Лужение и пайка кузова автомобиля

Приветствую Вас на блоге kuzov.info!
В этой статье мы рассмотрим как осуществляется лужение и пайка кузова автомобиля.
Лужение и пайка кузова автомобиля применялись при изготовлении и ремонте автомобилей с середины 1930‑х годов. Свинцовый припой использовался при массовом производстве автомобилей для нанесения на сварочные соединения внахлёст крыши и задних крыльев. Нанесение припоя на кузов долгие годы, до появления автомобильной шпаклёвки, оставалось традиционным методом ремонта повреждённого кузова автомобиля (см. статью об истории изобретения и развития шпаклёвки).
Содержание:
Процесс состоит в нанесении специального припоя на панели кузова, чтобы заполнить неровности, герметизировать и замаскировать сварочные соединения, а также запаять отверстия. В то время, как в современном кузовном ремонте чаще всего применяется шпаклёвка, при реставрации классических автомобилей по-прежнему используют припой. На самом деле, и лужение и шпаклёвка имеют свои преимущества и недостатки. Главными недостатками применения припоя для ремонта кузова являются сложность его нанесения и нагрев кузова. Слишком сложного в этом процессе ничего нет, но требуется соблюдать некоторые правила и приобрести навык. При правильном воздействии горелки нагрев получается достаточно щадящим. Даже краска с обратной стороны может остаться целой. Шпаклёвка в этом смысле выигрывает, так как наносится на поверхность легче припоя. По характеристикам припой во многом превосходит шпаклёвку. Его преимущества мы рассмотрим в этой статье ниже.
Припой размягчается нагревом и наносится на поверхность, подготовленную лужением. После остывания образуется прочная связь припоя с поверхностью металла.
Нанесение припоя на кузов может потребоваться там, где сложно или невозможно использовать другие методы ремонта. Припой удобно применять, когда металл слишком толстый для рихтовки и отсутствует доступ с обратной стороны панели. Припой можно использовать на местах, где возможно небольшое движение металла при эксплуатации автомобиля и шпаклёвка может треснуть (сварочное соединение). Припой хорошо герметизирует сварочный шов и гарантирует его коррозионную устойчивость. Также, при использовании кузовного припоя, толщина слоя не так критична, как при применении шпаклёвки. Припой хорошо подойдёт для мест кузова, где нужно сформировать кант.
Преимущества лужения и пайки кузова
- Припой держится на поверхности лучше шпаклёвки. Прочность на разрыв (сила, требуемая, чтобы отделить припой от металла, на который он нанесён) составляет 423 бара. Это очень высокий показатель.
- Даже толстый слой припоя не даёт усадки, в отличие от шпаклёвки.
- Припой имеет лучшую эластичность и прочность, чем автомобильные шпаклёвки. Свинец хорошо гнётся вместе с металлом, на который он нанесён, поэтому не трескается.
- Припой не потрескается и не отслоиться при ударе, как это бывает со шпаклёвкой.
- Припой является водонепроницаемым. Шпаклёвку же нельзя назвать полностью водонепроницаемой.
- Припой может выдерживать высокие температуры, поэтому может применяться при ремонте и последующем нанесении порошковой краски.
- Ещё одним большим преимуществом припоя над шпаклёвкой является то, что не стоит беспокоиться о времени его затвердевания. Можно добавлять дополнительный припой прямо на уже нанесённый слой. Нужно только разогреть поверхность и новый припой и добавить его. Не нужно полностью расплавлять уже нанесённый слой.
Виды припоев для ремонта кузова
- Существуют разные типы припоев. Для ремонта кузова чаще применяются мягкие (легкоплавкие) припои. Они продаются в виде стержней, длинной 45 см, разной толщины. В целом, они классифицируются как припои с содержанием свинца и без содержания свинца (lead free). Первый тип припоя применялся много лет из-за его лёгкости использования. Однако он был запрещён в некоторых странах для применения в массовом производстве, по причине вреда здоровью и окружающей среде. Однако, свинцовый припой, по-прежнему используется частными лицами и его можно встретить в продаже. Многие мастера предпочитают использовать именно свинцовый припой.
- На припое указывается соотношение его компонентов (олова, свинца). Традиционный припой для кузова состоит из 30% олова и 70% свинца. Может содержаться дополнительный компонент, к примеру, 74% свинца, 25% олова и 1% сурьмы. Свинец опасен для здоровья. Чтобы его применять, требуются средства защиты, и нужно учитывать меры безопасности. Однако его легче использовать. Он дольше остаётся мягким после нагрева (в диапазоне от 180 до 260 градусов по Цельсию). Это облегчает его нанесение и разравнивание. Этот припой легко наносится на вертикальные и горизонтальные поверхности. После затвердевания свинцового припоя, его не рекомендуется обрабатывать шлифовальной машинкой, так как образуется очень токсичная пыль. Так, его обычно обрабатывают специальным кузовным напильником, а на завершающей стадии бруском с крупнозернистой шлифовальной бумагой вручную. Если всё же применяете шлифовальную машинку, то нужно использовать только крупный абразив, чтобы не было взвеси из мелкой пыли. Остатки свинца после шлифования нужно сразу утилизировать.

