к верхней точке конденсатора или линейного ресивера. Этот способ выпуска воздуха приводит к значительным потерям холодильного агента.
Рис. . Зависимость массовой концентрации воздуха в смеси с R12 от давления смеси рСм и ее температуры tсм.
Зависимость суммарного давления воздушно-аммиачной смеси от массовой концентрации показана на рис. , а зависимость массовой концентрации воздуха в смеси с R12 от давления смеси и ее температур — на рис. . Как видно из графиков, для уменьшения потерь холодильного агента при выпуске парогазовой смеси пары хладона необходимо охлаждать до более низких температур, чем аммиак.
Для уменьшения потерь холодильного агента установки оборудуют воздухоотделителями. Наиболее простыми по конструкции являются двухтрубные воздухоотделители (см. рис. ,а), которыми комплектуются линейные ресиверы.
Рис. . Схема включения АВ-4 со сливом жидкого аммиака в коллектор регулирующей станции (а) или в линейный ресивер (б).
Наиболее полное охлаждение смеси происходит в воздухоотделителях АВ-2 и АВ-4, где автоматически выпускается воздух по мере его поступления в систему.
Вариант подключения воздухоотделителя со сливом жидкого аммиака в линейный ресивер показан на рис. . Для создания свободного стока конденсата аммиака в линейный ресивер воздухоотделители АВ-2 и АВ-4 размещают над ним на высоте 1—2 м.
Удаление воздуха и воды из гидравлической жидкости
Наличие воздуха в жидкости может быть причиной множества проблем в гидравлической или смазочной системе,таких как : высокий уровень шума, плохая управляемость исполнительных устройств из-за высокого содержания воздуха и жидкости, повреждения…
Удаление воздуха из гидравлической жидкости
Наличие воздуха в жидкости может быть причиной множества проблем в гидравлической или смазочной системе,таких как : высокий уровень шума, плохая управляемость исполнительных устройств из-за высокого содержания воздуха и жидкости, повреждения вследствие кавитации, деградация жидкости.
Устройства для удаления пузырьков из гидравлической жидкости используются для механического удаления воздуха, но решая эту задачу они так же помогают уменьшить размер гидравлического бака и уменьшить общую стоимость системы (см. «Основные функции гидравлического бака»). В этой статье рассказывается о принципах работы и обслуживания устройств, которые могут быть установлены в гидравлическую систему для физического удаления пузырьков воздуха в ходе эксплуатации системы.
Рисунок 1. Процесс кавитации
Кавитация возникает, когда давление, действующее на жидкость ниже давления насыщения растворенного в жидкости газа. В тот момент, когда пузырек, содержащийся в жидкости циркулирующей в системе попадает в область высокого давления (обычно гидравлический насос), он разрушается как это показано на рисунке выше. В зависимости от давления в гидравлическом насосе этот процесс может наносить серьезные повреждения и быть причиной высокочастотной вибрации, шума, термической деградации масла.
В гидравлическом баке пузырьки газа могут находиться в основном на поверхности в виде пены, но так же могут быть и в самой гидравлической жидкости как на рисунке ниже.
Рисунок 2. Воздух в гидравлической жидкости
Если пузырьки присутствуют в жидкости и гидравлическом баке, они могут быть засосаны насосом, где их объем сначала увеличится из-за снижения давления на линии всасывания, а затем снова уменьшится, когда они попадут в область высокого давления. Такое сжатие почти адиабатическое (пузырек нагревается, но не сильно повышает температуру окружающей жидкости) в результате чего высокие температуры локализуются на поверхности раздела газ-жидкость, что приводит к термическому повреждению масла и образованию нагара.
С точки зрения воздействия сложно провести различие между этими двумя процессами, поэтому в рамках данной статьи будем рассматривать их оба как единый процесс кавитации.
Существую различные причины попадания воздуха в систему, такие как :
- Сопротивление всасыванию.
- Падение давления при проходе жидкости через отверстия.
- Падение давления при проходе жидкости через трубы и шланги.
- Турбулентность от закрытия или открытия клапана.
- Ударные волны, вызванные резким закрытием клапанов или резким прекращением работы насоса.
- Падение давления из-за резкого открытия клапана.
- Внешние усилия, воздействующее на шток гидроцилиндра.
- Недостаточный объем жидкости для работы гидравлического насоса.
В системах смазки при подаче жидкости на шестерни или подшипники при прохождении через них пузырьки могут создавать эффект вспенивания. Обычно физические и химические эффекты, возникающие в результате такие процессов нежелательны, например увеличение шума системы, известное как эффект «водяного молота» как правило, сопровождается кавитацией.