- Припой может иметь разное соотношение свинца и олова (70/30, 60/40 или 50/50). Припой с более низким содержанием свинца также используется при ремонте кузова, но имеет низкий диапазон пластичности (от 183ºC до 188ºC), поэтому его сложнее использовать. Припои с таким соотношением обычно применяют на горизонтальных поверхностях, так как они быстро становятся жидкими и могут стекать. Прилипание у всех свинцовых припоев примерно одинаковое и зависит от правильности подготовки поверхности.
- Как альтернатива припою со свинцом был разработан более безопасный припой без содержания свинца. Во всех припоях без содержания свинца, олово является главным компонентом. Другим компонентом может быть серебро, медь, индий или висмут. Большинство припоев без свинца имеют либо более высокую, либо более низкую точку плавления, чем у свинцового припоя. Для ремонта кузова наиболее распространён припой без свинца, состоящий из олова и серебра (94% олова и 6% серебра или 96% олова и 4% серебра). Он имеет более высокую стоимость. Припой без свинца примерно равен по характеристикам традиционному припою со свинцом с соотношением 50/50 (свинец/олово). Такой припой имеет более высокую точку плавления (221°C). После нагрева, он остаётся в мягком состоянии менее продолжительное время, чем свинцовый припой, что усложняет его выравнивание. При застывании получается более твёрдым и хрупким. Его сложнее обрабатывать напильником. Преимущество в том, что его можно обрабатывать шлифовальной машинкой, так как он не образует токсичной пыли. Хотя, не нужно забывать про респиратор. Дополнительным преимуществом припоя без свинца является более высокая прочность на разрыв.
- Припой, применяемый в электронике, обычно состоит из 60% олова и 40% свинца. Он может содержать флюс в центре. Флюс с канифолью, часто используемый с таким припоем, не способствует адгезии к стали, а флюс с кислотой может действовать хорошо. Такой припой лучше применять только для пайки маленьких отверстий, так как его диапазон пластичности очень маленький.
- Для работы с кузовами из алюминия используется другой тип припоя (с содержанием олова и цинка).
Что такое флюс? Какой флюс использовать для лужения кузова?
Цель флюса – облегчать процесс пайки и обеспечить прочность соединения припоя с металлом кузова. Одной из преград для достижения успешной пайки является нечистота поверхности (загрязнения и окисление). Загрязнения могут быть удалены механической чисткой, но окисление увеличивается при увеличении температуры, что ухудшает прикрепление припоя к ремонтной поверхности. Металл имеет тонкий слой оксидов или сульфидов, каким бы чистым он не выглядел. Флюс предназначен для того, чтобы убрать этот слой и должен предотвратить формирование нового оксидного слоя во время нанесения припоя. Флюс не только предотвращают окисление, но и обеспечивают химическую чистку и выполняет смачивающую функцию, сокращая поверхностное натяжение расплавленного припоя, помогая ему лучше растекаться по поверхности. Таким образом, припой не прилипнет на не подготовленную металлическую поверхность, он будет собираться в шарики. На подготовленной поверхности припой нормально растекается и прилипает.

Для лужения кузова применяется флюсовая паста. Она представляет собой некое подобие первичного грунта. В её состав входит кислота (хлорид цинка или соляная кислота) и припой в виде порошка. Кислота химически очищает поверхность и удаляет окисление, переводя его в растворимую соль, а порошок одновременно въедается в металл, оставляя очень тонкий слой (олова или олова со свинцом), который улучшает адгезию припоя при нанесении на ремонтную область.
После нанесения, пасту нужно нагреть и стереть остатки тряпкой.
Флюсовая паста активирована кислотой (хлорид цинка или соляная кислота), и её остатки требуется удалить после завершения нанесения припоя. Если флюс основан на соляной кислоте, то нейтрализовать её можно водой с содой, а потом обмыть чистой водой. Если флюс содержит хлорид цинка, то для нейтрализации потребуется ацетон. Также, можно использовать средство дихромат натрия.
Частицы от флюсовой пасты могут оставаться в порах и мелких углублениях сварочного шва, что может стать причиной коррозии. Поэтому, перед лужением и нанесением припоя, нужно, чтобы отверстия и углубления были заварены.
Какие инструменты и материалы нужны для лужения и пайки кузова?
- Существуют специальные наборы, в которые входит сам припой, флюсовая паста, инструменты для выравнивания нанесённого припоя и инструкция. Также, все принадлежности можно купить по отдельности.

- Необходим припой и паста для лужения (tinning paste) с кистью для более лёгкого нанесения.
- Также нужна чистая тряпка (лучше всего подходит хлопковая), для стирания остатков пасты после нагрева.
- Для нагрева необходима сварочная газовая горелка, пропановая (бутановая) горелка или фен с регулировкой температуры и потока воздуха. При использовании сварочной газовой горелки, пламя должно быть настроено на минимальную температуру, при которой будет плавиться флюс и разогреваться металл кузова.
- Припой разравнивается специальными блоками из твёрдого дерева. Применяется специальная смазка (твёрдый животный жир), тонкий слой масла или пчелиный воск, наносимый на лопатку или блок, чтобы они не липли к припою. Так припой, разглаженный блоками, получается более ровным. Можно изготовить блок нужной формы самостоятельно.
- Нужно использовать респиратор с системой HEPA (high efficiency particulate air) с фильтром высокой эффективности удержания частиц, также известный как фильтр N100. Можно также рядом установить вентилятор, который будет сдувать вредные испарения в сторону от мастера. Тогда вред испарений снижается и можно обойтись без респиратора. При использовании припоя со свинцом необходимо использовать перчатки. Нужно избегать контакта припоя и флюса с кожей.
- Для обработки затвердевшего припоя понадобится кузовной напильник или шлифовальный блок с крупнозернистой шлифовальной бумагой.
- Нужно, чтобы все материалы и инструменты были в зоне досягаемости, чтобы не терять время, во время лужения.
Лужение и пайка кузова автомобиля
Свинец не желательно применять на тонком металле или быть осторожным, чтобы не перегреть тонкий листовой металл, тем самым, ослабив его. Тепловой деформации могут подвергаться особенно плоские панели, так как имеют меньшую жёсткость, в сравнении с выпуклыми формами и панелями, имеющими рёбра жёсткости.
Процесс лужения и пайки кузова (нанесение припоя):
- Сначала поверхность должна быть очищена от краски и возможной ржавчины. Используйте нейлоновый зачистной круг, который не удаляет металл при чистке. Зачищайте поверхность минимум на 5 см с запасом по краям. Протрите поверхность обезжиривателем или ацетоном.
- Нанесите кистью флюсовую пасту для припоя на ремонтируемую область с запасом по краям.
- Далее поверхность с нанесённой пастой разогревается пропановой горелкой (или другим источником пламени или горячего воздуха) до момента, когда приобретёт серебристо-коричневый пенистый вид. Когда это произойдёт, возьмите чистую хлопковую тряпку и вытрите излишки флюса. Чистой хлопковой тряпкой нужно разровнять слой и стереть остатки флюса. Должно получиться ярко-серебристое покрытие. Важно не перегревать пасту для лужения, иначе паста будет сожжена и её придётся счищать и наносить заново. Пламенем нужно водить, не задерживаясь на одном месте. Нужно использовать только кончик пламени.
- Можно применить другой метод лужения металла кузова. Нужно нагреть панель (не докрасна). После разогрева поверхности используйте медную мочалку для посуды, чтобы нанести флюсовую пасту. Удерживая плоскогубцами или зажимом для сварки, её нужно намокнуть во флюсовую пасту и начать протирать нагретую поверхность, продолжая поддерживать нагрев панели пламенем. После лужения, остатки от флюса нужно тщательно смыть с поверхности раствором горячей воды с содой.
- Нужно предварительно подготовить деревянный блок для разравнивания нанесённого припоя. Если он не новый и уже использовался, то нужно убрать остатки состава, предотвращающим прилипание к припою, который был на него нанесён в прошлый раз. Для этого можно отшлифовать его крупнозернистой шлифовальной бумагой. Подошва блока должна быть чистой и ровной. Далее его нужно смазать жиром (или пчелиным воском), чтобы он не прилипал к припою, а легко скользил по его поверхности. В процессе работы, может понадобиться снова нанести смазку.

- Технология нанесения припоя может быть разной. Можно нагреть панель и припой и нанести его на поверхность горками в нескольких местах. Потом снова нагреть эти горки и разровнять деревянным блоком. Есть другой способ. Нужно разогреть поверхность кузова, поставить стержень припоя под углом 45 градусов к поверхности и разогреть его кончик до момента, когда он начнёт плавиться. Далее нужно наплавлять припой полосками, двигая припой вдоль поверхности.
- После нанесения полосок нужно снова разогреть припой и начать разравнивать деревянным блоком, поддерживая нужную температуру.

- При обработке большой площади, можно удерживать в руке несколько стержней припоя. Как и в случае со шпаклёвкой, наносить припой нужно немного дальше повреждённой области и выше общего уровня всей панели, с запасом. Лучше потом срезать напильником излишек припоя, чем добавлять его после застывания. При работе на вертикальных поверхностях правильный нагрев припоя наиболее важен. Не страшно, если припой при разогреве и нанесении будет немного капать. Нужно просто немного увеличить расстояние пламени от поверхности.