Кроме того, кавитация может привести к усилению окисления масла. Если в пузырьке газа содержится воспламеняющееся вещество, оно может загореться из-за повышения температуры, которым сопровождается сжатие. Этот процесс продолжается наносекунды, но локальная температура может достигать 1100 C и выше. Этот процесс так же называют «микро-дизель» и он может приводить к окислению масла, а резкие перепады давления, сопровождающие его, приводят к квитанционной эрозии гидравлического насоса и других компонент. Помимо этих хорошо известных процессов, кавитация может привести к образованию промежуточных химических веществ, которые способны повлиять на вторичный окислительный и восстановительные процессы.
Другие проблемы гидравлических систем вызванные наличием пузырьков в гидравлической жидкости :
- Повышение температуры масла.
- Ухудшение качества масла.
- Ухудшение смазывающих свойств (вследствие либо потери вязкости, либо образования нагара).
- Пониженная теплопроводность.
- Кавитация и эрозия.
- Сильный шум.
- Уменьшение коэффициента упругости (из-за наличия пузырьков в жидкости).
- Уменьшение производительности насоса.
- Низкие диэлектрические свойства.
Недавно компания «Opus System, Inc» разработала устройство для механического удаления пузырьков из гидравлической жидкости, которое получило оригинальное название «Bubble Eliminator», что с английского переводится как отделитель пузырьков
Рисунок 3. Принцип работы Bubble Eliminator
Как это работает ?
Устройство состоит из конусовидной трубки, имеющей круглое поперечное сечение, которая находится в цилиндрической камере самого устройства. Жидкость, содержащая пузырьки, попадает в устройство под прямым углом из входной трубки и создает закрученный поток, который циркулирует через проточный канал. Закрученный поток, ускорение которого по радиусу уменьшается, снижает давление жидкости вдоль центральной оси согласно закону Бернулли. К концу конусовидной трубки вихревой поток замедляется, давление восстанавливается, и жидкость движется на выход.
Значение центробежной силы зависит от расстояния, поэтому в вихревом потоке пузырьки движутся по направлению к центральной оси за счет разницы значений центробежной силы. Мелкие пузырьки создают воздушный столб, из закрученного потока, вращающегося в центре, где давление самое низкое. Затем пузырьки удаляются из устройства через клапан.
Рисунок 4. Удаление воздушных пузырьков.
А) Аэрированная жидкость В) Де-аэрированная жидкость.
Использование
Использование устройства на линии всасывания после гидравлического насоса, теоретически может удалить пузырьки из жидкости. Затем они поступают на устройство и удаляются из системы. Когда содержание растворенного в жидкости газа уменьшается, способность жидкости растворять газ увеличивается, поэтому она поглощает больше пузырьков, которые потом удаляются из нее посредством Bubble Eliminator.
Bubble Eliminator так же может быть подключен на линии слива, было продемонстрировано ,что он эффективно удалять пузырьки из гидравлических жидкостей, предотвращая кавитацию и поломки оборудования.
Выводы
- Использование оборудования по удалению воздуха из гидравлической жидкости позволяет уменьшить объем гидравлического бака, и помимо этого дает следующий преимущества :
- Уменьшение физических размеров и цены.
- Уменьшает деградацию жидкости, тем самым продлевая ее срок использования.
- Предотвращение кавитации и шума в насосе.
- Уменьшение сжимаемости жидкости и улучшение динамических характеристик.
- Упрощенная конструкция гидравлического бака без экранирующей перегородки.
Сжатый воздух, очистка от масла
Масловодоотделители служат для очистки сжатого воздуха от масла и воды (рис, 40). Они представляют собой сосуды цилиндрической формы 1 с выпуклым днищем и плоской крышкой 3, прикрепленной болтами к корпусу. Внутренняя полость цилиндра заполнена гранулированным коксом 9, проложенным между слоями войлока 10. На крышке масловодоотделителя расположен редуктор с манометром 5. Воздух от компрессора поступает в нижнюю часть масловодоотделителя через трубу 2, а затем проходит через фильтр, очищается от воды п масла и через кран 4 поступает в шланги, ведущие к распылителю. [c.177]Фильтры с зернистым слоем фильтрующего материала используют для тонкой очистки газов, например для очистки сжатого воздуха от масла, улавливания сажи, очистки от пыли синтез-газов. [c.236]
Сжатый воздух, выходящий из компрессорной установки, необходимо очищать от содержащихся в нем паров масла и воды с целью предотвращения уноса их в воздухосборник и трубопроводы. В определенных условиях масло и вода могут быть причиной аварии и даже взрыва. Поэтому с целью очистки сжатого воздуха от масла и воды в поршневых и ротационных компрессорных установках применяются масловодоотделители. [c.71]