- Следующим шагом, после остывания припоя, нужно очистить поверхность раствором соды в воде, чтобы нейтрализовать остатки флюса, а также стереть остатки масла от выравнивающей лопатки или блока. Этот этап особенно актуален, если остатки флюса стирались простой тряпкой (см. пункт №3). Смешайте пищевую соду (2 или 3 столовые ложки) на 1 литр воды и нанесите губкой, тряпкой или скотч-брайтом (чтобы оттереть въевшийся от нагрева флюс), тщательно вымойте поверхность этим средством, потом высушите феном или сжатым воздухом. После этого обработайте наждачной бумагой на сухую и покройте кислотным грунтом. После этого нужно обмыть поверхность чистой водой. Далее можно продуть поверхность, протереть обезжиривателем или ацетоном.
- Далее используйте специальный кузовной напильник, чтобы выровнять припой по форме панели. Более подробно о применении напильника можете прочитать в статье “рихтовка своими руками”. После обработки напильником, поверхность становится достаточно гладкой. Припой срезается напильником гораздо быстрее, чем прилегающая поверхность, поэтому периодически проверяйте форму припоя, чтобы не срезать лишнего. При обработке напильником, двигайте его диагонально вдоль ремонтной поверхности, приподнимая переднюю часть напильника. Если обрабатываете припой со свинцом шлифовальной бумагой, то лучше не использовать размер абразива меньше p80, чтобы пыль от шлифования не была слишком мелкой. Напильником нужно двигать наискосок, чтобы зазубрины и края не врезались в припой и не оставляли царапин. Обработка шлифовальной машинкой не должна производиться, так как образуется и поднимается в воздух токсичная пыль, которая вредна для здоровья, а также может прилипнуть к припою и вызывать коррозию.

- При необходимости, можно нанести тонкий слой шпаклёвки, чтобы довести поверхность до идеала. Для повышения адгезии перед шпаклеванием или грунтованием акриловым грунтом, на поверхность с нанесённым и обработанным припоем можно нанести эпоксидный грунт (см. статью “эпоксидный грунт, применение”).
Запайка отверстий
- Заваривание отверстий влечёт за собой тепловую деформацию (металл утолщается и стягивается), что может потребовать последующей рихтовки. Заделывание усиленной шпаклёвкой даст лишь временный результат. Припой может заполнить отверстие и послужить хорошей альтернативой сварке.
- При запайке большого отверстия, можно немного утопить металл вокруг него, чтобы припой его заполнил с запасом и держался не только на кромках отверстия. Также, можно рассверлить отверстие сверлом для зенковки по металлу нужного размера, либо обработать кромку отверстия круглым надфилем, чтобы она располагалась наискосок. Так припой будет лучше держаться на кромке.
- Также, при заполнении большого отверстия, можно на обратную сторону наклеить алюминиевый скотч, который послужит основой для припоя. Чтобы клеящий состав скотча не повлиял на качество ремонта, нужно вырезать из этого же скотча сегмент, размером чуть больше отверстия и наклеить на скотч (блестящей стороной наружу), который будет приклеиваться с обратной стороны отверстия. Для удобства можно пометить центр, который должен будет совпасть с отверстием. Таким образом, получится двойной блестящий скотч. Далее нужно наклеить всю эту аппликацию с обратной стороны отверстия. Чтобы не перегревать металл, можно лудить металл вокруг отверстия и его кромку паяльником, а также расплавлять припой тоже паяльником.
- Подобным способом можно ремонтировать сквозные отверстия от ржавчины, если вокруг них металл крепкий. Нужно предварительно обработать ржавые кромки отверстия и немного утопить металл вокруг.
- Мелкие отверстия можно заполнять припоем, который используется для пайки электроники.
- При заделке отверстий припоем, остатки флюса с обратной стороны панели могут вызывать ускоренную коррозию металла. Поэтому, остатки флюса лучше удалить горячей водой с содой как с лицевой, так и с обратной стороны.
[adsp-pro‑4]
Печатать статью
Ещё интересные статьи:
Используют ли сейчас лужение кузова автомобиля для защиты от коррозии?
Последний раз лудили Победу 60 лет назад. А современное поколение даже не знает что такое лужение. Ну типа того «слышал звон, но не знает где он»
набери в ютубе бмв -сборка с нуля и посмотри как их делают во всех подробностях.
Уважаемый «автомобилист по образованию». В СССР НИКОГДА не применяли лужение кузовов для увеличения срока службы. Это делалось для скрытия огрехов при штамповке панелей. Иногда до 20-ти кг олова наносили на детали кузова автомобилей «Победа». Стыдно не знать такие факты.
какие авто из немцев с лужеными кузовами?
Там где в ВИН коде стоит ZZZ- я такое слыхал.
в начале 90тых пришлось ставить заплаты на гнилого оппеля, с передних крыльев олово побежало, но ему в те годы было лет 20
Байки о лужёных кузовах возникли не на пустом месте несмотря на то, что ни одна автомобильная фирма не применяла лужение в качестве защиты от коррозии в массовом производстве. Дело в том, что до изобретения шпатлёвок в том виде, в котором мы их привыкли видеть, при кузовном ремонте использовалось свойство олова при нагревании становиться пластичным и вязким, как пластилин. Ещё раньше олово использовали и при выравнивании поверхностей кузова перед покраской и на заводских конвейерах! А считать, что капли олова, стекающие при нагревании кузовной детали горелкой при ремонте- признак лужёного кузова, неверно. Для защиты от коррозии применялись и применяются другие покрытия. Наилучшее качество даёт электрохимическое цинкование, которое применялось почти на всех производствах в Европе лет 20 назад. Сейчас большинство популярных у нас иномарок вообще не имеют антикоррозионного покрытия под краской- окрашивание производится по голому металлу. Сейчас попробую найти снимок Лансера 10 с небольшим кузовным повреждением и выложить для иллюстрации. <img src=»//otvet.imgsmail.ru/download/cacc6e6d56f9d208928afb95b95abdab_i-491.jpg» > Видно, что на машине, простоявшей несколько дней, металл, оставшись без краски, уже пожелтел от ржавчины. Ожидать от современных машин коррозионной стойкости кузова как у Ауди 80 уже невозможно- запланированный срок службы этих машин намного меньше, чем раньше.
Наверное с оцинкованным? Сейчас все немцы, даже самые дешёвые, идут с оцинкованными кузовами. Из старых немцев отличная оцинковка была у АУДИ
В холодную его!.. — журнал «АБС-авто»
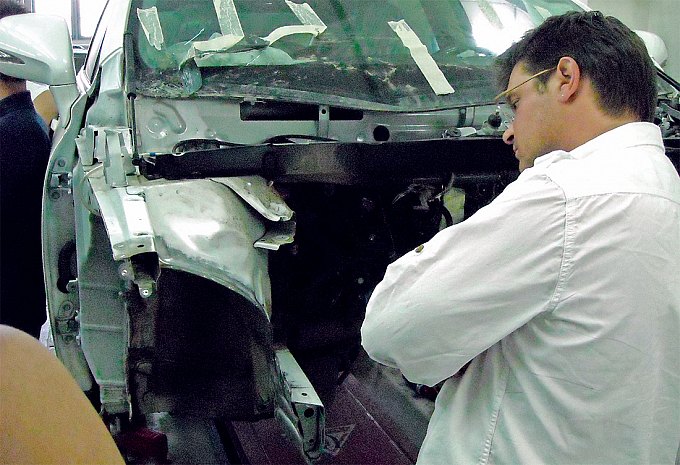
Оцинкованный кузов сегодня стал делом обычным. Это хорошо: цинковый слой повышает коррозионную стойкость панелей. Но вот беда, при кузовном ремонте это покрытие может быть нарушено. Как его восстановить? Промышленные способы оцинковки в условиях сервиса не подойдут…
Кто у нас активнее?
Почему цинк защищает стальной кузов? Давайте вспомним азы. Есть в химии такое понятие – электрохимический ряд напряжений металлов. Смотрим в таблицу: литий, калий… алюминий, цинк, хром, железо, никель, олово… серебро, платина, золото. Выше расположены более активные металлы, ниже – менее активные.
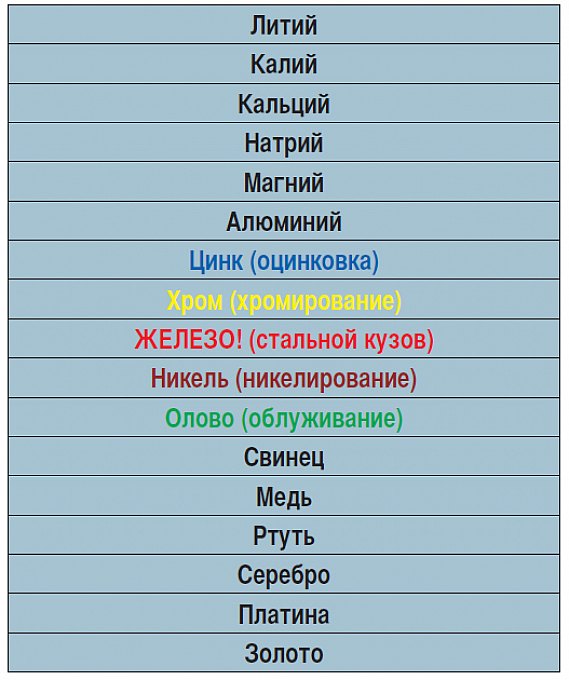
Если в какой-либо детали или узле имеется соединение двух металлов с различными потенциалами, то в присутствии электролита они образуют гальваническую пару. И чем дальше разнесены металлы в электрохимическом ряду напряжений, тем больше гальванический ток, и, соответственно, сильнее разрушения активного металла. Разрушаясь, он препятствует коррозионному поражению менее активного соседа.
Проиллюстрируем сказанное простым примером. Положим, в стальной автомобильной панели появилась медная заклепка. Смотрим в таблицу. Медь менее активна, значит коррозионное разрушение железа в месте соединения обеспечено. А если заклепка алюминиевая? Снова смотрим в таблицу. Здесь картина меняется: разрушаться будет алюминий.