Чтобы предотвратить образование отложений внутри компрессорных установок, воздух перед поступлением в компрессор очищается от пыли, влаги и вредных примесей, вызывающих коррозию и опасность взрыва. Забор воздуха производится из чистой зоны на высоте не менее 2—3 м от земли. Для очистки сжатого воздуха от масла и сконденсировавшейся влаги на напорных трубопроводах устанавливают влагомаслоотделители. [c.137]
Для очистки и осушки сжатого воздуха от масла и воды наиболее широкое применение получили масловодоотделители и осушительные баллоны. [c.72]
Примечания 1. В компрессорных станциях, где установлены компрессоры без смазки полостей сжатия, или в установках, где предусмотрена специальная очистка сжатого воздуха от масла в капельном виде, а также если температура воздуха в воздухосборнике и воздухопроводах не превышает 50 °С, осмотр и очистка воздухосборников и воздухопроводов должны производиться не реже одного раза в год. [c.75]
Щелочная очистка масляных дистиллятов проводится при температурах 140—160 °С и при давлении 0,6—1,0 МПа во избежание испарения воды. Технологическая схема щелочной очистки масел приведена на рис. ХП1-6. Масляный дистиллят насосом 1 прокачивается через трубное пространство теплообменника 2, змеевики трубчатой печи 3 и с температурой 150—170 С подается в диафрагмовый смеситель 4. Туда же закачивается 1,2—2,5 %-ный раствор гидроксида натрия. Из смесителя реакционная смесь поступает в отстойник 5. Температура в отстойнике 130—140 °С, давление 0,6—1,0 МПа, длительность отстоя 3,5—4 ч. Щелочные отходы, выходящие с низа отстойника, охлаждаются в холодильнике 6 погружного типа до 60 °С и направляются в сборники для отделения нафтеновых кислот. Очищенный масляный дистиллят с верха отстойника 5 поступает в смеситель 7 на промывку водой. Температура подаваемой в смеситель химически очищенной воды 60—65 °С, Отделение промывной воды от дистиллята осуществляется в отстойнике 8. Выходящие с низа отстойника промывные воды охлаждаются в холодильнике 9 погружного типа и направляются в сборник для отделения нафтеновых кислот. Очищенный и промытый продукт с верха отстойника 8 проходит теплообменник 2, где, отдавая свое тепло сырью, охлаждается с 90 до 70 °С, и поступает в сушильную колонну 10 для удаления мельчайших капелек воды за счет продувки его горячим сжатым воздухом. Готовое масло с низа сушильной колонны откачивается в резервуары. [c.117]
Воздух, сжатый поршневыми и ротационными компрессорами некоторых типов, содержит капельки масла. Если такой воздух направить в контактный аппарат, масло окислится и будет загрязнять получаемые продукты. Этим объясняется необходимость очистки сжатого воздуха по выходе из компрессора. [c.399]
Для очистки сжатого воздуха от масла, воды и твердых частиц установка снабжена сдвоенным масловодоотделителем, на котором установлены манометр и запорные вентили для регулирования напора и количества сжатого воздуха, подаваемого в ванну взвешенного слоя. [c.182]
Комплекты оборудования для очистки сжатого воздуха от масла и влаги [c.419]
Кроме рассмотренных маслоотделителей и масловодоотделителей для очистки сжатого воздуха от масла и воды, применяют следующие масловодоотделители. [c.28]
При необходимости очистки сжатого воздуха от масла рекомендуется применять масляные фильтры по схеме фиг. 14-11. [c.440]
В основном эти меры сводятся к недопущению загрязнения воздуха, засасываемого компрессорами, ацетиленом и другими углеводородами и к очистке сжатого воздуха от масла и продуктов его разложения до поступления воздуха в блок разделения. [c.223]
Хорошие результаты по очистке сжатого воздуха от масла дает непрерывное автоматическое удаление эмульсии из маслоотделителей На рнс. Х1У-12 показан аппарат автоматической продувки, а на рис. XIV- [c.225]
Сжатый воздух после компримирования содержит не только масло, но и влагу, пыль, продукты коррозии. Поэтому он нуждается в очистке и осушке. Для отделения водяных и масляных капель используются специальные аппараты — водомаслоотделители. Существуют водомаслоотделители инерционного, поверхностного и инерционно-контактного типа. Инерционное отделение капель происходит вследствие поворотов и резкого изменения скорости воздушного потока. В аппаратах поверхностного типа воздушный поток пропускают через слой насадки с развитой поверхностью (гофрированные сетки, кольца Рашига и т. п.), в аппаратах инерционно-контактного тина воздушный поток проходит между зигзагообразными листами или жалюзями. [c.254]
Повышению стабильности масла может способствовать окисление его нестабильных компонентов (перевод в стабильные соединения). Достигается это путем продувки воздуха или чистого кислорода через масло при умеренных температурах. Такая обработка также способствует повышению вязкости маловязких масел. Полученный продукт фильтруют для удаления осаждающихся полимеров. Так, для улучшения качества масла лиственницы (компонент СОТС) его окисление ведут при 120—130°С (постепенный нагрев), барботаже сжатого воздуха 15—18 мVч на тонну масла