Покрытия, выполненные из более активных металлов называют «безопасными», а из менее активных – «опасными». Поговорим о тех и о других.
Лудить или цинковать?
В народе до сих пор живет легенда: дескать, кузов «Победы» был покрыт оловом и никакая коррозия его не брала. Известны ее корни: мастера, ремонтирующие аварийные машины, использовали местный нагрев, орудуя паяльными лампами. И вдруг из-под пламени горелки начинало литься олово – много олова! Отсюда и пошла молва: кузов, дескать, весь облужен…
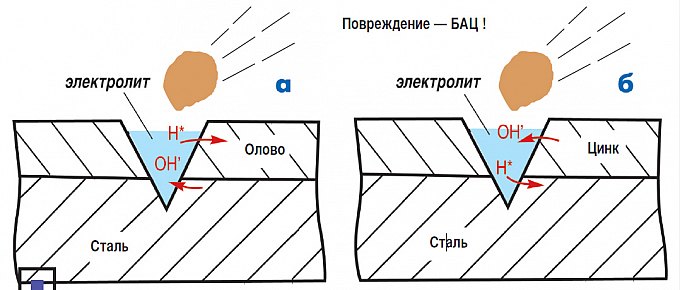
На самом деле все гораздо прозаичнее. Штамповая оснастка тех лет была несовершенной, и заводские технологии предусматривали рихтовку кузовных деталей. Остающиеся неровности выравнивали, заливая припоем. Особенно много олова было вблизи рамки ветрового стекла.
Так ли хорошо покрытие кузова оловом, как считают некоторые? Давайте разбираться. Коррозия всегда возникает на поверхности металла, а облуженная деталь ведет себя так, будто она изготовлена из олова. А оно само по себе очень стойко и практически не корродирует. Значит, и сталь под слоем олова находится в полной безопасности.
Но когда защитный слой получает повреждение, картина меняется. Между сталью (железом) и оловом мгновенно возникает гальваническая пара. А поскольку олово является менее активным металлом, сталь под воздействием гальванического тока начинает разрушаться.
Вспомним судьбу консервных банок, изготовленных из луженой жести. Все бывает хорошо, пока банку не поцарапаешь. А уж коль поцарапаешь, то луженая сталь в месте повреждения ржавеет гораздо быстрее нелуженой. Поэтому не надо говорить о «вечных луженых кузовах» – они вечные до хорошего удара острым камешком, которых на наших дорогах предостаточно.
Теперь о цинке. Все мы знаем, что кузовные панели многих автомобилей оцинковывают на заводах. Покрытие толщиной от 2 до 10 мкм обеспечивает прекрасную защиту от возникновения и распространения коррозионных поражений.
Это вам не олово: защищающий металл (цинк) в ряду напряжений расположен выше железа. Следовательно, и коррозия в поврежденном месте протекает иначе, чем с металлами, находящимися ниже. Гальваническая пара, само собой, тоже возникает, но разрушается уже не сталь, а цинк.
Почему же тогда цинковый щит не исчезает, не тает со временем? Исчезает и тает, но очень-очень медленно. Здесь есть особенность: цинк начинает активно разрушаться лишь при повышенных температурах. Вот почему в оцинкованных ведрах не рекомендуют кипятить воду. И тогда эти ведра живут долго – десятилетиями. И оцинкованные крыши тоже.
А вот мы его по-шведски…
Промышленные методы оцинковки, будь то горячее окунание или гальваника, не применимы в сервисных и гаражных условиях. Поэтому появление так называемых «препаратов холодного цинкования» оказалось для ремонтников весьма кстати.
Наносимые подобно грунтовке или краске, эти материалы образуют двойную защиту стальной поверхности: активную, как у промыщленной оцинковки, и пассивную, как у лакокрасочного слоя. Давайте познакомимся с ними на примере шведских препаратов Dinitrol 443 и Dinitrol 444.
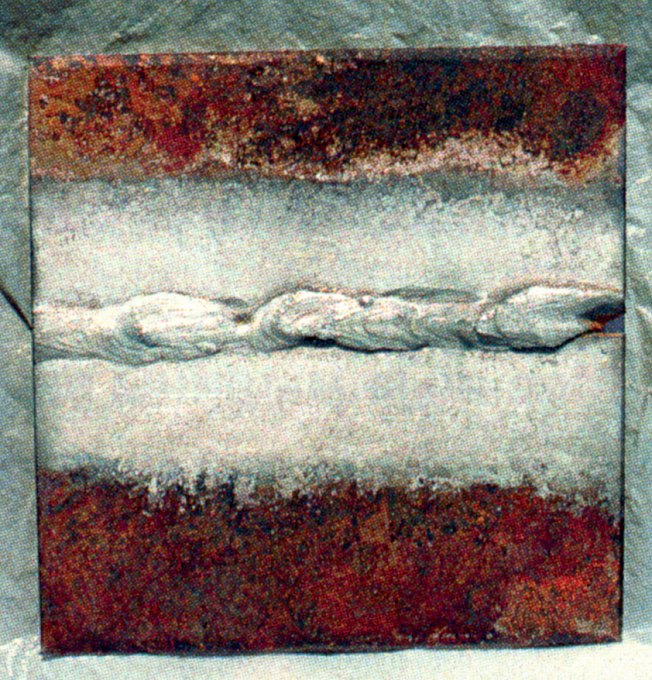
Они представляют собой готовые к применению жидкие однокомпонентные составы, содержащие технически чистый гальванический цинк. «Технически чистый» означает 99,995% Zn, что является очень высоким показателем для промышленного продукта. И вот такого, практически не содержащего примесей цинка, в препаратах Dinitrol 443 и Dinitrol 444 ни много, ни мало – 95%. Остальные 5% приходятся на синтетичсеские смолы, безопасный растворитель и некоторые специальные добавки.
Химики знают, что пороговая величина для активизации электрохимического щита – 92%, а тут все 95! Значит, при прочих равных условиях, пленку материала можно сделать тоньше, а материала потратить меньше – и это тоже относится к заслугам шведских технологий. А Dinitrol 444 содержит не только цинк, но и алюминий – тоже очень выгодный металл с точки зрения электрохимической защиты.
Нельзя не сказать и о размерах цинковых частиц – они ограничиваются величиной 3,5 мкм. Искушенные читатели вправе задать вопрос: «А этот диспергированный цинк не слипнется?». Действительно, любая суспензия может потерять однородность. Частицы соберутся в более крупные конгломераты – и прощайте технологические возможности и эксплуатационные козыри.
Что сказать на это? Суспензия, как таковая, может преподнести неприятный сюрприз, а вот Dinitrol 443 и Dinitrol 444 – нет. Им помогают те самые специальные добавки, о которых упоминалось выше. Они действуют поддерживают частицы цинка во взвешенном состоянии и предотвращают их слипание.
Очень важна роль синтетической каучуковой смолы, входящей в рецептуру препарата. Благодаря ей слой Dinitrol 443 или 444 обладает отменной адгезией. Но это еще не все: при высыхании он сохраняет эластичность, без проблем выдерживая механические и тепловые деформации.
Кстати, о тепле. А как обстоят дела с термостойкостью? А вот как: пленка препарата выдерживает температуры от –40 до +150 °С без потери эксплуатационных свойств. Так что, добро пожаловать и в Сибирь, и в окрасочно-сушильную камеру!
Что касается стойкости к химической агрессии, то «шведы» могут находиться в среде с рН от 5 до 10. Для тех, кто химию подзабыл, напомним: дистиллированная вода имеет рН=7. Значит, Dinitrol 443 и 444 выдерживает как щелочную, так и кислотную «баню».
И в заключение этого раздела отметим, что скорость разрушения активного цинкового слоя составляет от 1 до 6 мкм в год. Это гарантирует сохранность защиты в течение 25–50 лет в зависимости от толщины пленки и условий окружающей среды. Словом, на автомобильный век хватит.
Как наносим?
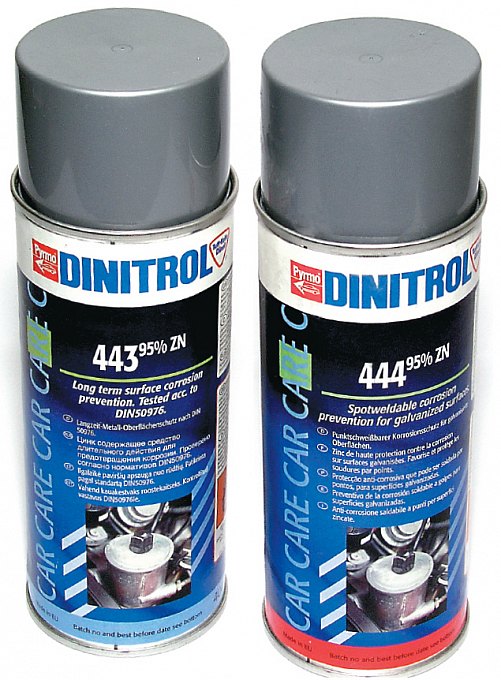
«Холодный цинк» марки Dinitrol может наноситься методом воздушного или безвоздушного распыления, кистью, валиком или окунанием.
В фирменной документации говорится, что нанесение препаратов не требует высокой квалификации работника. Это действительно так, особенно если воспользоваться аэрозольным баллончиком. А вот подготовка поверхности требует тщательности и профессионализма. Главное – обеспечить требуемую чистоту и шероховатость.
Препарат можно наносить на вертикальные и наклонные поверхности. Важно добиваться ровного слоя, без подтеков и пузырей. При толщине пленки 40 мкм расход составит 0,25 кг/м2. Высыхание длится 48 часов при комнатной температуре (на отлип – 10 мин). Для ускорения сушки деталь можно поместить в камеру и выдержать 30–60 мин при 60 °С. Повторный слой материала наносится через час. Полученную пленку можно окрашивать практически всеми видами ЛКМ.
Области применения новых шведских препаратов обширны: транспорт, мосты, дороги, тоннели, строительство, промышленные и городские объекты, гидросооружения, нефтегазовая промышленность. Не сомневаемся, что материалы Dinitrol 443 и Dinitrol 444 будут полезны всем мастерам кузовного ремонта.
Лужение кузова автомобиля — Разное
В первые годы массового автомобилестроения в нашей стране кузовное производство было далеким от идеального. Штампы деталей не гарантировали стопроцентную повторяемость, потому рабочим на конвейере приходилось вручную их доводить и подгонять. При этом нужно было тщательно скрыть технологические стыки и сварные швы. Зачастую кузов автомобиля приходилось собирать из нескольких элементов, поскольку не было возможности изготовить их из цельного листа металла.
Несмотря на значительную трудоемкость процесса, именно опайка кузова позволяла устранить перепады до 10мм, качественно выровнять зазоры и тем самым уменьшить процент выбраковки деталей кузова. Страна требовала автомобили, металла катастрофически не хватало, потому рихтовка, припой, зачистка и выравнивание кузова были единственным правильным выходом в сложившейся ситуации. Данная технология лужения кузова использовалась приблизительно до 60-х годов. Затем свинцовые припои плавно сменили пластизольные мастики, продержавшиеся на рынке машиностроения еще лет тридцать.
Прошли годы, но и сегодня большинство авторемонтников отдают предпочтение опайке кузова. И это несмотря на широкие возможности современной автохимии. Созданы специальные полиэфирные шпатлевки, которые отлично справляются с поставленными перед ними задачами. Зачем тогда проводить лужение кузова автомобиля?
Срывая покровы, открывая секреты…
Бесспорно, работать с полиэфирными шпатлевками при подготовке кузова к покраске – одно удовольствие. Нет ничего сложного – нанес, немного подождал, срезал лишний материал – и все готово! Но мало кто задумывается, что будет с поверхностью после полной полимеризации смолы. Представьте разогретую в кармане плитку шоколада в фольге. Что будет, если согнуть ее? Шоколад согнется, а вот фольга порвется. Приблизительно такая же картина ожидает и автовладельца через пару-тройку лет. Все дело в коэффициенте совместимости материалов, который нужно учитывать. Два используемых материала должны подходить друг другу, необходимо учитывать их возможные вибрации, изгибы и деформации. Для наглядного сравнения можно взять два железных прута, один покрыть припоем, а второй – шпатлевкой. Попробуйте их согнуть. Результат очевиден, но он хорошо демонстрирует преимущество использование в реставрации именно лужения, а не шпатлевки. Конечно, фанатизм в этом деле тоже не выгоден, выводить все плоскости и шероховатости припоем будет дорого, но в небольших количествах этот метод будет вполне оправдан.
Технология лужения кузова автомобиля
Предлагаем более детально рассмотреть процесс превращение дефективного кузова автомобиля в блестяще отремонтированный участок. Основная сфера применения технологии – это нерихтуемые места, ребра, сварочные швы и имеющиеся зазоры. Все это можно легко исправить и получить идеальную геометрию имея под рукой горелку и деревянный шпатель. Процесс лужения осуществляется поэтапно:
- Легкая шлифовка нужного участка абразивом и продувка сжатым воздухом. Во время этого осуществляется удаление имеющейся пыли и зерен наждачной бумаги.
- Подготовка поверхности – создание тонкой олово-свинцовой пленки, на которую уже лепится нужный слой. Использование в процессе лужение специальных паст значительно упрощает все процессы и не требует специальных умений и навыков.
- Кисточкой состав из банки наносится на поверхность, прогревается пропановой горелкой и протирается тряпкой. Из серо-матовой поверхность превращается в блестящую. На данном этапе важно не перегреть поверхность, чтобы не подгорела основа полуды, поскольку могут остаться пятна. Нагревание должно проходить, пока не заметите легкое вскипание. Не дожидаясь остывания, протираете поверхность тряпочкой.
- В специальном лоточке разогревается пруток припоя до размягчения. Консистенция должна быть как у сливочного масла. На подготовленную поверхность деревянной лопатой наносится припой, наращивается до нужной толщины. Затем слегка прогревается горелкой и повторно разглаживается. В течении последующих 1-2 минут с помощью рыхтовочной плиты поверхности придается необходимая форма. Если данного слоя припоя недостаточно, процесс повторяется заново до получения нужной толщины и требуемой формы.
- С помощью наждачной бумаги на шлифке или вручную деталь доводится до совершенства, уменьшаются риски и кратеры. После этого работают автомаляры – поверхность обрабатывается эпоксидными грунтами, тиксотропной шпатлевкой, грунтовкой-наполнителем и другими расходными материалами.